Materials: Partially Biobased PC Film
Covestro’s Makrofol EC film contains more than 50% of its carbon content sourced from plant-based biomass.
Just recently, PT reported on a strategic cooperation between Covestro, Pittsburgh, Penn., and Helsinki-based Neste, whereby the latter is supplying Covestro with material from renewable sources to replace a significant portion of the fossil raw materials used to date in the manufacture of PC resins. Sustainable alternatives to traditional materials are increasingly being sought by OEMs and designers. Recognizing that sustainable thinking and action are key to a brighter future, Covestro is now expanding its materials portfolio with a novel PC film.
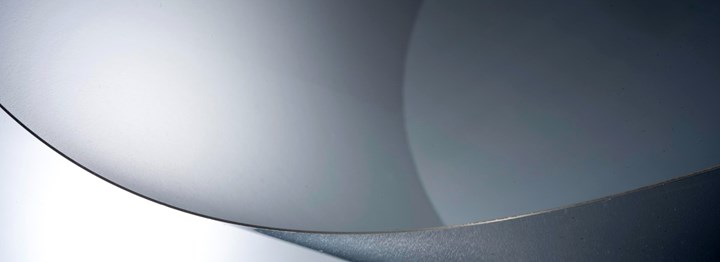
More than 50% of Makrofol EC film’s carbon content is sourced from plant-based biomass. When compared to standard films made from petrochemicals, a portion of the oil-based primary products used have been replaced with plant-based raw materials. Reducing the use of raw materials based on fossil resources slashes the film’s carbon footprint by approximately 20%.
The new PC film reportedly exhibits comparable or even better properties, including improved chemical and weather resistance. This partly biobased film also offers excellent mechanical properties and impact strength, high abrasion resistance and surface hardness, and good optical properties. Such films can be processed by a variety of technologies, including printing, thermoforming, high-pressure forming (HPF), coating (hardcoat, adhesive), cutting and lamination. It can be used in similar applications as traditional PC films, including automotive speedometers, decorative trim parts and instrument clusters, E&E and appliance housings, decorative control panels and electrical insulation. Other applications include labels, tags, overlays and signage and thermoformed packaging for sensitive goods.
Related Content
-
Multilayer Solutions to Challenges in Blow Molding with PCR
For extrusion blow molders, challenges of price and availability of postconsumer recycled resins can be addressed with a variety of multilayer technologies, which also offer solutions to issues with color, processability, mechanical properties and chemical migration in PCR materials.
-
Medical Molder, Moldmaker Embraces Continuous Improvement
True to the adjective in its name, Dynamic Group has been characterized by constant change, activity and progress over its nearly five decades as a medical molder and moldmaker.
-
Medical Tubing: Use Simulation to Troubleshoot, Optimize Processing & Dies
Extrusion simulations can be useful in anticipating issues and running “what-if” scenarios to size extruders and design dies for extrusion projects. It should be used at early stages of any project to avoid trial and error and remaking tooling.