IMM Cells Display Communications, Energy Measurement and Energy Recovery
NPE2024: Wittmann is featuring five injection molding machines incorporating its range of robotics and auxiliaries, with all products employing industry 4.0 communications, energy measurement and a brand-new red color.
Wittmann is utilizing five injection molding machine work cells in a new red color to showcase its latest molding, robotic and auxiliary technologies. Every cell feature the company’s 4.0 Technologies, including Plug and Produce, Wittmann Digital, all-new Control Room, Remote Access, and OPC UA communication and data collection. In addition, every machine in the booth relays energy usage via Wittmann’s proprietary IMAGOxt software. Energy is recovered in all the SmartPower and EcoPower molding machines, thanks to kinetic energy recovery system (KERS) technology. On the process side, Wittmann’s HiQ Flow program is being deployed to minimize scrap and improve part quality.
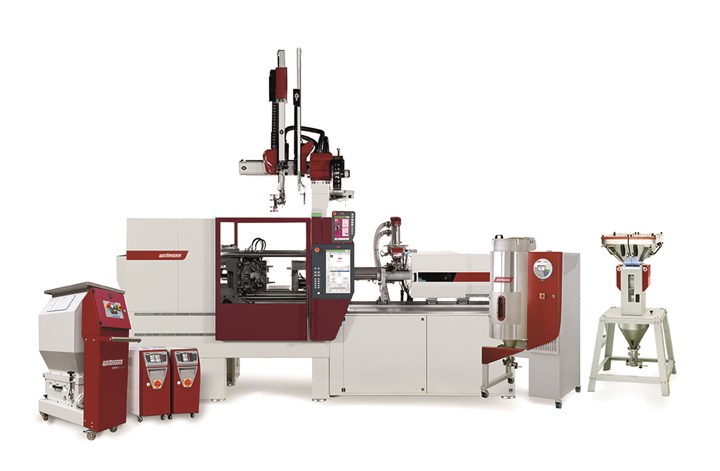
Five machine cells will be used to display Wittmann’s full slate of injection molding machines, auxiliaries and robotics, in a new red color. Source: Wittmann
A large-tonnage MacroPower servo-hydraulic machine with an electric metering motor is molding a sunroof bezel from Axiom, applying hybrid-grade recycled content PP from TotalEnergies and running regrind from the process. The new Feedmax Clean with dust/fines separation is conveying material from the G-Max XL granulator to the G34 Blender, removing dust during conveying, which is managed from the M8 central conveying controller. The press is applying Wittmann HiQ Flow to account for any changes in resin viscosity. Process cooling comes via a Tempro Plus D L250 temperature control unit (TCU) and a 20-ton, air-cooled Coolmax chiller. A WX153 Robot is removing parts and, in partnership with Keyence, show how QR codes and other important data can be printed directly onto the part.
A 3-shot SmartPower servo-hydraulic 400 is utilizing Wittmann’s Cellmould technology on the outer layer of a cup to mold the 1-cavity “family mold” cup and lid from a Haidlmair tool, using Borealis PP resin and color, and a WX142 robot. Auxiliaries include Aton Plus 120 VS dryer with a 3-hopper Silmax compact cart. This cell features Wittmann’s Net5 conveying platform, as well as a Tempro Plus D 250 TCU, WFC120 water manifold, Coolmax 15-ton air-cooled chiller and Dosimax color feeders.
In LSR, A SmartPower 120 is running beverage caps/covers from Nexus, using a 4-cavity family mold and Momentive silicone. Parts are removed by a W918 robot, and auxiliaries include the Coolmax 5-ton, air-cooled chiller and Tempro Plus D L250 TCU.
In micromolding, 2-shot MicroPower 15 is molding a speaker membrane from Starlim Spritzguss, using PBT and LSR, with a Micro Dryer and Micro Plus D TCU also in the cell. Finally, a SmartPower 4.0 demo cell features Wittmann 4.0 on the latest generation SmartPower servo-hydraulic machine, with Wittmann’s B8X controller, and new multiconnector for screw and barrel assemblies, plus a W918 robot, two Tempro Plus D TCUs, one G14 Blender and one Aton Plus Dryer.
“Control Room” Debut
There are also two freestanding robot cells, both showcasing the new Control Room, which debuts at NPE2024. Wittmann says the Control Room can be used to view and control several Wittmann auxiliary products within its work cell, operating on the R9 robot pendant as well as a PC.
In addition, the new Sonic 131 robot shows off its acceleration and speed via demos, while a WX142 Robot is being used to demonstrate the latest QuickNew Teach Program generator, which Wittmann says makes programming complex injection work quicker and easier.
Related Content
Datwyler Expands O-Ring Production
The company has added injection molding machines to production sites in Mexico and China to boost production.
Read MoreMilacron’s Massive Booth Highlights Multiple Brands
NPE2024: Coinjection of postconsumer resin, in-mold decoration, LSR micromolding and bioplastics processing are just some of the machine displays at Milacron's booth.
Read MoreCold Deck for LSR Molding
After field testing, validation and refinement with customer feedback, Husky announced the introduction of a cold-deck system for direct gate molding of LSR.
Read MoreCompletely Connected Molding
NPE2024: Medical, inmold labeling, core-back molding and Industry 4.0 technologies on display at Shibaura’s booth.
Read MoreRead Next
Wittmann Finds Battery Partner for Direct Current (DC) Molding Machine Concept
Displaying the solar-powered press at Fakuma 2023 following its K 2022 debut, Wittmann announced a development partnership with Innovenergy for DC infrastructure.
Read MoreFakuma: High-Speed Robot Series Extended
Wittmann Battenfeld will extend its Sonic series of high-speed robots at Fakuma, introducing the Sonic 108 targeting smaller injection molding machines.
Read MoreMES Platform Adds Energy Monitoring Module
Wittmann Battenfeld’s TEMI+ manufacturing execution system (MES) software has added the IMAGOxt software module to track energy consumption and more on a plant floor.
Read More