System Quickly, Safely Cleans and Wipes Pelletizing Dies
Unit mounts directly to the die body in a space-saving design that avoids thermally dependent dimension stackups.
Bay Plastics Machinery (BPM) has created a fast, versatile and customizable die wipe system for on-demand startup of automatic strand pelletizing lines. Full cycle time is approximately four seconds depending on die width. A 16-inch (400 mm) die face can be wiped in as little as a quarter of a second.
The unit mounts directly to the die body in a space-saving design that avoids thermally dependent dimension stackups. Available for 45-degree downward-facing, vertical or horizontal strand die plates, the BPM die wipe features an angled blade that reduces “interrupt” from the blade crossing die holes — increasing throughput by adding relief clearance once the blade passes. The 1-½ inch (38 mm) wide brass blade can be used with single- or dual-row strand dies and die face widths between 6 inches and 40 inches (150 mm to 1,000 mm).
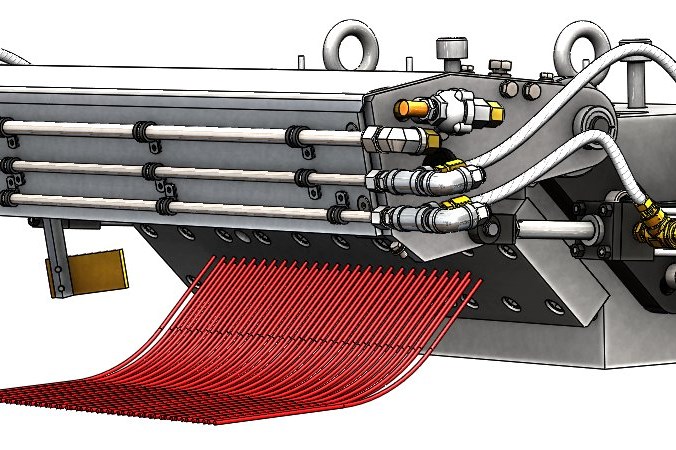
Behaving similarly to a manual die wiping action with a handheld scraper, BPM’s automated die wipe enables startups at higher throughput rates and eliminates the false starts that often occur from manual wiping. Further efficiency is achieved thanks to the wipe’s low air consumption requirements — meaning no accumulator tanks are required for operation.
With an adjustable blade and mounting arm to adjust for optimal preload to the die face, BPM’s automated die wipe is pneumatically activated, with speed controllers to fine-tune motions. Two-axis actuation removes the blade from the die face when parked, keeping the blade cool to reduce adhesion with molten polymer, while also enabling access to the die plate.
Importantly, the single-direction wipe — moving away from the operator — is guarded for operator safety, the guards enabling heat to pass through.
BPM offers custom mounting options for its automated die wipe, which is available either for standalone operation or integrated into strand line PLCs with customizable electronics.
Related Content
-
How to Configure Your Twin-Screw Extruder for Mixing: Part 5
Understand the differences between distributive and dispersive mixing, and how you can promote one or the other in your screw design.
-
Engineering Resins Compounder Expands to Take on More Scrap
Polymer Resources responds to sustainability push by upgrading plant with grinding and shredding equipment to take on both postindustrial and postconsumer reclaim.
-
Processing Megatrends Drive New Product Developments at NPE2024
It’s all about sustainability and the circular economy, and it will be on display in Orlando across all the major processes. But there will be plenty to see in automation, AI and machine learning as well.