Cover for On-Board Battery Charger Made of Nylon 6
Lanxess’ highly-reinforced Durethan BKV50H3.0 proven in new large-scale electric vehicle applications in place of nylon 66.
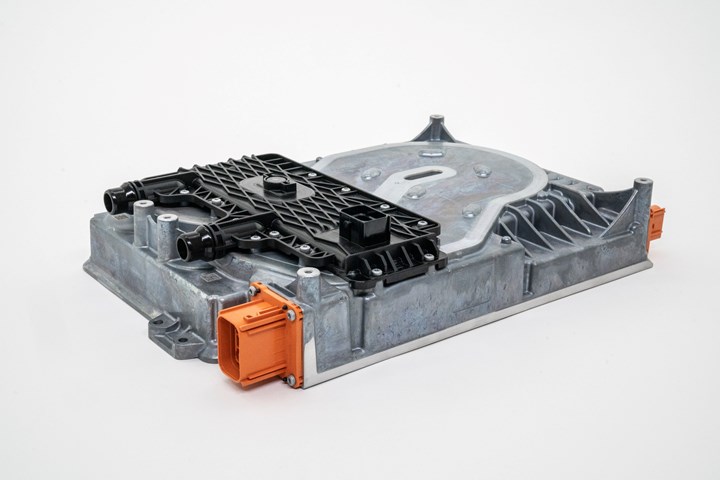
A highly-reinforced nylon 6 from Lanxess has proven itself for larger-scale electric vehicle applications. The cover for an on-board battery charger that is used in an all-electric compact vehicle made by a German car manufacturer is composed of Durethan BKV50H3.0 reinforced with 50%/wt of short glass fibers. The manufacturer of the system consisting of the cover and charger is Leopold Kostal GmbH & Co. KG, a global system supplier of automotive, industrial and solar electrics as well as electrical connector systems.
This large-scale application underlines the fact that nylon 6 compounds do not necessarily have to be hydrolysis-stabilized to be used in cooling applications with glycol-water coolants in electric vehicles. Says technical key account manager Bernhard Helbich, “We assume that in the future, nylon 6 products of this type will become very common in the mass production of covers and other thermal management components for electric vehicles. That is especially the case for applications such as fluid connectors or control units in the cooling system.”
Plastic components in the cooling circuit of combustion engines have long been a domain nylon 66., due to its high resistance to hot coolants such as water-glycol mixtures. However, the requirements in the thermal management of purely electric powertrains are shifting toward lower temperatures. For all-electric vehicles, the long-term thermal resistance of nylon 6 compounds to water-glycol mixtures is sufficient for most of the parts, even for the significantly longer stressing times in some cases.
As such, the new cover permanently withstands temperatures of up to 752 F during vehicle operation without any problems, and burst loads of up to 10 bar are achieved. Long-term tests on test specimens also revealed that the mechanical properties of the compound in water-glycol mixtures hardly diminish even after 1500 hours of storage at 230 F and a pressure of 1.5 bar. As a result, the material meets the technical requirements of a major German carmaker for water-cooled components of electric vehicles.
At around 11.42-in. long and 4.4-in wide, the cover has a considerable flange length. The cover, together with a seal, is screwed to the aluminum housing of the charger. The high degree of strength and stiffness shown by the nylon 6 compound ensures that the cover meets the strict leak tightness requirements. Helbich comments, “To that end, we optimized the mechanical component properties in close collaboration with Kostal and, by simulating filling, we determined how minimum values for shrinkage and warpage can be achieved in injection molding processing. These services are part of our HiAnt service package, with which we support our project partners at all stages of component development.”
The cover also exhibits other material advantages of Durethan BKV50H3.0. It is easy to process and can be injection-molded at high injection speeds, which benefits short, and therefore economical, cycle times. Furthermore, its copper-free H3.0 thermal stabilization does not result in electrical corrosion occurring on metallic parts in the cooling circuit. Another of the compound’s virtues is that it is resistant to media typically found in vehicle operation, such as oils, greases, battery electrolyte, and road salt.
Related Content
Prices Bottom Out for Volume Resins?
Flat-to-down trajectory underway for fourth quarter for commodity resins.
Read MoreWhat is the Allowable Moisture Content in Nylons? It Depends (Part 1)
A lot of the nylon that is processed is filled or reinforced, but the data sheets generally don’t account for this, making drying recommendations confusing. Here’s what you need to know.
Read MoreScaling Up Sustainable Solutions for Fiber Reinforced Composite Materials
Oak Ridge National Laboratory's Sustainable Manufacturing Technologies Group helps industrial partners tackle the sustainability challenges presented by fiber-reinforced composite materials.
Read MoreThe Fantasy and Reality of Raw Material Shelf Life: Part 1
Is a two-year-old hygroscopic resin kept in its original packaging still useful? Let’s try to answer that question and clear up some misconceptions.
Read MoreRead Next
People 4.0 – How to Get Buy-In from Your Staff for Industry 4.0 Systems
Implementing a production monitoring system as the foundation of a ‘smart factory’ is about integrating people with new technology as much as it is about integrating machines and computers. Here are tips from a company that has gone through the process.
Read MoreLead the Conversation, Change the Conversation
Coverage of single-use plastics can be both misleading and demoralizing. Here are 10 tips for changing the perception of the plastics industry at your company and in your community.
Read MoreSee Recyclers Close the Loop on Trade Show Production Scrap at NPE2024
A collaboration between show organizer PLASTICS, recycler CPR and size reduction experts WEIMA and Conair recovered and recycled all production scrap at NPE2024.
Read More