Mini Control Offers Central Conveying for Small Plants, Work Cells
NPE2024: System supports vacuum conveying systems with up to three vacuum pumps and a maximum of up to 12 receivers.
Share
The new SmartFLX Mini conveying control from Conair is sized for the needs of small processing plants or work cells that need a centralized conveying control with powerful standard features, easy installation and an economical cost. Based on the system architecture, logic and field-proven components developed for Conair’s full-sized SmartFLX conveying control, the SmartFLX Mini supports vacuum conveying systems with up to three vacuum pumps and a maximum of up to 12 receivers.
Though the SmartFLX Mini is scaled to fit smaller operations, it offers a range of important central-conveying features. Configuring conveying system equipment to utilize these features is simple because of “predefined” I/O panel slots. For example, receivers may be configured for standard, multisource or ratio loading, while sources can be configured to operate as pocket valves, purge valves or as a granulation device/common line valve. Other important conveying features include FIFO priority loading; load-and-hold, fill-sensor operation; and VNC remote connections. Pump configuration options include idle mode and dust-collector controls.
The SmartFLX Mini also connects easily with SmartServices, Conair’s cloud-based Industry 4.0 platform, which provides a “dashboard” of auxiliary equipment status for centralized monitoring and control.
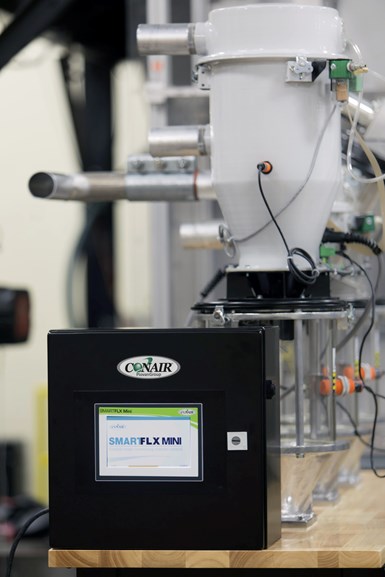
High-end security and communications features — multilevel password security, keystroke logging and multilingual displays — are also standard and easily accessible through a 7-in., color touchscreen HMI that utilizes Conair’s “common control” interface. The common control interface shares the same look and feel as other Conair auxiliary equipment controls. It also offers a context-sensitive Help system that provides specific instructions for each command screen, helping even novice operators to access and use control capabilities with confidence. All control functions operate atop a new PLC processor and software, with all system intelligence centralized in the system’s main panel for easy, single-point software upgrades.
Like the larger and more powerful SmartFLX control, the new SmartFLX Mini features a two-channel system architecture for maximum conveying reliability. The first, high-speed channel prioritizes material conveying requests and equipment diagnostic signals to ensure timely material movement and provide real-time equipment status. It uses the advanced Powerlink protocol, which supports crystal-clear data communications in noisy industrial environments while operating at speeds far faster than older communication protocols. The second channel, which carries non-time-critical equipment signals and system reports, utilizes the proven Modbus communication protocol.
Related Content
-
Safety, Recycling, and Compounding Trends Bring New Opportunity to 70-Year-Old Company
NPE2024: Vac-U-Max presents pneumatic conveying solutions for powdered materials.
-
Radar Level Sensor Streamlines Bulk Material Inventory Management
NPE2024: The NCR-86 is designed to ensure rapid data updates, enhancing efficiency in inventory management.
-
Conair: Going All In on AI
Conveying with Optimizer, Conair’s new AI-based conveying technology stands to be a true game changer for plastics processors.