Top Shops Adapt, Evolve and Overcome
Like a stress test on steroids, the pandemic took full measure of Plastics Technology’s Top Shops as it exacerbated or revealed preexisting conditions around labor, the supply chain and more.
What is striking about talking to this year’s Top Shop’s honorees is how many of them were not satisfied to just hunker down and weather the challenges posed by COVID-19 but face them and emerge stronger. I guess it’s really just “continuous improvement” not “continuous improvement [except in a global pandemic].” [Ed. note: bookmark this URL—survey.ptonline.com/topshops—to participate in next year’s survey; the survey goes live Jan. 1, 2022].
Automate, Automate, Automate
We’ve already used this space to talk about how automation is in record-breaking territory, and conversations with Top Shops honorees reveal that many of these molders contributed to those historic sales. Faced with soaring demand and cratering labor prospects, molders leaned into automation.
“Our focus on automation was amplified as we found that new employee availability was negatively impacted by the unemployment bonus add-ons,” Eric Seebeck, operations manager at Top Shop honoree Modern Molding (Minneapolis) said. “While adding automation has always been part of our plan, the lack of applications for open production floor position was a catalyst to accelerate automation purchasing and implementation.”
How focused on automation is Modern Molding? You could find out by asking the employee dedicated to finding new ways to automate old jobs. “We have an automation engineer on staff whose sole focus is automating jobs to reduce or eliminate the need for labor,” Seebeck said. “The creativity we are seeing in end-of-arm tooling is significant.”
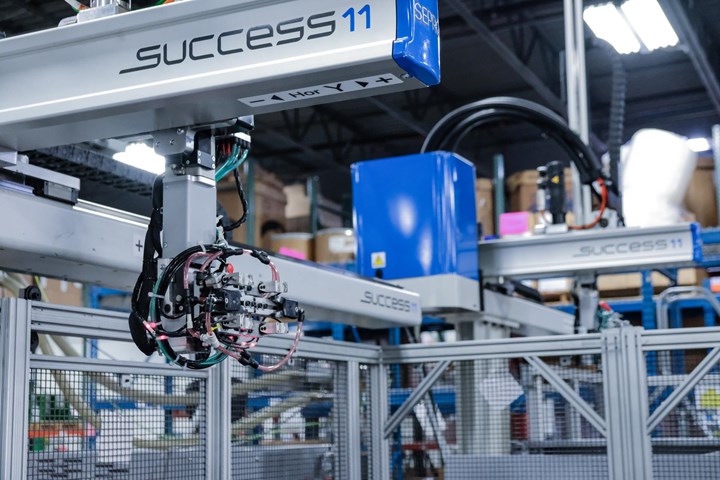
Modern Molding, which has an automation engineer on staff, increased its focus on automation during 2020.
Photo Credit: Modern Molding
For Martien Vloet, owner of Top Shops honoree Auralites (Fletcher, N.C.), the company’s pre-pandemic focus on automation was key, with the challenges posed by 2020 prompting even more investment. “We’re a highly automated, family-run shop with limited staff,” Vloet said, “that’s helped us keep operational during this time. The way our production lines are set up, we are capable of adding capacity without increasing labor.”
In 2020, the molder of polycarbonate candle cups added a repacking line to automate the process of transferring parts from large containers into smaller ones. “The addition of the line allowed us to reduce our dependence on unskilled labor, which has always been an inconsistent variable.”
At Plastikos (Erie, Pa.), General Manager and President Philip Katen said 2020 lead the molder and moldmaker to accelerate and expand its use of automation. “We eliminated any duplicate efforts or steps in our process and reduced or minimized other low value added manual activities,” Katen said. “That was all in an effort to provide some much needed relief to our team, as well as to better manage the range of staffing challenges.”
Here too, the company invested in more automation in 2020 to mechanize operations further. The company installed an automated vision-inspection system dedicated to supporting product quality on one of its most complex/highest volume medical device projects, while also adding automated part handling and packaging systems. Doing so allowed the company to reassign multiple production team employees to higher value-added jobs, according to Katen.
