‘World First’ 3D Printing Material for Wear Parts
Liquid DLP resin makes high-precision parts with wear life 30 to 60 times longer than conventional 3D printed parts.
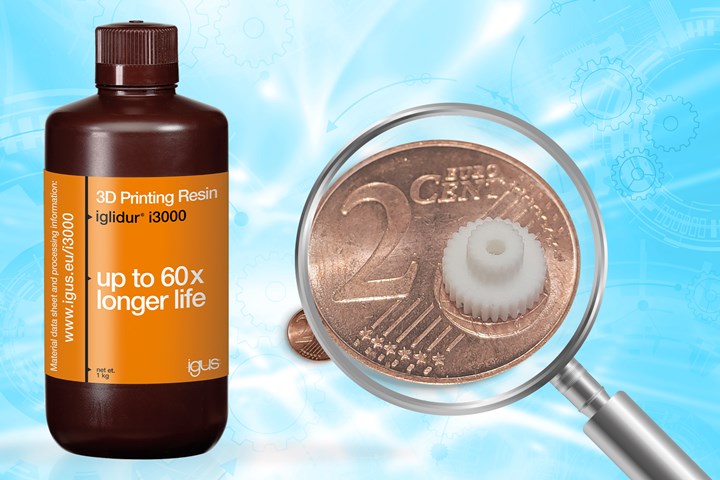
In addition to its new iglidur i3000 DLP resin, igus offers custom printing services that now includes DLP capability with resolution down to 0.035 mm. (Photo: igus)
What’s said to be the first 3D printing material for highly wear-resistant moving mechanical parts has been introduced by igus of Germany. Its new iglidur i3000 proprietary liquid resin is said to enable additive manufacturing by digital light processing (DLP) of very small, precise components in the millimeter range with wear life 30 to 60 times longer than conventional 3D printing resins.
The company says DLP is particularly suitable for printing tiny parts with high precision, such as gears with tips just 0.3 mm thick. The tips also have very smooth surfaces that require no post-treatment, igus says. The new material, like others from igus, contains solid microscopic lubricant particles and needs no external lubrication.
In addition to the new material, igus also offers custom-printed components. Up to now, igus offered 3D printing by selective laser sintering (SLS) and fused deposition modeling (FDM). Now, igus is expanding its 3D printing service with DLP printers that can achieve a resolution of just 0.035 mm. It offers an online tool with which customers can upload STEP files for their components or configure gears in just a few clicks.
Related Content
-
Additive Fusion Technology Optimizes Composite Structures for Demanding Applications
9T Labs continues to enhance the efficiency of its technology, which produces composite parts with intentionally oriented fibers.
-
Production Tool, Prototype Time
Mantle's metal 3D printing technology targeted toolmaking and injection molders and moldmakers are taking notice.
-
Additive Technologies for Injection Mold Tooling Ride Tailwinds
NPE2024: Lowering barriers to additive manufacturing adoption in toolmaking.