Wireless Strain Measurement Tracks Tie Bar Bending, Cavity Pressure
Gefran says the QE2008-W wireless strain measurement system uses a sampling rate of up to 1000 measurements/sec to measure clamping force, bending and cavity pressure profile.
Gefran Inc. (North Andover, Mass.) has introduced the QE2008-W wireless strain measurement system to the North American market for die casting and injection molding. Utilizing a sampling rate of up to 1000 measurements/sec, the QE2008-W system can gauge clamping force, bending and cavity-pressure profile helping molders maintain production quality while also protecting equipment from damage. Each QE2008-W system comes with a protective carrying case containing eight sensors that mount to tie bars magnetically. Gefran offers users the Sensormate app to serves as the digital interface for the QE2008-W system, which can also connect to a molder’s network. Available at the Microsoft Store, Google Play and Apple App Store, the app allows the QE2008-W to connect to smartphones, tablets and computers, so that multiple users can analyze and share measurement data.
No wiring and magnetic application mean the QE2008-W can be installed in minutes. Once in place, the system can help molders with mold alignment, ensuring equal force distribution and minimizing flash, plastic deformation and mold damage. The sensors connect to the Sensormate app using Bluetooth, and the micro-electro-mechanical (MEM) chips inside the QE2008-W sensors ensure proper placement and orientation. Whenever the QE2008-W is connected to the app, it will also check for firmware updates with the sensors updated through Sensormate.
The app serves as the digital interface for the QE2008-W system, which can also connect to a molder’s network. Users can locate the sensors wirelessly through the app and then download measurements as raw data or put the information into a chart. Doing so, they can quickly summarize test values and measurement data into a PDF report, include screenshots and add comments to give readers contextual details or troubleshooting notes.
To track bending forces, the QE2008-W uses four sensors, evenly distributed around the tie bar and mounted at 90-degree intervals. By averaging the readings from these sensors, the QE2008-W measures maximum tension to determine the angle and direction of the bend, achieving greater accuracy of tension and compression measurements for each tie bar.
Cavity-Pressure Profile
The QE2008-W can also measure the cavity pressure profile by calculating the indirect pressure on tie bars during the injection cycle. Compared to in-cavity sensors, the QE2008-W lives outside the tool and can be reused on multiple machines and several types of molds, costing less to operate than permanent methods of measurement, according to Gefran.
In addition to low-energy Bluetooth communications, the QE2008-W wireless strain measurement system features an integrated accelerometer (MEM chips). Gefran says this means that sensor mounting can be done quickly, without reliance on diameter-dependent templates or guessing. For the QE2008-W, the accelerometer accurately determines the sensor's relative position using gravity, while calculating its angle in relation to another sensor. The sensor’s indication lights offer users guidance on placement or repositioning.
The QE2008-W also has integrated RAM inside each sensor for measurements at a rate of 1kHz, and the strain measurements are securely saved in the sensor’s RAM during the measurement period. Once a measurement is complete, the sensor transmits the saved data to the Sensormate app.
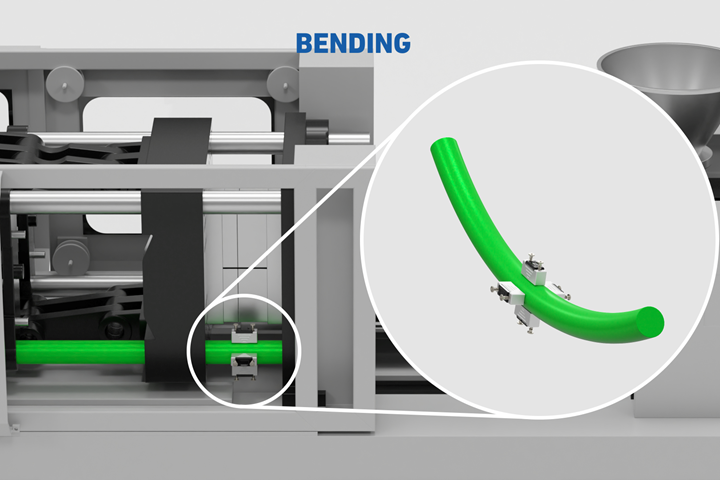
Gefran’s QE2008-W wireless strain measurement system installs in minutes via magnets and feeds data to an app via Bluetooth.
Photo Credit: Gefran
Related Content
Injection Molding: Focus on these Seven Areas to Set a Preventive Maintenance Schedule
Performing fundamental maintenance inspections frequently assures press longevity and process stability. Here’s a checklist to help you stay on top of seven key systems.
Read MoreBack to Basics on Mold Venting (Part 2: Shape, Dimensions, Details)
Here’s how to get the most out of your stationary mold vents.
Read MoreA Systematic Approach to Process Development
The path to a no-baby-sitting injection molding process is paved with data and can be found by following certain steps.
Read MoreThree Key Decisions for an Optimal Ejection System
When determining the best ejection option for a tool, molders must consider the ejector’s surface area, location and style.
Read MoreRead Next
People 4.0 – How to Get Buy-In from Your Staff for Industry 4.0 Systems
Implementing a production monitoring system as the foundation of a ‘smart factory’ is about integrating people with new technology as much as it is about integrating machines and computers. Here are tips from a company that has gone through the process.
Read MoreBeyond Prototypes: 8 Ways the Plastics Industry Is Using 3D Printing
Plastics processors are finding applications for 3D printing around the plant and across the supply chain. Here are 8 examples to look for at NPE2024.
Read More