Molder Repairs Platen Holes with Threaded Inserts
Automotive molder ITW Deltar Fasteners found new life for the battered bolt holes on its machine platens with a solution that’s designed to last.
ITW Deltar Fasteners keeps its mold setters, and the more than 100 injection molding machines on its Frankfort, Ill., production floor, quite busy, undertaking multiple mold changes daily. Based in Troy, Mich., ITW Deltar Fasteners has production operations in Frankfort and Chippewa Falls, Wisc., from which it molds fasteners, hole plugs, bumpers and baffles for the automotive industry and the military.
Years of numerous, regular mold changes had left many of company’s molding machine’s bolt holes stripped, and this damage made securing tools to the platens a time-consuming challenge. Back in August 2020, the company began repairing platen holes with C-Sert threaded inserts made by C-Sert Manufacturing (Portland, Ore.), and Kenny Dearing, ITW Deltar Fasteners process engineer, says those repairs have lasted to this day.
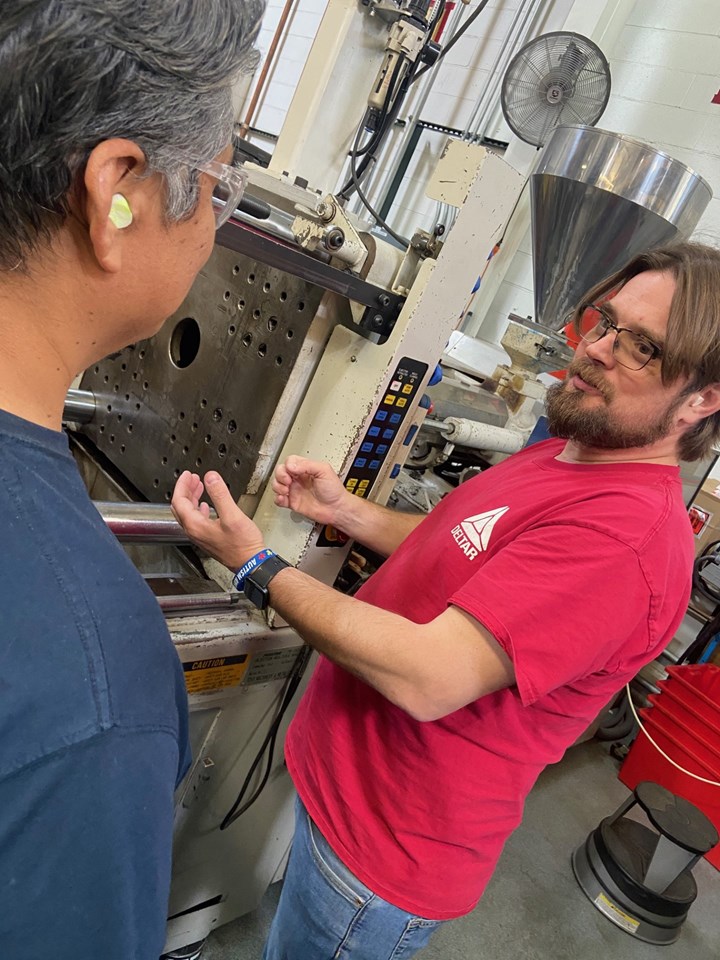
Kenny Dearing (right), ITW Deltar Fasteners process engineer, has utilized C-Serts to replace worn bolt holes on platens throughout the company’s molding facility.
Photo: C-Sert Manufacturing
ITW Deltar Fasteners’ test case for C-Sert were the well-worn platens of a 150-ton Toyo press, vintage 1995. Featuring large and lengthy clamps and clamp bolts for mold installs, the machine is in ITW Deltar Fastener’s sample shop, where it’s used for mold trials and training purposes. After successfully repairing the stripped bolt holes, Dearing and his team installed C-Serts in more than 20 of the company’s presses to replace stripped holes. To help quantify the value of the thread replacements, ITW Deltar Fasteners points out that the sampling press undergoes two or three mold changes per day with more than 250 mold swaps performed through the first half of 2023. Dearing says that what used to take at least 15 minutes is now done in five because the mold setters can always “count on using the correct holes.”
