Molder Opts for Machine Flexibility for Complex Jobs
AE Plast opted for tiebarless multimaterial Engel victory machines as it took on complex parts for the appliance and power tool market, including a 3K housing for Dremel’s rotary tool.
Founded in 2006, AE Plast, Császártöltés, Hungary serves the appliance and power tool markets, including molding the housing components for Dremel’s MM20V rotary tool that are sold into the U.S.
AE Plast delivered 80,000 of the assemblies this year, which include a cup housing for the rotary head and two half shells that form the tool’s handle and enclose its battery. In addition to looking good, the assembly must be rugged, as it’s subjected to a 6-and-a-half-foot drop test.
In 2008, AE Plast installed the first of what would become eight victory machines, with the absence of tiebars being the decisive purchasing factor.
The three-component multimaterial design includes a gray housing base molded from 35% glass-filled nylon; black portions using TPE for a soft-touch grip; and blue trim elements also molded from glass-filled nylon and used to achieve a strong bond between the various elements.
Three Shots, Three Materials, Two Steps
For this job, AE Plast uses a 440-ton Engel victory combi injection molding machine featuring a vertical rotary table, three injection units and an integrated viper linear robot from Engel as well. Production comes from two molds: a 2-cavity tool for the cup housing and a 2+2-cavity mold for the two half shells.

Three materials — two glass-filled nylons and a TPE — come together to make the housing for Dremel’s rotary tool. Photo Credits: Engel
AE Plast says the cup housing is the most challenging part in the assembly, with 10 total valve gates applied and a hot runner temperature controller with 27 separate zones required. The widely disparate amounts of material injected pose a challenge when considering residence time and precision dosing. The combined part features 120 grams of gray nylon per shot for the basic housings, with 5 grams of the blue nylon for joining and 20 grams of TPE for the overmolded grip.
In the process sequence, the three components are created in just two injection steps, with the gray base components molded first, and the blue nylon and black TPE part injected simultaneously in the second step after the rotary table rotates.
From an energy efficiency standpoint, the servo-hydraulic ecodrives on AE Plast’s newest victory machines provide average energy savings of 25% compared to older models, with motors that idle when the press is not in motion. For the Dremel cup housings, this is particularly beneficial because idle cooling time accounts for almost half of the total 52-second cycle.
Back in 2008, AE Plast installed the first of what would become eight tiebarless Engel victory machines, with the absence of tiebars being the decisive purchasing factor. AE Plast says the victory’s unobstructed access to the mold area accelerates its setups, making for faster mold changes which ultimately equates to more machine uptime.
Another factor is the plant’s relatively low ceiling height — 16 feet — precluding overhead loading of molds and requiring the retraction of tiebars in a conventional machine. Another benefactor of the open-access platen area: automation. Engel says the linear robot can reach cavities directly from the side without navigating any obstacles. This also reduces the amount of time spent in the mold, enabling faster cycles.
AE Plast notes that many other aspects of the machines heighten their flexibility and appeal, including the ability to change the injection unit nozzle distance by 6 to 12 inches, further increasing the machine’s ability to accept differently sized molds. That flexibility was also aided by Engel customizing the hole patterns on the mold-fixing platens and the ejector bores to AE Plast’s specifications.
Finally, for no extra cost and starting at installation, the victory machines “spoke” Hungarian, with a machine control that could toggle between German and Hungarian, when at the time adding the Uralic language would have been an expensive option on other presses.
“We can clearly see that Engel is a family business,” AE Plast Managing Director Thomas Herpertz says. “We can talk to each other in an open way and reach out to each other. We handle many things without any red tape. That's our understanding of collaboration.”
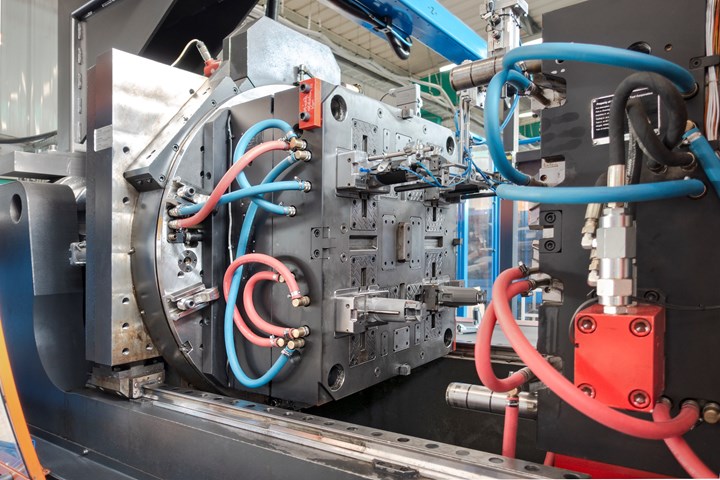
The three materials are processed in two steps, with the basic body molded in the first step, and then the blue trim strips and the black TPE overmolded in the second.
Related Content
Online X-Ray Inspection Boosts Extrusion Quality
Höhle uses Sikora’s x-ray measuring systems for inline quality control of extruded microducts.
Read MoreInjection Molder Changes Up Color Changes
An injection molder of trash cans, pallets, totes and other plus-size components, Rehrig Pacific’s machine fleet is composed of larger tonnage presses whose size makes material changes at the feed throat a potentially dizzying exercise.
Read MoreNew CRM Streamlines Quoting for Automotive Molder
Eliminating the need to contact each supplier for every individual quote, a new CRM for automotive supplier Axiom Group tracks past quotes as well as industry history to generate fast, reliable RFQs and more.
Read MoreNovel ‘Clamtainer’ Extends Thermoformer's Reach in Packaging
Uniquely secure latching expands applications for Jamestown Plastics’ patented clamshell package design.
Read MoreRead Next
Why Blum Went All Tiebarless
One of the first adopters of tiebarless injection machines a quarter-century ago uses them exclusively, both here and in Europe. One reason is their ability to handle oversized molds with awkward projections on smaller presses.
Read MoreK 2019: ReverseCube Puts New Spin on Multimaterial Molding
Foboha brought a new concept to the world of cube molds, splitting top from bottom to handle different materials.
Read MoreSee Recyclers Close the Loop on Trade Show Production Scrap at NPE2024
A collaboration between show organizer PLASTICS, recycler CPR and size reduction experts WEIMA and Conair recovered and recycled all production scrap at NPE2024.
Read More