Fakuma: Boy Promotes Upgrades and New Additions
Boy Machines had an ejector upgrade, easier network connectivity, Molding Assist software and cooling flow recording on display at the show in Friedrichshafen.
At Fakuma 2021, German injection molding machine manufacturer Dr. Boy GmbH & Co. KG (Neustadt-Fernthal; U.S. office Exton, Penn.) highlighted a range of advances from an electromechanically operated ejector and a WLAN-stick to make molding machines network-compatible to an intelligent molding assistant software.
The optional electromechanically operated ejector is designed for the company’s larger BOY 50 to BOY 125 injection molding machines. Featuring adjustable speed profiles up to 500 mm/sec, the electromechanical ejectors are independent from the molding machine’s main drive, and they offer an exact track-positioning, allowing synchronization of ejector and handling movement.
Boy says that by utilizing the WLAN stick, molders can more easily integrate Procan Alpha 4 control equipped Boy presses into any network without requiring a wired network connection. Boy says some advantages include the ability to communicate wirelessly with the machine via WLAN, with EM 77/83, OPC_UA, VNC, NAS all made possible. The stick also lets molders connect the machine via a phone’s hotspot, and it provides immediate assistance by remote control via VNC or programming environment, so that assistance globally is possible via a stable internet connection. The company says the stick allows easier integration into an existing customer-network by DHCP-router, eliminating complex configuration. It can also support remote monitoring, allowing molders to be online with the machine wherever they are.
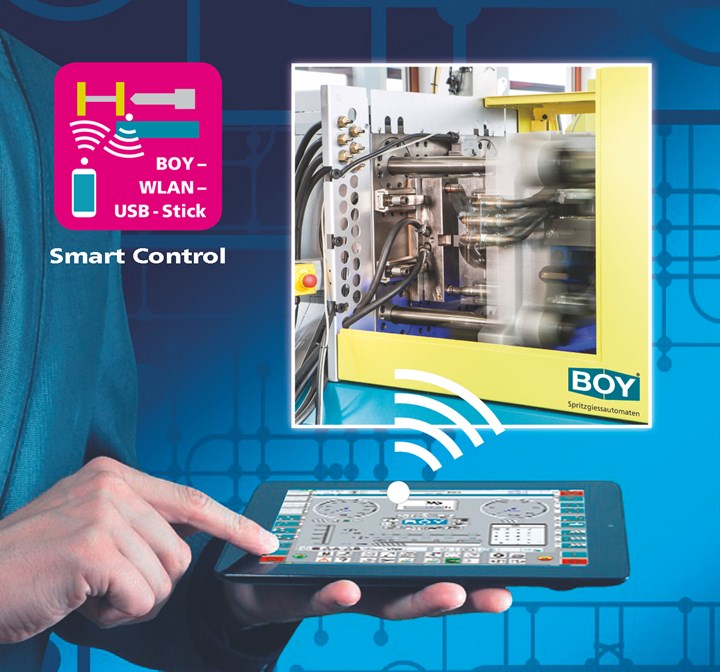
Boy’s WLAN stick lets molders integrate Procan Alpha 4 control equipped Boy presses into any network without needing a wired connection.
Photo Credit: Boy Machines
The Molding Assist software is described as an intelligent assistant that can identify molding faults. Giving users suggestions to eliminate injection molding errors at the machine, Boy says setting pages of the Procan Alpha 4 control are directly displayed to ease troubleshooting. A spokesperson told Plastics Technology that the system works as well as “the data the client enters.” The program assigns answers to questions with the most frequent answers given to users as the first possible step. Boy compares it to a Google search. “The answer that most often solved the problem is suggested first the next time,” the spokesperson said.
Finally, Boy has added flow recording and measurement to its cooling water distribution. With this feature, flow is digitally recorded and shown on the machine display. Target rates and tolerances can be set, displayed and monitored. Boy said it plans to integrate this function as standard in all its Procan Alpha 4 enabled machines. In addition to flow volume, an optional temperature display with process data monitoring is available. The spokesperson said Boy added sensors to capture the measurements. Measured values or “recipes” can then be saved for each part.
Related Content
-
System Offers 'Lights Out' Mold-Channel Cleaning & Diagnostics
New system automatically cleans mold-cooling lines—including conformal channels—removing rust and calcium, among other deposits, while simultaneously testing for leaks, measuring flow rate and applying rust inhibitor.
-
North American Distribution for System to Track Cooling-Circuit Temperatures, Flow Rates
Globeius is now a North American supplier of Mouldpro’s Flosense 1.0 Flexible Flow Monitoring system for tracking manifold pressures and mold temperatures.
-
Cooling Bore Creates Turbulent Flow
Hasco says its Cooling Tornado facilitates turbulent flow, boosting cooling effectiveness by up to 20%.