Coiling System Features Automated Spool Removal
NPE2024: Designed for wire and cable and tubing, system is equipped with a Yaskawa cobot for automated spool removal.
Share
Reel Power Industrial, which makes reel and coiling systems for wire and cable and tubing, has introduced an Automatic Cut and Transfer system (ACT-26) for coiling and spooling up to 1,000 feet/minute. The ACT-26 can accommodate different coil sizes and configurations, providing flexibility to meet diverse production needs.
At NPE2024, the ACT-26 system is being showcased with a Yaskawa HC20DTP collaborative robot (cobot), demonstrating automated spool removal. This 6-axis HC20DTP cobot enables operation with or in close proximity to humans. Precision hand guiding facilitates easy programming for fast implementation of the cobot system, while a pinchless design featuring Power and Force Limiting (PFL) technology, constantly monitors force to quickly react to contact. Through-arm utilities hide cabling, including a Category 6 Ethernet cable. An IP67 rating enables use in harsh environments.
The ACT systems are said to offer quick return of investment when replacing manual machines with improved safety and one operator to run multiple lines. It can coil materials quickly and consistently, reducing production time and increasing output, and is designed to coil materials with precise measurements, resulting in consistent coil dimensions and minimizing material waste. This accuracy is crucial in industries where precise coil dimensions are required for downstream processes or product quality.
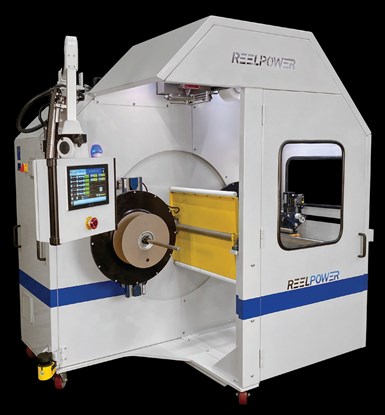
The ACT-26 systems are equipped with sensors and monitoring devices to ensure consistent quality throughout the coiling process. Data monitoring and analysis capabilities enables manufacturers to track production metrics, identify areas for improvement and optimize overall process efficiency over time.
Designed to be easily maintained, the ACT-26 is said to provide the lowest maintenance option on the market with no belts, gears or pulleys. It is designed for continuous operation with minimal downtime. Routine maintenance tasks can often be scheduled during planned downtime, minimizing disruptions to production schedules.
Special control features and a user-friendly, color operator touchscreen interface enables convenient operator controls with exceptional switchover reliability at high speeds.
Related Content
-
System Offers 'Lights Out' Mold-Channel Cleaning & Diagnostics
New system automatically cleans mold-cooling lines—including conformal channels—removing rust and calcium, among other deposits, while simultaneously testing for leaks, measuring flow rate and applying rust inhibitor.
-
Automation in Thermoforming on the Rise
Equipment suppliers’ latest innovations exemplify this trend driven by factors such as labor shortages, higher-speed thermoformers and tighter quality control.
-
Drones and Injection Molding Ready for Takeoff
Drones and unmanned aerial vehicles (UAV) are approaching an inflection point where their production volumes — and functionality — will increasingly point to injection molding.