Ribbon Blenders Now Come with Pressure-Feed Vessels
New option enables 100% discharge of the liquid component through a spray bar and into the blending zone, ensuring even mixing and consistent batches.
Ross Ribbon Blenders, which are custom-built for multi-phase mixing, can now be specified with a pressure-feed vessel. Wherein minor liquid ingredients must be thoroughly blended into powder or other solids, a pressure-feed vessel enables 100% discharge of the liquid component through a spray bar and into the blending zone, ensuring even mixing and consistent batches.
In lieu of manually pouring liquids through an open blender cover or safety grating, utilizing a pressure feed-vessel and spray bar facilitates liquid addition while the blender is closed, minimizing dusting and safety issues. The spray bar typically includes four or more spray nozzles so that liquids are uniformly distributed along the entire length of the blender. The pressure- feed vessel eliminates the need for a pump to deliver liquids to the spray bar. Designed for compressed air supply up to 20 psig or higher, a distinguishing characteristic of the pressure-feed vessel is the absence of residual product in the piping. After the blending cycle, the pressure feed vessel can also assist with cleaning/washdown.
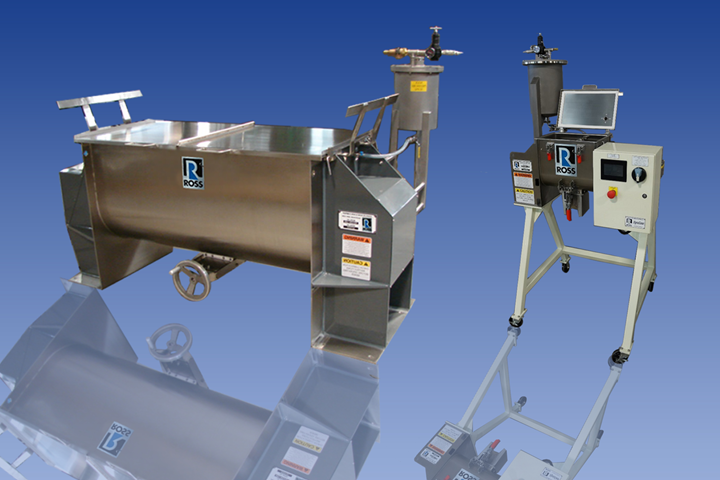
Available in various sizes to accommodate the required volume of the additive liquid phase, these vessels are mounted and plumbed to Ross Ribbon Blenders, which range from 1/2 to 500 ft3 working capacity.
Related Content
-
More Than a Compounder: They Have the Science to Create New Custom Materials
Insight Polymers & Compounders leverages its expertise in polymer chemistry to develop next-generation materials.
-
How to Configure Your Twin-Screw Extruder for Mixing: Part 5
Understand the differences between distributive and dispersive mixing, and how you can promote one or the other in your screw design.
-
Improving Twin-Screw Compounding of Reinforced Polyolefins
Compounders face a number of processing challenges when incorporating a high loading of low-bulk-density mineral filler into polyolefins. Here are some possible solutions.