Wittmann Opens Simulated Clean-Room Demo Facility
White walls, sticky floor tape, and even a startlingly realistic manikin gowned in a “bunny suit”—all intended to simulate the look and feel of a clean room in one alcove of the U.S. headquarters plant of Wittmann Battenfeld, Inc. in Torrington, Conn.
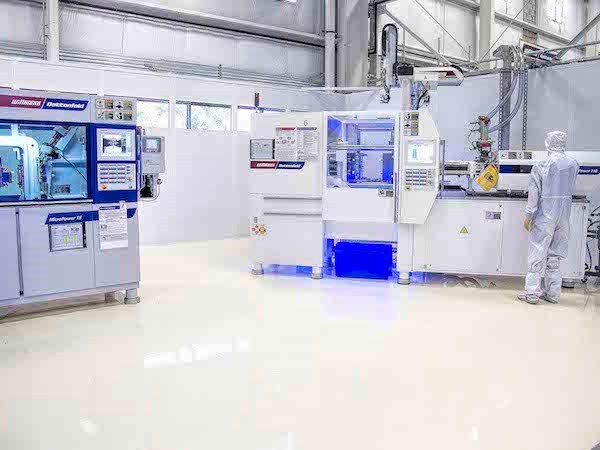
White walls, sticky floor tape, and even a startlingly realistic manikin gowned in a “bunny suit”—all intended to simulate the look and feel of a clean room in one alcove of the U.S. headquarters plant of Wittmann Battenfeld, Inc. in Torrington, Conn.
Given the intense interest in “clean” facilities for medical and electronics molding, the company pursued this approach to demonstrate the “clean-room-ready” molding equipment from its new Medical Products Group. These include specially equipped medical clean-room versions of its MicroPower, EcoPower, and SmartPower machines. “Our involvement in medical molding applications is increasing, and the addition of this new facility shows our continued commitment to the market,” said David Preusse, president.
The simulated clean room contains a fully enclosed MicroPower 15-ton micro-molding system, which can be equipped as a self-contained clean room; and a 110-ton, all-electric EcoPower SE (special clean-room edition) press with a W823 clean-room robot. An application for Wittmann 4.0 (the company’s version of Industry 4.0) is exemplified by a touchscreen terminal located outside the perimeter of the “clean room” demo area, that can provide full remote access to the molding machines, water-flow controllers, hot runners, robots, temperature-control units (TCUs), and dryers.
The clean-room demo facility was shown to the public for the first time at last month’s open house, which I attended along with around 300 visitors and some 20 industry partners, presenting 22 machine demonstrations, eight operating molding cells, and 36 technical presentations over two days. The open house also showed off the company’s recent expansion, involving the purchase of a 50,000-ft2 plant next door to the original building. Occupied in April, the new building is devoted to material-handling and auxiliary equipment.
Related Content
-
Innovative Micro-Molding From Minnesota Machine Shop
Machine shops are natural inventors, but not necessarily suited to supporting and marketing a product. This Minnesota shop with an invention related to micromolding will share it through licensing.
-
Slimmer All-Electric Press Debuts
NPE2024: A slimmed-down version of Engel’s all-electric, e-mac injection molding machine is among eight displays, which also include LSR micromolding, quick mold changes and a cube mold.
-
Precision Processing Requires Precision Equipment
Moretto offers plastics processors and micromolders for a broad suite of auxiliary solutions targeted specifically for precision processing.