Electric Roller Suited for High-Temp Web Applications
Billed as “game-changing” product to enhance process control and efficiency.
Webex’s Electric HTR Roller has been designed to address the unique needs of industries requiring high-temperature applications. It boasts several features that Webex, a Maxcess company, says make it a game-changer for manufacturers looking to achieve precise process control and efficiency.
Key Features of the Webex Electric HTR Roller:
Even Heat Profile: The Electric HTR Roller offers an even heat profile end-to-end, ensuring consistent temperature distribution across the entire roll face, which is essential for high-quality production.
Multiple Heating Zones: With multiple heat zones, the Electric HTR Roller accommodates various web widths, enabling manufacturers to optimize their processes.
Fast Ramp-Up Time: The Electric HTR Roller achieves process temperatures of up to 850°F in approximately 1 hour, significantly reducing downtime and improving overall productivity.
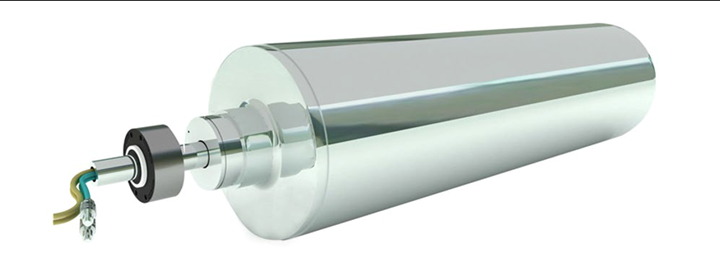
Integrated Zone Temperature Control: Featuring integrated zone temperature control with high alarm shutoff, the Electric HTR Roller offers enhanced safety and precision.
Compatibility: The Electric HTR Roller seamlessly integrates with existing controllers, providing a hassle-free upgrade option for manufacturers. Alternatively, customers can request Webex to supply compatible controllers.
Reduced Maintenance: This environmentally-friendly solution reduces maintenance costs and downtime, offering long-term benefits to users.
Energy Efficiency: The Electric HTR Roller provides up to 70% energy savings compared to traditional fluid-heated rolls, making it a cost-effective choice for businesses.
Notes Jason Annes, global product manager at Maxcess, “The Webex Electric HTR Roller represents a major advancement in the web handling industry. With its precision control, fast ramp-up time and energy efficiency, manufacturers in various industries can expect improved productivity, reduced operational costs and superior product quality.”
Related Content
-
What to Know About Your Materials When Choosing a Feeder
Feeder performance is crucial to operating extrusion and compounding lines. And consistent, reliable feeding depends in large part on selecting a feeder compatible with the materials and additives you intend to process. Follow these tips to analyze your feeder requirements.
-
How to Select the Right Tooling for Pipe Extrusion
In pipe extrusion, selecting or building a complementary set of tooling often poses challenges due to a range of qualitative factors. Here’s some guidance to help you out.
-
Use Interactive Production Scheduling to Improve Your Plant's Efficiencies
When evaluating ERP solutions, consider the power of interactive production scheduling to effectively plan and allocate primary and secondary equipment, materials and resources on the overall production capacity of the business and conclude that this is a key area that cannot be overlooked.