Automation: Kit Turns Cobots into Autonomous Bin Pickers
Universal Robots says ActiNav allows its cobots to autonomously extract parts from a bin and place them with precision and orientation.
Universal Robots (UR) says its ActiNav kit can turn cobots into autonomous bin pickers able to service machine-tending applications. UR notes that automated bin picking typically requires a massive amount of integration and programming, resulting in systems that are usually only focused on the vision aspect of bin picking. If the system needs to go past picking parts to placing them—particularly if the process isn’t just dropping parts into a box or tote but accurately inserting them into a fixture—hundreds of lines of additional programming can be required.
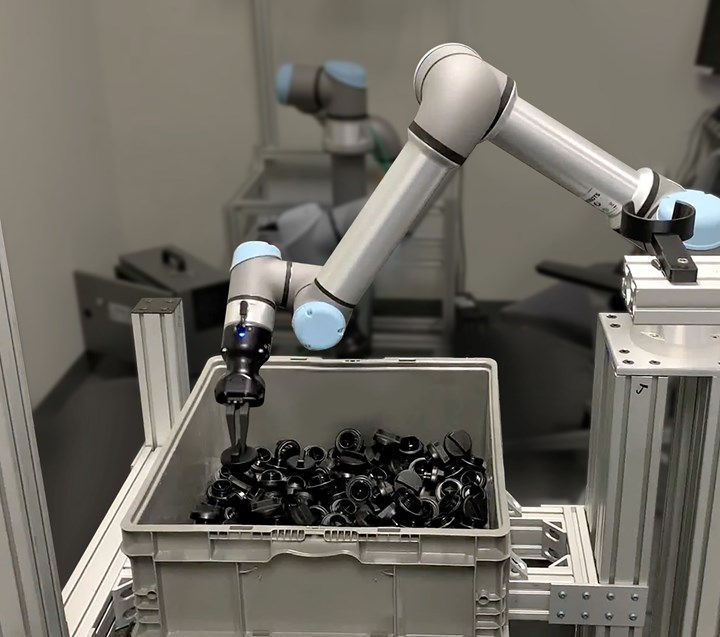
Universal Robots ActiNav kit turns collaborative robots into autonomous bin pickers.
ActiNav, however, requires no vision or robotic programming expertise, but is instead based on a “teach-by-demonstration” principle using a six-step, wizard-guided setup process integrated into the UR cobot teach pendant. The ActiNav kit combines real-time autonomous motion control, collaborative robotics, vision and sensor systems. Working with UR’s UR5e and UR10e e-Series cobots, ActiNav can be integrated with a UR+ component or user-defined end effector, and application-specific frame or fixture as needed. The kit includes the Autonomous Motion Module (AMM) and ActiNav URCap user interface software, along with a choice of 3D sensors.
Automating machine tending stations typically involves using trays, bowl feeders or conveyors to get the parts to the machine—a step bypassed by ActiNav. Many of these parts are already in bins, and ActiNav allows the cobot to pick directly from there and place them into the machine, minimizing floor space used and reducing the need for part-specific tooling.
ActiNav uses a structured light scanner to take an image of the bin and generate a point cloud. The technology than applies a CAD-matching algorithm that integrates CAD models of the robot, part and end effector, creating a “clearance shape” so the arm can move in and out of the bin without colliding with anything.
In a virtual press conference introducing the technology, Eric Andersen, ActiNav product manager, said the system is focused on machine tending and servicing secondary operations like drilling, tapping, polishing, grinding, deburring and CNC machining. Andersen noted that there are millions of machines that require some kind of tending, but there is also a labor shortage. ActiNav would especially target jobs that fall under the “three Ds”, according to Andersen: dirty, dull or dangerous, which are especially difficult to fill.
For processes where the cycle time ranges from 10 to 90 seconds, the operator typically has to remain at the machine, spending most of that time idle. For around $100,000, Andersen said ActiNav could allow that worker take on more value-added tasks than bin picking, with ROI possible in as little as 18 months for a 2-shift operation. Ideal target parts would be two fists in size or less. For very small parts, technologies like bowl feeders would make sense, while for very large parts, with longer cycles, conveyors or trays are more applicable.
Related Content
-
Drones and Injection Molding Ready for Takeoff
Drones and unmanned aerial vehicles (UAV) are approaching an inflection point where their production volumes — and functionality — will increasingly point to injection molding.
-
Real-Time Production Monitoring as Automation
As an injection molder, Windmill Plastics sought an economical production monitoring system that could help it keep tabs on its shop floor. It’s now selling the “very focused” digital supervisor it created, automating many formerly manual tasks.
-
Cobot Creates 'Cell Manufacturing Dream' for Thermoformer
Kal Plastics deploys Universal Robot trimming cobot for a fraction of the cost and lead time of a CNC machine, cuts trimming time nearly in half and reduces late shipments to under 1% — all while improving employee safety and growth opportunities.