Nebraska Community College Heeds PPE Call in Cororavirus Crisis
Molds 550 pieces of headgear for face shields in the same time it took to produce one on a 3D printer. College has donated 11,500 completed face shields for use throughout Nebraska and 800 to Columbus Community Hospital, a local facility.
The injection molding program at Central Community College (CCC) in Nebraska helped meet the demand for personal protective equipment during the COVID pandemic. In particular, there was a great need for headgear pieces for face shields to be produced at a much higher rate than 3D printing. Utilizing on-campus injection molding machines, program director Ben Wilshusen was able to produce 550 pieces of headgear in the same time it took to produce one on a 3D printer.
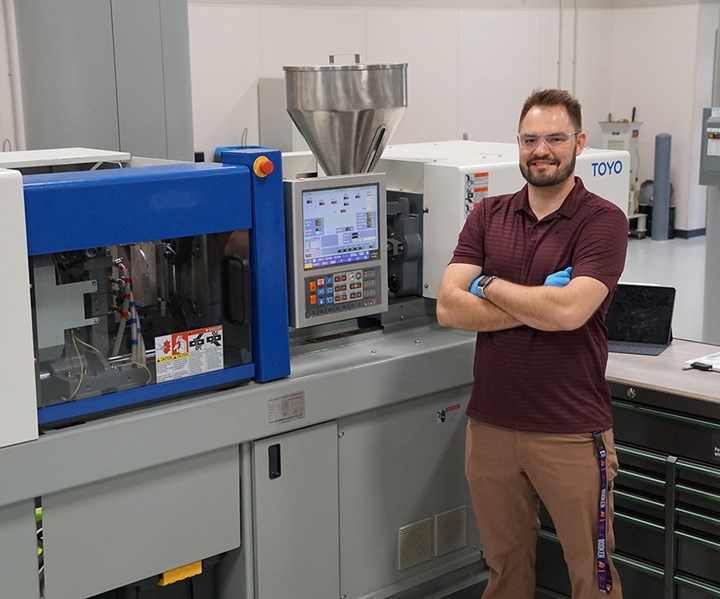
CCC partnered locally with Jimko Machine for the project as well as custom molder Majors Plastics of Omaha. Wilshusen produced the headgear pieces on two machines—a Toyo Si-55-6 (55 ton) and an Arburg Allrounder 370 E golden Electric (55 ton). Both presses were donated on consignment from the machine builders. The material used to make the headgear pieces was HIPS regrind donated by Majors Plastics. An aluminum MUD mold insert was utilized with the cavity machined by Jimko Machine. The waterline and ejector system was machined on campus by advanced manufacturing design technology coordinator Darin Skipton.
Once the headgear pieces were created, 100 were boxed along with shields, elastic bands and assembly instructions. CCC staffers and even a couple of student-athletes helped pack the boxes, which were then shipped to various health departments in Nebraska. CCC has donated 11,500 completed face shields for use throughout Nebraska and 800 to Columbus Community Hospital, a local facility.
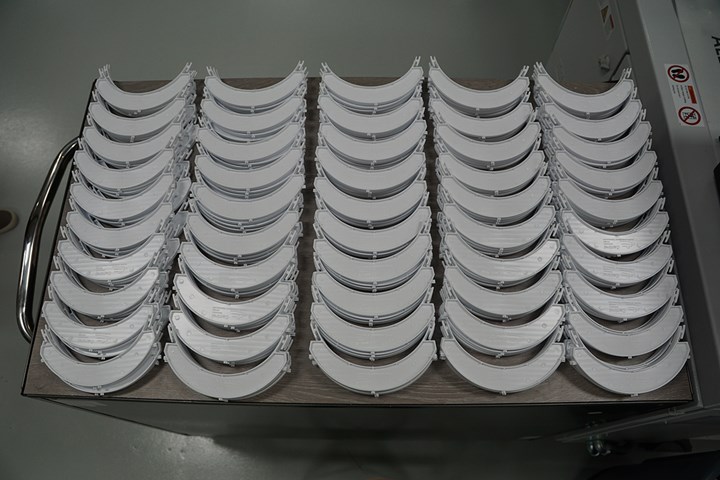
Face shield head gear molded of HIPS by Nebraska Central Communnity College Program.
With the assistance of a National Science Foundation grand, CCC’s plastic injection molding program is in development and scheduled to launch in fall 2021.

Related Content
-
A Systematic Approach to Process Development
The path to a no-baby-sitting injection molding process is paved with data and can be found by following certain steps.
-
Using Data to Pinpoint Cosmetic Defect Causes in Injection Molded Parts
Taking a step back and identifying the root cause of a cosmetic flaw can help molders focus on what corrective actions need to be taken.
-
Three Key Decisions for an Optimal Ejection System
When determining the best ejection option for a tool, molders must consider the ejector’s surface area, location and style.