Automation: System Promises Greater Flexibility for Molded Packaging
Integrated automation system can accommodate multiple molds and cavitation, from one to 48, allowing it to adapt to changing applications and volumes.
Muller Technology Colorado, the former CBW Automation, has launched the M-Line integrated robot and automation system, which offers greater flexibility for its users, a departure from past systems that were highly application/tool specific.
The M-Line, which was jointly developed by Muller Technology Colorado and its sister company Muller Technology Conthey of Switzerland, can accommodate various mold types with differing cavitation, and pitch between those cavities, ranging from single to 48 cavities. Instead of more rigid automation systems that are designed for certain molds with specified cavitation, the M-Line can adapt to market changes and shifting production volumes.
The M-Line has three models suited for various injection molding machine sizes. A spokesperson told Plastics Technology that those sizes are based on the reach of the robot arms and range from small (300 to 500 tons) to medium (600 to 850 tons) to large (850 to 1000 tons). Muller says the M-Line features low-cost, flexible end-of-arm-tooling (EOAT) that can be changed quickly. Built on a single frame that doesn’t require assembly and has a small footprint, the M-Line is also motorized eliminating pneumatics with servomotors, which reduces overall energy consumption. Servomotors, which can have a lifespan that’s 10 times that of pneumatics, also reduce maintenance. Muller notes that using servomotors also creates an extended period of accumulation time on the conveyor of up to one hour. That can ultimately reduce the number of packers needed.
Muller utilized finite element analysis (FEA) in the M-Line’s design to eliminate vibration of the arm and beam. A wireless WiFi-enabled tablet is included for setup and troubleshooting. The system is protected by a 2-year warranty and Muller says 95 percent of replacement parts are in stock and available with one-day delivery.
The systems themselves will be made in Switzerland and Colorado, and Muller reports that a total of seven units have already been sold in North America. Applications currently utilizing the systems range from specialty closures to thinwall containers and lids.
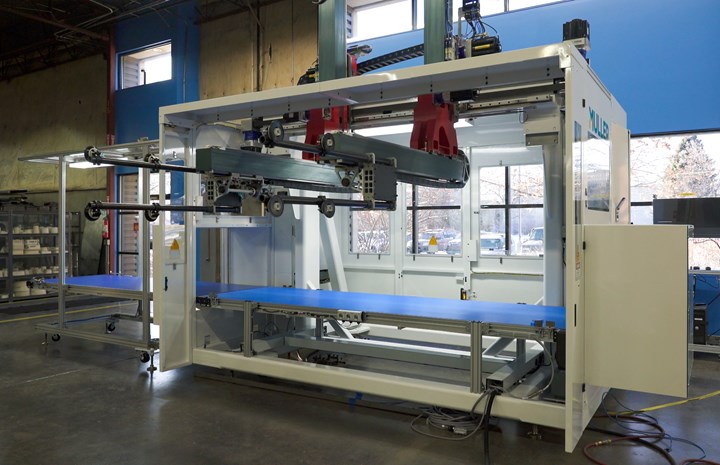
Muller’s new M-Line automation system for injection molded packaging can adapt to different tools and different cavitations.
Related Content
-
Get Color Changes Right In Extrusion Blow Molding
Follow these best practices to minimize loss of time, material and labor during color changes in molding containers from bottles to jerrycans. The authors explore what this means for each step of the process, from raw-material infeed to handling and reprocessing tails and trim.
-
‘Monomaterial’ Trend in Packaging and Beyond Will Only Thrive
In terms of sustainability measures, monomaterial structures are already making good headway and will evolve even further.
-
US Merchants Makes its Mark in Injection Molding
In less than a decade in injection molding, US Merchants has acquired hundreds of machines spread across facilities in California, Texas, Virginia and Arizona, with even more growth coming.