Planned Demonstration Facility Will Produce Acrylonitrile from Bio-based Glycerol
Trillium announced its partnership with Zeton to design its demonstration facility for converting plant-based glycerol into acrylonitrile.
Trillium Renewable Chemicals announced plans to scale up its process for converting glycerol to acrylonitrile, with Zeton to design the demonstration facility. Trillium’s plans, dubbed “Project Falcon,” are informed by its operation of a pilot facility in West Virginia.
Acrylonitrile is used in the production of a variety of materials, including acrylonitrile butadiene styrene (ABS) plastic, carbon fiber, nitrile butadiene rubber and acrylamide. Acrylonitrile is typically formed by ammoxidation of propylene, derived from oil or natural gas products. In contrast, Trillium’s process is fed with glycerol derived from plants.
“We take the good things about the Sohio (ammoxidation) process, which are the high yields and good economics, and combine it with a sustainable raw material. The end result is a drop-in material, chemically identical to what is being made today, with a much lower carbon footprint,” says Corey Tyree, CEO at Trillium.
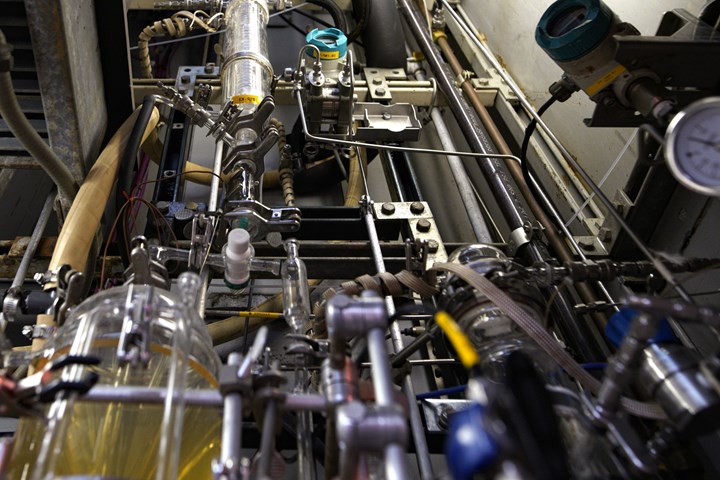
Processing equipment at Trillium’s pilot plant in West Virginia. Photo Credit: Trillium Renewable Chemicals
According to Trillium, the process reduces the carbon footprint of acrylonitrile by 70%. The company will market its product as a solution to reaching sustainability targets without the adjustments needed to adapt processes to alternative and recycled materials.
“The clock can run out on you as you’re trying to not only make a new material but also build up an entire raw material and downstream supply chain to accommodate that new material. I really believe that the drop-in approach is the more practical approach to meeting these timelines, because you don’t have to re-engineer the supply chains” Tyree says.
The demonstration facility will produce enough product for Trillium to provide to customers for analysis and qualification, as a final step before commercialization. The facility is expected to be complete in 2024 and operational in 2025. Site selection is expected to be announced by the end of 2023.
Related Content
-
NPE2024 Materials: Spotlight on Sustainability with Performance
Across the show, sustainability ruled in new materials technology, from polyolefins and engineering resins to biobased materials.
-
Prices Up for All Volume Resins
First quarter was ending up with upward pricing, primarily due to higher feedstock costs and not supply/demand fundamentals.
-
What is the Allowable Moisture Content in Nylons? It Depends (Part 1)
A lot of the nylon that is processed is filled or reinforced, but the data sheets generally don’t account for this, making drying recommendations confusing. Here’s what you need to know.