JSW and iMFLUX Announce Partnership
The collaboration agreement would integrate iMFLUX processing software on the full line of JSW America presses.
Japan Steel Works America Inc. (JSW) and iMFLUX, a subsidiary of P&G, have partnered to integrate iMFLUX processing software on the full line of JSW America presses, giving JSW customers access to the iMFLUX low-constant-pressure molding platform on its high-speed all-electric presses.
iMFLUX’s injection molding technology enables reduced tonnage requirements and lower energy usage, while adapting to material variation in real time. To mark the agreement and display the technology, iMFLUX is hosting a virtual event on July 20, showcasing a JSW J350ADS-460H-Ultra Spec injection molding machine utilizing iMFLUX.
Held at iMFLUX’s Innovation and Education Center in Hamilton, Ohio, the event will show the program’s ability to automatically adjust to blocked cavities and material changes. On that front, the company will shift from a virgin SR549 polypropylene with a melt flow index of 11, to Sustainable Resin’s post consumer plastic with a melt flow index of 25.
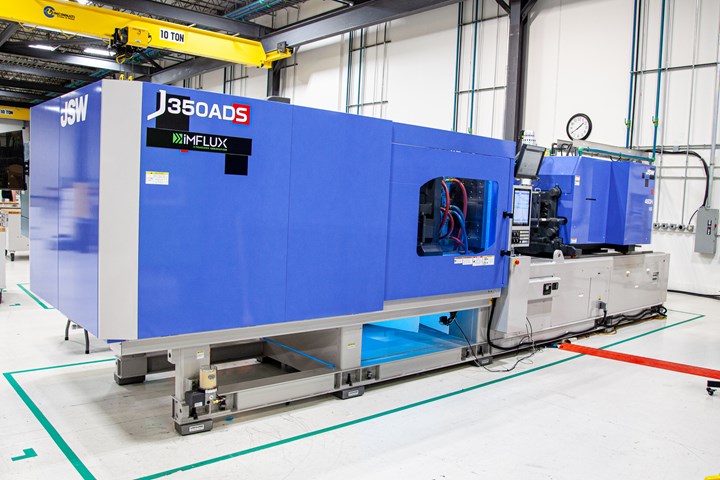
In a July 20 virtual event, iMFLUX will showcase a JSW J350ADS-460H-Ultra Spec injection molding machine utilizing its constant low-pressure molding technology.
Related Content
-
What to Look for in High-Speed Automation for Pipette Production
Automation is a must-have for molders of pipettes. Make sure your supplier provides assurances of throughput and output, manpower utilization, floor space consumption and payback period.
-
Understanding the Effect of Pressure Losses on Injection Molded Parts
The compressibility of plastics as a class of materials means the pressure punched into the machine control and the pressure the melt experiences at the end of fill within the mold will be very different. What does this difference mean for process consistency and part quality?
-
Is There a More Accurate Means to Calculate Tonnage?
Molders have long used the projected area of the parts and runner to guesstimate how much tonnage is required to mold a part without flash, but there’s a more precise methodology.