Materials: Extremely Lightweight and Foam-Free TPEs
Kraiburg’s TPE’s new TPE technology incorporates 3M’s Glass Bubbles to create extremely lightweight thin-wall moldings.
An innovative material technology that allows the production of non-foamed TPEs with very low density has been developed by Kraiburg TPE, Buford, Ga., and has resulted in the commercialization of three new product lines for the manufacture of extremely weight-saving components of a type that is in increasing demand for vehicle construction and other sectors such as other sectors such as power tools, aviation, drones, sports, leisure and outdoor items.
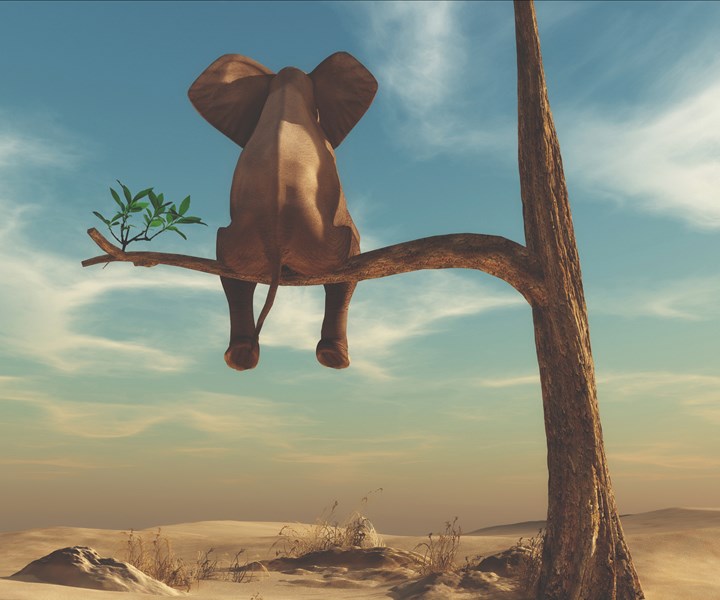
While expandable materials including TPEs are often used to meet this demand, they require strict process control procedures to achieve an even surface quality without surface waviness. Kraiburg’s new TPE technology utilizes Glass Bubbles from 3M, St. Paul, Minn., to produce TPEs with very low densities of between 0.7 and 0.9 g/cm³ (1.358 and 1.746 slug/ft³) that reportedly allow the production of extremely lightweight thin-walled moldings that provide excellent surfaces and are able to withstand mechanical loads. The microscopically small hollow glass bubbles are made of chemically stable borosilicate glass that is insoluble in water. They spread evenly in the TPE matrix and help increase the dimensional stability.
The new TPEs reportedly can be processed cost-effectively using established injection molding and extrusion machinery. Kraiburg claims significant weight savings over other materials including: 50% vs. PVC, 40% vs. TPU and EPDM, 35% vs. TPS, and 30% vs. TPV. Moreover, very homogeneous surfaces and excellent compression set values are also claimed. Also, production waste can be recycled directly. Kraiburg’s initial offering of what is said to be the world’s first TPEs of this type is in three specific series:
▪ Thermolast K LW/UV (lightweight + UV resistance) specifically for exterior vehicle components
▪ Thermolast K LW/CS/UV (lightweight + increased compression set + UV stability) with excellent resilience and adhesion to polypropylene, making this product series particularly suitable for various sealing applications
▪ Thermolast K LW/PA (lightweight + adhesion to polyamides), also with HB nonflammability classification in accordance with UL94; ideal for power tools, for example
Noted Kraiburg TPE’s project manager for advance development Martina Hetterich, “3M Glass Bubbles have been tried and tested as weight-saving fillers in various ‘hard’ thermoplastics, but our new lightweight technology is using them in TPEs for the first time/ Thanks to the excellent collaboration with our partner 3M, we have been able to develop formulations that not only meet current lightweight construction and quality requirements, but also open up completely new markets for the commercial use of our TPEs.”
Related Content
-
EV Chargers Made From Renewable PC
SABIC is enabling Charge Amps to manufacture electric vehicle (EV) chargers with a housing made from certified renewable PC, a first for the industry.
-
Ineos Nitriles Launches Biobased Acrylonitrile
The company’s Invireo is said to deliver a 90% lower carbon footprint compared to conventionally produced acrylonitrile.
-
IPEX Opens Injection Molding Facility in North Carolina
The pipe and fittings manufacturer’s new 200,000-square-foot facility represents a $200 million investment and will create 150 jobs.