Cadillac Products Debuts New Brand Line of Medical Gowns
As PPE demand rises, automotive supplier and packaging manufacturer Cadillac Products steps-up with new line of extruded medical gowns.
A new line of single-use medical-grade gowns is being produced by Troy, Mich.-based automotive supplier and packaging manufacturer Cadillac Products, Inc. (CPI), as demand for PPE (Personal Protective Equipment) increases. The company’s ProTec-USA division has debuted the new line of medical gowns which are designed to maintain the integrity of comfort, flexibility and safety for all end users' needs, while also conforming with AAMI PB70 Barrier Level 1, 2 and 3 standards, withstanding water spray and water penetration under constant contact with increasing pressure.
The company is currently producing more than 400,000 medical gowns per month under the EZDoff brand, with the ability to scale up to meet the market needs for healthcare workers nationwide.
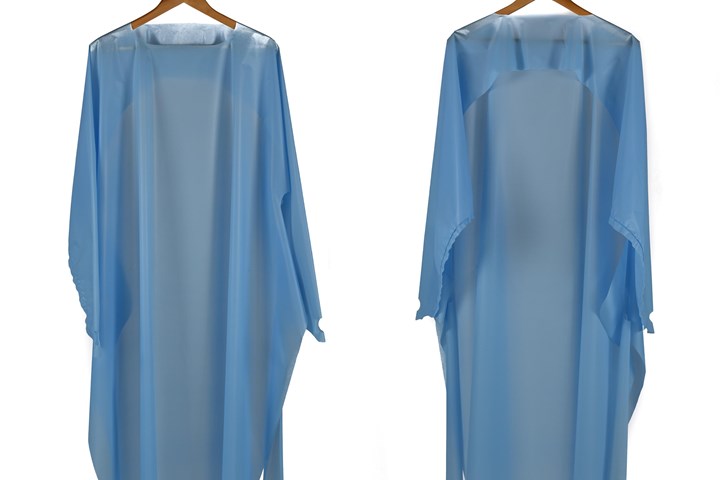
Company sources confirm that the ProTec-USA EZDoff gowns, are extruded of a custom PE blend with a taffeta grain applied to the A surface via tooling at the Cadillac Products’ packaging manufacturing site in Paris, Ill., on typical packaging film extrusion equipment. The film rolls are then sent to the Troy location where patterns are cut into single-use disposable gowns. These are single layer film extrusions, but the company is looking into the possibility of expanding the product line to include SMS (Spunboutn/Meltblown/Spunbond PP/PE or SMMS (Spunbond/Meltblown/Meltblown/Spunbond) PP/PE.
EZDoff gowns are available for order immediately, with quick turnaround times for delivery and without risk of shortages and delays. Said spokeperson at CPT Don Lowe, “Our team recognized the dire needs for reliable, American-made PPE that brave frontline and essential workers had in the early stages of the pandemic and made it a mission to pull together to voluntarily engineer and distribute gowns to properly protect them.”
EZDoff gowns are available for order immediately, with quick turnaround times for delivery and without risk of shortages and delays. Said spokeperson at CPT Don Lowe, “Our team recognized the dire needs for reliable, American-made PPE that brave frontline and essential workers had in the early stages of the pandemic and made it a mission to pull together to voluntarily engineer and distribute gowns to properly protect them.”
The manner in which the gowns are donned and doffed in sequence with other PPE is an important consideration when selecting optimal PPE coveralls, as the ease or difficulty with which PPE is put on and removed. EZDoff gowns are engineered to maintain effectiveness and mitigate potential self-contamination during doffing of contaminated PPE. In essence, the wearer doesn’t have to touch the outer surface of the EZDoff gown to remove it, thereby, protecting against consequential contamination by the wearer.
Product benefits and features include:
▪ - One size fits all--eliminates the needs to manage various size inventory
▪ Perforated rear yoke--enables safe, easy doffing of gowns
▪ Sleeve with thumb loop--ensures full arm and wrist protection, simultaneous glove donning
▪ Apron closure and open-back design--maintains a cool temperature for users during work performance
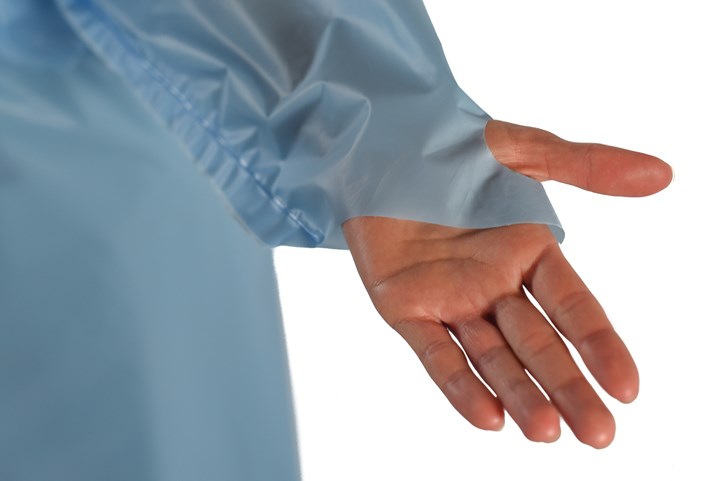
In addition to being an approved supplier to several United States governmental agencies such as the Department of Defense and the Department of Veterans Affairs, ProTec-USA was recently awarded a grant from Oakland County for the “Saving Business, Saving Lives” program, which underscores its steadfast commitment and ability to engineer high-quality PPE products in the fight against COVID-19 and beyond. The company has invested in upgrades and enhancements to production lines and equipment at its Troy, Mich. facility, where production levels allow the company to manufacture and distribute more than 92,000 EZDoff gowns per week with the ability to add capacity as needed to meet market needs.
Said Lowe, “The advantage of American manufacturing is the ability to understand the market, pivot to make changes quickly, and continually meet the needs of customers as a reliable, domestic-based resource to onshore their supply chain.”
Related Content
Consistent Shots for Consistent Shots
An integral supplier in the effort to fast-track COVID-19 vaccine deployment, Retractable Technologies turned to Arburg and its PressurePilot technology to help deliver more than 500 million syringes during the pandemic.
Read MoreMedical Tubing: Use Simulation to Troubleshoot, Optimize Processing & Dies
Extrusion simulations can be useful in anticipating issues and running “what-if” scenarios to size extruders and design dies for extrusion projects. It should be used at early stages of any project to avoid trial and error and remaking tooling.
Read MoreAllegheny Performance Plastics to Enter Health Care Sector
The custom molder has secured multiple projects in health care and will be adding cleanroom and white-room spaces, as well as injection molding machines, in support.
Read MoreKrones Acquires Netstal
Krones adds PET preform injection molding to its bottle blowing and filling capabilities, as well as cap molding and expansion into medical, food and other markets.
Read MoreRead Next
Making the Circular Economy a Reality
Driven by brand owner demands and new worldwide legislation, the entire supply chain is working toward the shift to circularity, with some evidence the circular economy has already begun.
Read MoreFor PLASTICS' CEO Seaholm, NPE to Shine Light on Sustainability Successes
With advocacy, communication and sustainability as three main pillars, Seaholm leads a trade association to NPE that ‘is more active today than we have ever been.’
Read More