Heat-Activated Purging Concentrate Cuts Molder's Scrap & Changeover Times
CH3 Solutions increased productivity on its multi-cavity hot runners with new Asaclean Plus Grade concentrate.
A new heat-activated purging concentrate is being used by CH3 Solutions, a custom injection molder of PP tiles for sports flooring and garages, to reduce scrap and changeover time on its multi-cavity hot runners. The Dalton, Ga., molder opted for Asaclean PLUS Grade concentrate after trialing four competitive products, which did not perform sufficiently.
Developed by Asahi Kasei Asaclean Americas, Asaclean PLUS heat-activated chemical purge is said to offer the performance and cleaning power of Asaclean purging compounds, but blends seamlessly with a molder’s own production resins. It is said to excel in difficult purging tasks, particularly high-cavitation molds for caps and closures, and other hot-runner applications. It is also said to meet the needs of extruders and blow molders using their existing processing temperatures, along with other applications such as screw and barrel cleaning, on-the-fly color/material changeovers, contamination removal, and—depending on your production resins—shutdown and sealing. It reportedly performs excellently in clear applications. Excepting both super-low-temperature and super-high-temperature applications, Asaclean PLUS covers the vast majority of resins and processing-temperature ranges.
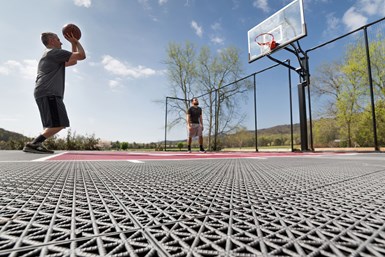
With over 20 color changes per week, CH3 is realizing significant reductions in downtime scrap using Asaclean PLUS concentrate. CH3 molds PP tiles for garages and recreational surfaces.
CH3 has been using a purge program for years, according to Rodney Davenport, vice president. The firm’s plant culture is built on education and working with vendors to ensure everyone understands how to get the most out of their equipment and materials, he notes. “We run lean, and our proactive approach helped us double the size of our business over the past five years.”
CH3 currently operates Wintec injection molding machines from 730 to 1000 tons and will be adding a 1500-tonner in the first quarter of 2022. “All of our machines are equipped with Yudo robots and all of our molds have Yudo hot runners,” says Davenport. The plant currently runs nearly 4 million lb/yr of PP and makes upwards of 20 color changes every week.
Prior to trying the Asaclean PLUS concentrate, the company had been using a mechanical-cleaning grade of Asaclean. In first transitioning to Asaclean PLUS, CH3 continued to use the existing purge for machine barrels and used the new Plus Grade for hot runners. “However, after in-house training we found we could save time by just using the PLUS Grade throughout the entire process,” explains Davenport. As such, Asaclean PLUS is now used to maintain all of CH3’s machines and hot runners.
By eliminating the secondary step of using different purges for the barrel and the mold, CH3 has reduced downtime from 30-40 min to under 15 min. In addition, Davenport believes CH3 realized a 20-25% reduction in overall scrap by using the PLUS Grade. “We were already keeping our scrap to a minimum by utilizing Asaclean and good purging practices. Using PLUS Grade is like adding nitrous oxide to an engine—just add it in for a powerful performance boost.”
Asaclean N-Series chemical purging compounds are some of the strongest performing chemical grades available on the market today, according Asaclean senior marketing manager Tom Hanvey. PLUS Grade was engineered with the cleaning power of the N-Series. Chemical purging compounds are recommended for low-flow and low-pressure environments.
The major advantage cited for PLUS Grade is that it supercharges your own processing resins. Says Hanvey, “Purging compounds sometimes present issues because the processing temperatures and MFRs are different than the resin being purged and the resin following the purge in the changeover. By using PLUS Grade, you know your resin will effectively displace your previous resin—because it is your resin.”
Related Content
Got Streaks or Black Specs? Here’s How to Find and Fix Them
Determining the source of streaking or contamination in your molded parts is a critical step in perfecting your purging procedures ultimately saving you time and money.
Read MoreInjection Molding: Focus on these Seven Areas to Set a Preventive Maintenance Schedule
Performing fundamental maintenance inspections frequently assures press longevity and process stability. Here’s a checklist to help you stay on top of seven key systems.
Read MoreUnderstanding the Effect of Pressure Losses on Injection Molded Parts
The compressibility of plastics as a class of materials means the pressure punched into the machine control and the pressure the melt experiences at the end of fill within the mold will be very different. What does this difference mean for process consistency and part quality?
Read MoreUsing Data to Pinpoint Cosmetic Defect Causes in Injection Molded Parts
Taking a step back and identifying the root cause of a cosmetic flaw can help molders focus on what corrective actions need to be taken.
Read MoreRead Next
Get the Most Bang For Your Purging Buck
More processors are turning to purging compounds to clean their machines and speed up changeovers. Here are tips on how to avoid typical trouble spots when using them.
Read MoreThe Experts Speak: Seven Cost-Saving Purging Tips for Compounding Twins
Purging gurus from the material, machinery and compounding sides of the industry offer their insights on best practices and tips that can keep your compounding twin-screw extruder up and running.
Read MoreFollow These Tips to Power Up Your Purging Process
A properly executed purging process can save processors thousands a year in lost production while helping them increase output and avoid scrap. Here’s how to optimize your results.
Read More