Fast, Simple QC Method Directly Quantifies Recycled Content in Plastics
Novel fluorescence-based spin-out technology provides a rapid and reliable method to measure and certify recycled content in a wide range of plastics.
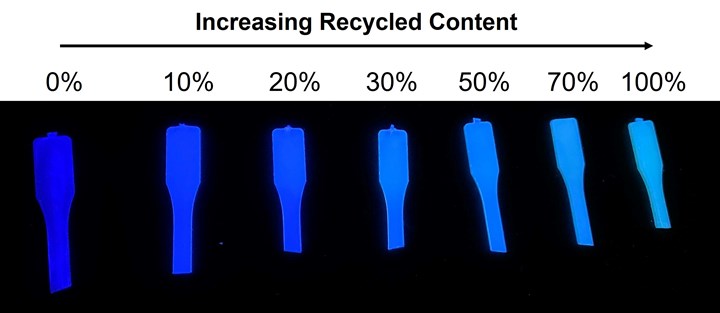
With ReCon^2, recyclers and compounders can produce masterbatches with a traceable recyclate concentration, and its “fluorescent signature” can be tracked to the final products to be compared and validated when recycled-content claims are audited. (Photo: University of Manchester)
What appears to be a breakthrough methodology that can quickly and accurately quantify the recycled content of a plastic product is being developed by a team from U.K.’s Manchester University. The development of ReCon^2 for direct quantification of recycled content in a wide range of plastics and plastic packaging is being led by Michael Shaver, professor of Polymer Science and director of the Sustainable Materials Innovation Hub, and by Natalie Mera-Pirttijarvi, project manager at the Univ. of Manchester Innovation Factory.
ReCon^2, short for “Recycled Content Reconnaissance,” uses minute quantities of fluorescent tracker additives and fluorescence spectroscopy to analyze the recycled content of plastic materials or articles. Not only does it measure the intensity of the fluorescence as an indicator for the concentration of the additive, but the spectrum changes as the recyclate is diluted with virgin polymers. As such, recyclers/compounders can produce masterbatches with a traceable recyclate concentration, and its “fluorescent signature” can be tracked to the final products to be compared and validated when recycled-content claims are audited.
ReCon^2 uses minute quantities of fluorescent tracker additives and fluorescence spectroscopy to analyze the recycled content of plastic materials or articles.
The Manchester team’s Recon^2 approach can be used as a QC method for a plastic material or product, or a section or component of it. Within minutes, the recycled content of the product can be assessed accurately and precisely to about a 5% wt. level. The method can be used to minimize fraudulent claims of recycled content.
The technique reportedly has shown success with various high-volume packaging plastics—HDPE, LDPE, PP and PET—and is also expected to be applicable to PS, PVC and specialty plastics. Although it was developed for mechanical recycling, it is anticipated that it can also be adapted for chemically recycled feedstocks.
A Challenge to the Mass Balance Approach
While the technology and its applications are still under development, the Manchester team has been actively contacting companies along the plastics, packaging and recycling production chains and related organizations to explore interest in the technology. This encompasses both mechanical and chemical recycling as a complement or alternative to present chain-of-custody, ISCC+ and mass-balance certification methods. In contrast to these existing methods, ReCon^2 is able to provide a direct measurement of recycled content in individual polymer feedstocks or packaging items rather than just an average over total production.
According to the Univ. of Manchester researchers, there is currently no commercially available fast and accurate quantification method to determine the recycled content in a plastic product, particularly as a simple and inexpensive quality QC method. While the mass-balance approach is the current methodology for determining the percentage of recyclate in a manufacturer’s products and packaging, there is considerable concern with factors such as high costs, traceability, data security and auditing challenges, especially in identifying and measuring the recycled content in a specific product or package.
According to the Manchester team, accurate and rapid analytical determination of recycled content (and thus tax liability in some jurisdictions) using other previously established physical characterization methods, such as rheology or differential scanning calorimetry (DSC), is hugely challenging. This is because the results depend largely on the conditions of the recycling process itself and are strongly affected by factors such as plastic degradation, presence of additives, and polymer feedstock variations. Moreover, such techniques are time-consuming, expensive, and specialized, requiring complex equipment and expert operators.
By contrast, ReCon^2 is completely process-independent, promising a fast, accurate, inexpensive and robust solution to facilitate the assessment of plastic packaging taxes and show conformity with the legal requirements and commitments made by many companies across the supply chain. The researchers say there will be only a minor impact on recyclate cost; the tracking marker materials are FDA approved for food packaging, and there are no adverse effects on mechanical and chemical properties of recyclate or taste/odor generation.
ReCon^2 could therefore offer several potential benefits to the plastics industry, in part by disincentivizing “greenwashing” and fraudulent practices that devalue circularity and erode public trust in plastics recycling.
Related Content
X-Ray Vision Inside Parts Gets More Affordable for Processors
Shimadzu’s new benchtop x-ray CT scanner provides internal and external metrology and flaw detection at a fraction of the previous cost.
Read MoreAvient Receives PLASTICS’ 2023 Re|Focus Sustainability Innovation in Design Award
Said to be the first digital tool of its kind, the award was for Avient’s post-consumer recycled resin Color Prediction Service.
Read MoreInline Inspection System for Wood Plastic Composites
Pixargus’ ProfilControl 7 DX WoodPlasticComposites measure all dimensions and geometrics, including deep grooves.
Read MoreExtrusion Plastometer is Modular, Easy to Clean
Improved accessibility and optimized surfaces enable the instrument to be cleaned quickly, expediting testing times.
Read MoreRead Next
See Recyclers Close the Loop on Trade Show Production Scrap at NPE2024
A collaboration between show organizer PLASTICS, recycler CPR and size reduction experts WEIMA and Conair recovered and recycled all production scrap at NPE2024.
Read MoreLead the Conversation, Change the Conversation
Coverage of single-use plastics can be both misleading and demoralizing. Here are 10 tips for changing the perception of the plastics industry at your company and in your community.
Read MoreMaking the Circular Economy a Reality
Driven by brand owner demands and new worldwide legislation, the entire supply chain is working toward the shift to circularity, with some evidence the circular economy has already begun.
Read More