Why Five-Axis Cartesian Robots Are a Hit with Molders
Five-axis linear robots are proving to be a cost-effective alternative to six-axis articulated robots in many applications.
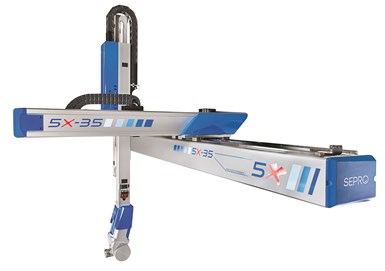
Why is five better than three—or six? When it comes to robot axes of motion, October’s Fakuma 2014 show in Germany provided some answers. Sepro Robotique of France (U.S. office in Warrendale, Pa.) said it has seen sales of five-axis Cartesian robots take off. Such robots are more capable than standard three-axis linear robots and often are a more cost-effective choice than a six-axis articulated robot (which Sepro also offers).
Based on a standard three-axis Cartesian beam robot, Sepro’s 5X line adds a two-axis servo wrist developed in partnership with Staubli Robotics (U.S. office in Duncan,
S.C.). In the two years since the 5X line was introduced at Fakuma 2012, Sepro says sales of these units have grown nine-fold and were expected to double 2013’s sales last year. It is by far the company’s fastest-growing new product line. According to CEO Jean-Michel Renaudeau, “We are seeing molders buying five-axis models even when they don’t have a need for them today, because they expect to in the future.”
IT’S ALL IN THE WRIST
There are several reasons for this popularity:
• Molders increasingly require high accuracy and flexibility in gripping and downstream positioning. Loading multiple inserts at high speeds, or multiple motions to demold complex parts in a tight mold space are facilitated by the extra axes. The same goes for secondary operations like passing the edge of a part past a flaming fixture or placing parts in trays in different positions. And unlike a pneumatic wrist, the servo wrist can grip parts at any angle and perform multiple servo motions in synchronization with other robot movements.
• Another benefit is adaptability to different molds and machines. Ability to reprogram servo motions in software is especially helpful for custom molders dealing with transfer tooling that they did not design, or that must run a given mold in different machines to meet scheduling requirements.
• The servo wrist boasts clean operation, suitable for medical and other applications that cannot tolerate particulates resulting from drive-belt wear or lubricant contamination.
• High accuracy and repeatability are afforded by servo wrist operation with a positional encoder that recognizes exactly where the drive shaft is at any moment. And the system control can integrate positional signals from all of the servo motors on all five axes so that it knows exactly where the gripper and part are in space at all times.
• Many of the complex part manipulation tasks mentioned above have historically been assigned to six-axis articulated-arm robots. But a linear Cartesian robot offers faster access to the mold space and simpler programming.
HOW TO MOLD A CUP FILLED WITH WATER
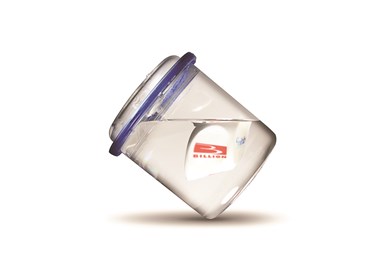
This cup comes out of the mold sealed, filled with water, and with a plastic object bobbing inside. A Sepro 5X robot inserts the floating piece, dispenses the water, and removing the finished part. This involves several lateral motions and two rotations inside the mold area
These capabilities were demonstrated at the booth of Billion, the French injection machine builder, where a Sepro 5X robot was mounted on a Billion Select 200 all-electric two-shot press. This demonstration of in-mold assembly involved multi-shot injection (a Billion specialty) to encapsulate a liquid (water) inside a closed, cup-like container with dice floating inside. The mold, built by MIHB in France,
uses two rotating plates for a multi-step process (see it on YouTube here):
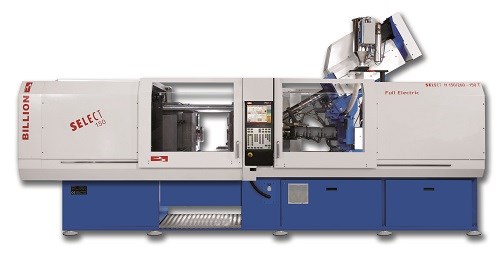
This Billion Select 150T all-electric, two-component press injects clear and colored copolyester to make the cup body and lid.
1. The machine injects the top and bottom of the container on opposite sides of the mold. One of the two rotating plates holds the lid of the cup and a finished part. The other rotating plate holds the body of the cup. One plate nests into the moving half of
the mold and the other into the stationary half, but both are connected by a shaft to the moving half of the mold.
2. The mold opens and the two rotating plates index forward and turn 180° to bring the two parts of the cup in line with each other. One plate retracts again into the stationary mold half, and the Sepro robot descends and removes the finished part and turns 180° to insert the dice into the body of the new cup.
3. The plate holding the bottom half of the cup retracts against the other plate, holding the two parts of the cup together with mild pressure. Meanwhile, the robot turns 90° and moves laterally to insert the end of a long filling nozzle into a hole in the lid of the cup.
Water is dispensed to fill the cup about two-thirds full.
4. The robot retracts and the mold halves clamp together, and the second Billion injection unit overmolds the seam between the cup halves to create a water-tight seal.
5. The mold opens so the finished part can be removed and the cycle repeats.
In this demo, the robot performs multiple functions: inserting the dice, filling the part with water, and removing the finished part. This involves several lateral motions and two rotations inside the mold area.
The material was Eastman’s Tritan clear copolyester for the lid and body, and Tritan with color masterbatch for the overmolded seal.
Related Content
Arburg Open House Emphasizes Turnkey Capabilities
Held at the company’s U.S. headquarters in Rocky Hill, Connecticut, the event featured seven exhibits, including systems that were designed, sourced and built in the U.S.
Read MoreTederic Promotes High Technology, Broader Market Presence
Four cells are running in its booth including a 1,300-ton multimaterial system highlighting its 2K capabilities.
Read MoreAbsolute Haitian Brings Next Generation of Presses to Orlando
NPE2024: Absolute Haitian says Generation 5 of the servo-hydraulic Haitian and electric Zhafir machines lines emphasize efficiency, performance and intelligence.
Read MoreU.S. Debut for Slimmed Down Electric Machine
NPE2024: Arburg’s debut of the 310-ton Allrounder 720 E Golden Electric extends the tonnage range of the electric series and marks the first global press premiere outside of Germany.
Read MoreRead Next
See Recyclers Close the Loop on Trade Show Production Scrap at NPE2024
A collaboration between show organizer PLASTICS, recycler CPR and size reduction experts WEIMA and Conair recovered and recycled all production scrap at NPE2024.
Read MorePeople 4.0 – How to Get Buy-In from Your Staff for Industry 4.0 Systems
Implementing a production monitoring system as the foundation of a ‘smart factory’ is about integrating people with new technology as much as it is about integrating machines and computers. Here are tips from a company that has gone through the process.
Read MoreMaking the Circular Economy a Reality
Driven by brand owner demands and new worldwide legislation, the entire supply chain is working toward the shift to circularity, with some evidence the circular economy has already begun.
Read More