Austrian Recycler's Mission to Recycle PET Takes It Beyond Bottles
Mission PET supplements bottle-to-bottle capability with alternative applications for recycled PET.
The inherent recyclability of PET, the quality of available feedstock for recycling and a supportive regulatory environment have created a circular economy for PET bottles in Europe. Legislation is in place to require 25% recycled content in PET bottles by 2025, and proposed rules would raise this to 65% by 2040. According to a 2022 report, several countries are already collecting over 90%.
In this environment, Markus Huemer and Daniel Pichler saw opportunity and founded Mission PET. Previously, both had been employed at recycling equipment manufacturer Next Generation Recycling (NGR). “My colleague and I knew the payback times. We had been joking for years that we should do it ourselves. So we made a business plan, a marketing plan and found investors,” Huemer says, now managing director at Mission PET.
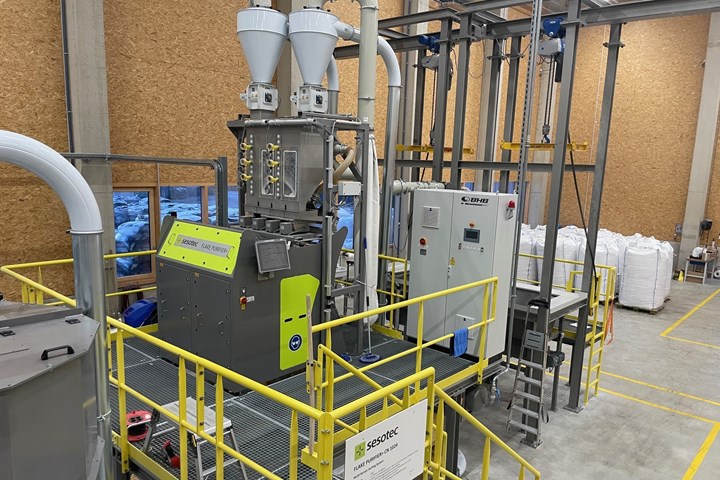
The Sesotec Flake Purifier+ at Mission PET. Photo Credit: Mission PET
The company’s recycling line is now installed and running 3-4 days per week. It is expected to be operating at full capacity sometime in either spring or summer 2024. The operation consists of a Sesotec sorting system, a pre-dryer from Eisbar, MAS extruder, Nordson filtration, liquid state polycondensation system from NGR, an underwater pelletizer by Econ and a post dryer, also from Eisbar.
Finding Alternative Applications in a Shifting Market for Recycled Polymers
The line is designed and built to be a “bottle to bottle” operation, for example starting with a food grade PET flake from bottles and creating a high-purity food grade pellet as its output, ready to be sold to a converter to become new bottles. But changing conditions have prompted Mission PET to branch out into other applications.
“The PET market is different than what it was three years ago. Over the last year, bottle-to-bottle has been a little bit difficult because stocks were full and imports from China were huge. So we started to think a bit differently,” Huemer says.
Mission PET is currently doing production runs mainly for alternative applications (non bottle-bottle), where it is engaged in business that includes service recycling and forms of PET beyond the clear food grade bottles.
This is where the Sesotec sorter, a Flake Purifier+, becomes especially important. “When thinking about bottle flakes for food applications, the material is already quite clean. But we also buy mixed colored bottle flakes for alternative applications and there we often see higher levels of PVC,” Huemer explains. The Sesotec flake sorter makes life easier on the extruder by removing PVC, metal and any other unwanted materials. At PET processing temperatures, hydrodechlorination causes the release of HCl, which degrades PET and can damage equipment.
“It really makes sense to sort it out and avoid the material degradation in the extruder, because PVC will hinder the polycondensation process and cause unexpected values in the granules if the amount is too high,” Huemer says.
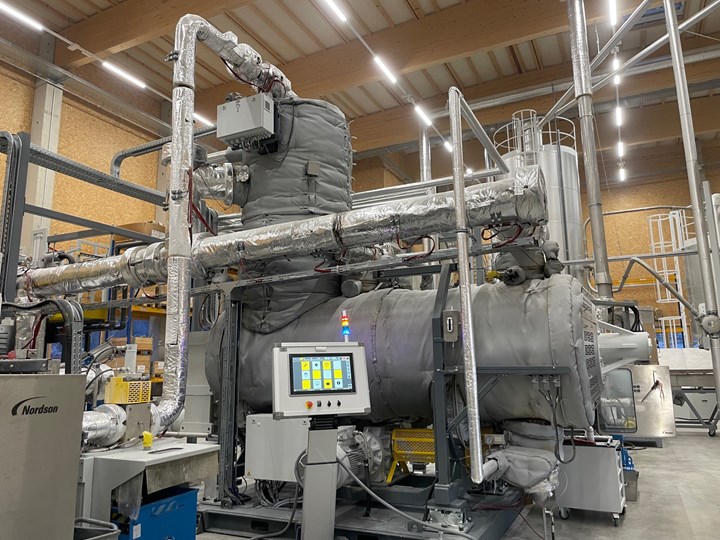
NGR’s liquid state polycondensation (LSP) system enables Mission PET to control viscosity and reduce contamination in rPET. Photo Credit: Mission PET
The configuration of the extruder enables it to be fed simultaneously from a feeding screw and from the Sesotec sorter. Mixed color PET flake material is fed through the Flake Purifier+, while shredded lumps or fines are fed directly via the screw system. “The result is a granule that still has still has quite a high viscosity, it’s filtered and really good quality for straps, film, any application for which color is not that important,” Huemer says.
By incorporating shredded lumps and fines in its product, Mission PET is diverting material that would otherwise be incinerated, while also filling an unmet need for recycled materials.
As recycled content minimums increase, more and more of the bottle feedstock will go back into bottles, in the EU especially. Which raises the question: Where will other manufacturers get recycled PET? Strategies like Mission PET’s, combining technology and available materials to make a product that meets the needs of the right application just as well, may be the answer.
Related Content
US Merchants Makes its Mark in Injection Molding
In less than a decade in injection molding, US Merchants has acquired hundreds of machines spread across facilities in California, Texas, Virginia and Arizona, with even more growth coming.
Read MoreAt NPE, Cypet to Show Latest Achievements in Large PET Containers
Maker of one-stage ISBM machines will show off new sizes and styles of handled and stackable PET containers, including novel interlocking products.
Read MoreFirst Water Bottles With Ultrathin Glass Coating
Long used for sensitive juices and carbonated soft drinks, KHS Freshsafe PET Plasmax vapor-deposited glass coating is now providing freshness and flavor protection for PET mineral water bottles.
Read MoreMeasuring Multilayer Plastic Containers Made Easier With Today's Ultrasonic Gauges
Ultrasonic gauge technology has evolved to simplify measurement of very thin layers in plastic containers. Today’s gauges with high-frequency capabilities and specialized software can make multilayer container measurement quick and easy for ordinary users.
Read MoreRead Next
See Recyclers Close the Loop on Trade Show Production Scrap at NPE2024
A collaboration between show organizer PLASTICS, recycler CPR and size reduction experts WEIMA and Conair recovered and recycled all production scrap at NPE2024.
Read MoreFor PLASTICS' CEO Seaholm, NPE to Shine Light on Sustainability Successes
With advocacy, communication and sustainability as three main pillars, Seaholm leads a trade association to NPE that ‘is more active today than we have ever been.’
Read MoreLead the Conversation, Change the Conversation
Coverage of single-use plastics can be both misleading and demoralizing. Here are 10 tips for changing the perception of the plastics industry at your company and in your community.
Read More