Mind the [Labor] Gap
The labor crunch that stimulated so much automation investment is not a new phenomenon, but it did intensify. “Finding skilled workers has been a problem for us for decades,” Matt Poischbeg, VP and GM of Top Shop honoree Sealect Plastics (Everett, Wash.) said, noting that very early in the pandemic, temp agencies that could normally help fill gaps ran out of workers to deploy—a situation that remains, according to Poischbeg. “This would cause production delays and machine down time, especially from June to December when we were working off tremendous back logs.”
But like other Top Shops, Sealect met the challenge, hiring workers from other industries—attracted in part to higher wages and an apprenticeship program—pushing the company to its highest ever headcount.
At Modern Molding, Seebeck says the company rolled out an internal apprenticeship program in its toolroom, while also implementing an injection molding technician training program to attract future techs.
At Plastikos, the company identified what roles could accommodate either 100% remote work or a hybrid approach to help retain workers, and it also expanded and enhanced its internal training programs. These included its Pennsylvania state-certified toolmaker apprenticeship program; its processor development program; its internal quality technician training; and its RJG Master Molder training.
“Prior to the pandemic, it was challenging to find and recruit experienced individuals, especially for the more technical positions,” Katen says. “If anything, COVID amplified the challenges that we face on the staffing front, both in terms of fewer qualified and available candidates.”
A Broken Supply Chain
The supply chain issues that still make headlines today started in the earliest days of the pandemic, representing yet another hurdle our Top Shops had to clear. “I have never in my 20 years at Modern Molding seen so much disruption and uncertainty in our supply chain,” Seebeck said. “Lead times have been extended dramatically, prices are constantly rising, and you often get late deliveries due to logistical bottle necks and high demand on limited transportation resources.”
Of the myriad difficulties posed by running a molding operation in a plague year, Auralites’ Vloet said one stood out above all others. “The biggest challenge we’ve had with the pandemic is how it has affected our supply chain with things costing more and taking longer to get,” Vloet said. “We simply increased our ordering timeframes and raised our prices as minimally as possible to keep our margins level.”
At Sealect, the supply chain issues were a teachable moment. “We believe the most important lesson from the pandemic is that we were depending too much on offshore manufacturing,” Poischbeg said. “If we keep doing that, our skilled workers will retire without passing on their knowledge and wisdom to a younger generation.”
To take part in next year’s Top Shops Benchmarking Survey, bookmark this URL—survey.ptonline.com/topshops. The survey goes live on Jan. 1, 2022.
Related Content
Annual Benchmarking Survey of Injection Molders Released
Plastics Technology Top Shops Benchmarking Survey provided both unanimous responses and divided results, but pervasive throughout is the sense of an industry still grappling with the aftermath of 2020’s global pandemic.
Read MoreTop Shops Time: Take the Injection Molding Benchmarking Survey Today
Plastics Technology has once again opened its annual survey of injection molders — participate in the anonymous benchmarking questionnaire today and reward your company with a free customized report.
Read MoreNew, Streamlined Injection Molding Benchmarking Survey Opens
The free, anonymous Top Shops Benchmarking Survey has been divided into core questions and modules, giving companies the option to complete a shorter questionnaire.
Read MoreMake Your Mark: Free Benchmarking Survey Remains Open
You have until April 30 to fill out your 2023 Plastics Technology Top Shops Benchmarking Survey, with no cost to you and a free analysis of your operations’ performance upon completion.
Read MoreRead Next
Top Shops 2020: Molding More from Less
Plastics Technology’s 2020 Top Shops benchmarking survey reveals that the most effective molders are, not surprisingly, the most efficient, accomplishing more than their peers from a smaller manufacturing footprint.
Read MoreTop Shops: Benchmarking Injection Molding in a Pandemic Year
At the start of 2021, as it does every year, Plastics Technology asked injection molders to look back on the year prior and take stock of their operations. The only difference this time: COVID-19.
Read MorePeople 4.0 – How to Get Buy-In from Your Staff for Industry 4.0 Systems
Implementing a production monitoring system as the foundation of a ‘smart factory’ is about integrating people with new technology as much as it is about integrating machines and computers. Here are tips from a company that has gone through the process.
Read More