Two-Piece Welded Feed Throat Liner Assembly
Unit is self supporting and provides the capability to press out a worn liner and install a new or refurbished liner.
Glycon now offers a two-piece welded liner assembly for feed throats. The design does not rely on an "interference fit" between the liner and housing to contain fluids.
Once installed, the two-piece design is self-supporting and provides the capability for processors to press out a worn liner and install a new or refurbished liner. This unique design of a new or replacement feed throat for extrusion or blow molding machines allows for replacement of a worn liner without replacing the entire feed throat housing. The Glycon design allows for unlimited liner replacements to match a new or relined barrel assembly.
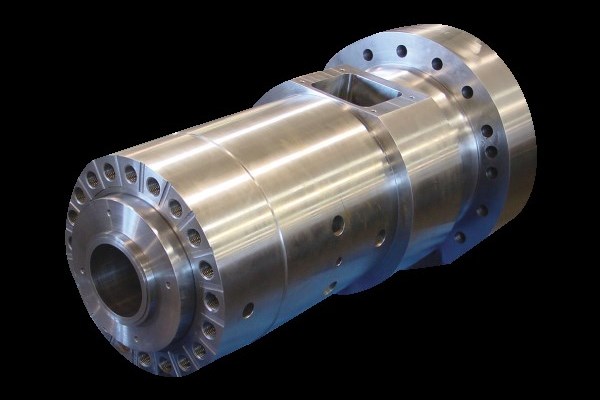
Lead time to replace the liner is normally about 4 weeks, and with commonality of extruders it allows for a replacement feed throat to be in stock for regular rotation of worn liners on a scheduled basis. At the same time, the feed throat can be pressure tested and acid flushed, if necessary, to ensure proper flow in cooling channels. Allowing for normal liner wear in cooling channel blockage this process would be preformed when a barrel is replaced to maintain OEM tolerances.
Glycon will be participating at the Extrusion 2021 Conference, September 21-23, Rosemont, Ill.
Related Content
-
The Importance of Barrel Heat and Melt Temperature
Barrel temperature may impact melting in the case of very small extruders running very slowly. Otherwise, melting is mainly the result of shear heating of the polymer.
-
Understanding Melting in Single-Screw Extruders
You can better visualize the melting process by “flipping” the observation point so the barrel appears to be turning clockwise around a stationary screw.
-
Single vs. Twin-Screw Extruders: Why Mixing is Different
There have been many attempts to provide twin-screw-like mixing in singles, but except at very limited outputs none have been adequate. The odds of future success are long due to the inherent differences in the equipment types.