A Permanent Solution
The C-Serts apply what’s known as an interference or metal-to-metal fit, which the company says ensures they will not back out, pull out or vibrate themselves free. Acting as both an insert and a tap, the C-Sert’s internal threads are as hard as a tap, making them highly resistant to damage from bolts once installed.
“Other products and attempts to repair did not sustain over time,” Dearing says. “They would pull out of the repaired holes or become worn out themselves. I knew we needed a permanent solution to repair these bolt holes to make mold installation quick, easy and safe.”
On the advice of his tooling manager, Dearing ordered several C-Sert kits and repaired four badly damaged holes on the Toyo machine in less than 90 minutes. The kits came with a 60-degree center; a cutting bit to open the stripped hole; cutting oil for the cutting bit; the threaded C-Serts; and a bit to install the inserts into the platen. ITW Deltar Fasteners used its own mag drill to center on the hole and perform the cutting.
Dearing notes that the C-Sert-supplied cutter performed well even after clearing multiple holes for installation, adding that C-Sert offers all the needed tools for installation. “It’s frustrating to buy something only to find out that you need a special tool to install it,” Dearing says. “However, the tools needed to install C-Serts can be found in most molding shops.”
In addition to boosting productivity, Dearing says the C-Serts have improved safety on the molding floor. “We have a safer and more productive work space because bolt holes that weren’t working have been restored, enabling us to use the correct mold clamps in the correct positions to mount molds, as opposed to grabbing a corner of the mold,” Dearing explains. “We don’t want ‘good enough’ here — we need to always use proper procedures for mold mounting.”
How permanent a solution does ITW Deltar Fasteners think it’s found? Dearing says that the company’s tooling engineering manager, Greg Mamelson, quipped that “one million years from now, the platens will be dust but the C-Serts will still be there.”
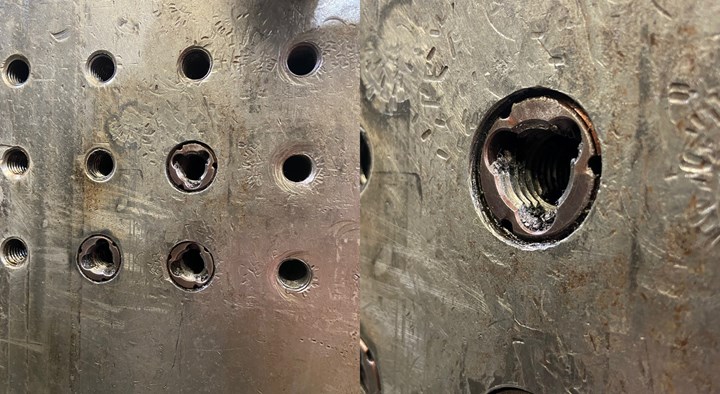
C-Sert threaded inserts help molders replace stripped bolt holes on platens with a new threaded hole that promises long service life.
Photo Credit: C-Sert Manufacturing
Related Content
Automotive Awards Highlight ‘Firsts,’ Emerging Technologies
Annual SPE event recognizes sustainability as a major theme.
Read MoreDesign Optimization Software Finds Weight-Saving Solutions Outside the Traditional Realm
Resin supplier Celanese turned to startup Rafinex and its Möbius software to optimize the design for an engine bracket, ultimately reducing weight by 25% while maintaining mechanical performance and function.
Read MoreImpacts of Auto’s Switch to Sustainability
Of all the trends you can see at NPE2024, this one is BIG. Not only is the auto industry transitioning to electrification but there are concerted efforts to modify the materials used, especially polymers, for interior applications.
Read MoreAutomotive Awards Highlight Emerging Technologies
Annual SPE Automotive event gives nods to several ‘firsts’ as well as sustainability.
Read MoreRead Next
Tension-Indicating ‘Smart’ Bolts Make Mold Mounting Safer, More Efficient
No more guessing about whether mold-mounting bolts are tightened properly, with an alternative to unreliable torque measurements.
Read MoreWhy Shoulder Bolts Are Too Important to Ignore (Part 1)
These humble but essential fasteners used in injection molds are known by various names and used for a number of purposes.
Read More