SPE 2023 Automotive Awards Highlight ‘Firsts’ and Emerging Technologies
Nods given to several ‘firsts’ as well as rapidly emerging technologies with sustainability nearly always a major theme.
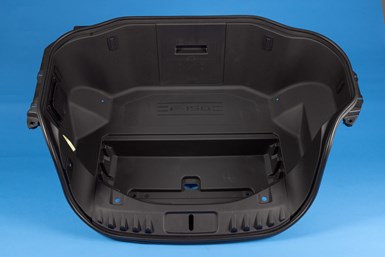
The 52nd annual Society of Plastics Engineers (SPE) Automotive Division Blue Ribbon Automotive Innovation Awards once again celebrated several “firsts” among eight categories, which included innovations in last year’s added categories of Electric & Autonomous Vehicle Systems and Aftermarket & Limited Edition/Specialty Vehicles and an expanded and renamed Sustainability category. As has been the case for the last several years, thermoplastics and thermoplastic composites led by far in all categories, with other hybrid thermoplastic/thermoset processes also included.
The 2023 grand award and category winner, body interior, was the mega bin/frunk which appears in Ford Motor’s battery-electric 2024 F-150 Lightning. This ‘first’ entailed converting from compression molded painted SMC to mold-in-color injection molded PP-LFT (40% glass) to produce the industry’s largest Class A composite frunk. Produced with Celanese’s Celstran PP-GF40 by Cascade Engineering, this conversion resulted in a 48% mass reduction, a 37% cycle time reduction, while eliminating the cost and environmental burden of paint. Also, seal interfaces were improved, secondary routering of holes is no longer needed, and the frunk is fully recyclable at end of life. A 4000-ton injection press and a tool equipped with a 16-drop hot runner system are used to mold parts.
Related Content
-
‘Monomaterial’ Trend in Packaging and Beyond Will Only Thrive
In terms of sustainability measures, monomaterial structures are already making good headway and will evolve even further.
-
Part 3: The World of Molding Thermosets
Thermosets were the prevalent material in the early history of plastics, but were soon overtaken by thermoplastics in injection molding applications.
-
How to Optimize Injection Molding of PHA and PHA/PLA Blends
Here are processing guidelines aimed at both getting the PHA resin into the process without degrading it, and reducing residence time at melt temperatures.