Addifab Announces Partnership, Micromolding Offering, PIM Viability
The Danish company’s novel additive manufacturing technology that prints dissolvable injection mold inserts from a UV-cured resin had a busy finish to 2020.
The novelty of Addifab’s Freeform Injection Molding (FIM) technology, where additive manufacturing is used to build heretofore impossible injection mold cavities from a UV-hardened polymer, continues to open up new opportunities and partnerships. Most recently, the Danish firm with U.S. offices in Palo Alto, Calif. announced a collaboration with Mitsubishi Chemical Advanced Materials. It also shared promising results using its molds in metal and ceramic powder injection molding, and introduced a new high-resolution printing module targeting micromolding.

Lattices and FIM molds in a range of materials, including TPE, ABS, PMMA and glass-filled PPS and PA66.
FIM allows designers to print injection molding cavities from a dissolvable UV-hardening liquid acrylic resin using the company’s Addline system. After printing, the molds are cleaned and flushed to remove residual resin. The molds can then be post-cured via light beam. These printed cavities can then be placed into standard injection molding machines running standard resins, which is a big part of their appeal, allowing users to rapidly iterate various tool/part designs and run already approved resins, with the tool dissolved away to reveal finished parts with truly novel shapes and features. Standard components can also be manufactured just as easily, noted Carsten Jarfelt, CEO of Addifab U.S.
Mitsubishi Adds Addifab
Starting in the latter half of 2020, Mitsubishi Chemical Advanced Materials has started offering services based on Freeform Injection Molding from three locations. Mitsubishi said select customers will be able to use its materials in conjunction with FIM-as-a-service from its Mesa, Az.; Tielt, Belgium; and Nagoya, Japan manufacturing sites. Mitsubishi Chemical Advanced Materials offers metal replacement polymers, specifically its KyronMAX materials, which include PC, PA 66, PPA, PEI, PPS and PEEK. The company supplies high-performance thermoplastic materials in the form of semi-finished products and finished parts.
“FIM lets the injection molder create injection molded objects with the same design freedom offered by conventional 3D-printing,” Addifab’s founding CEO Lasse Staal said in a release. “We have brought 3D-printing lead-times and start-up costs to the injection molding industry, without compromising on the choice of materials.”
Randy White, chief innovations officer at Mitsubishi Chemical Advanced Materials said his company’s “aha” moment came when a 70g lattice molded from KyronMAX in an Addifab mold was able to withstand being driven over by a pickup.
Micromolding Tools Targeted
The company also announced a new machine capable of printing mold inserts for micromolding parts. The AddLine Micro upgrade package allows the company’s printing machine to reduce resolution from 50 down to 10 µm. As Addifab points out in a release announcing the the new high-resolution upgrade, the nominal feature now achievable is smaller than a white blood cell.
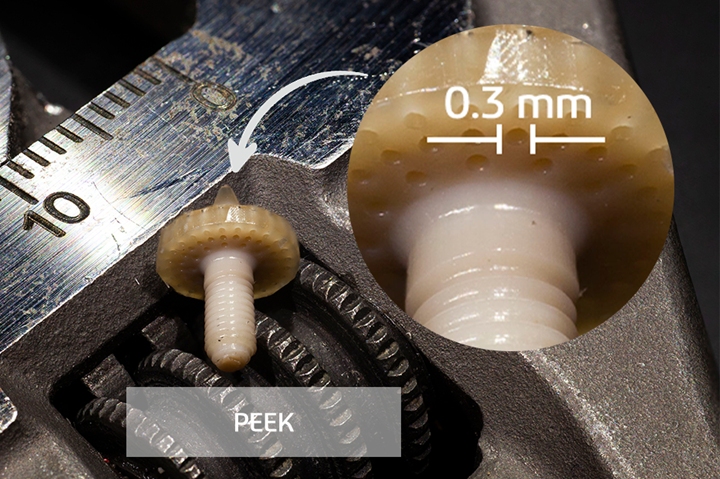
This micromolded PEEK component made in a printed Addifab mold, features 0.3-mm holes.
Noting its roots in the hearing aid industry, Addifab said in the release that miniaturization remains one of the hottest trends in the medical device industry. The Add-Line Micro package will be offered to select beta customers in the first quarter of 2021.
PIM Viability Validated
In a paper given at the MIM Advanced Processes Session during Euro PM2020 researchers from Addifab and Germany’s Fraunhofer Institute showed that FIM could be used in powder injection molding (PIM). Axel Müller-Köhn, Eric Schwarzer and Tassilo Moritz of Fraunhofer and Uffe Bihlet and Kyriakos Didilis from AddiFab specifically looked at molding a part from an alumina ceramic feedstock in an FIM polymer tool.
The researchers noted that in a normal PIM tool, larger draft angles, a high degree of rounding and larger gates often need to be designed into the cavity to ease demolding. The dissolvable FIM mold obviates those design elements.
In the experiment, the researchers molded an 18-mm bone screw from alumina powder. The mold was printed with a layer thickness of 50 μm, building up 200 layers with a full print time of 1 hour. A Boy 35 E VV vertical molding machine ran the mold, which was manually placed within a Meusburger mold base. The nozzle temperature used for molding was 170 C, with a tool temperature of 90 C. The maximum injection pressure was 950 bar, with a holding pressure of 500 bar, injection time of 0.3 sec and a cooling time of 30 sec.

This image shows the steps taken when applying Freeform Injection Molding (FIM) to a powder injection molding.
Post molding, the tool was dissolved and then came chemical and thermal debinding for the “green” component. The sintered parts were defect free and had comparable shrinkage behavior to that of conventionally produced PIM parts. The researchers said they were slightly—but uniformly—undersized based on the feedstock specification, but this could be accounted for in the design phase.
“The FIM approach is fully compatible with PIM,” the paper states. “The application of commercial feedstocks and standard thermal processing is possible, and the resulting parts have shapes, sizes and finishes similar to those produced by conventional methods.”
Related Content
Freeform Injection Molding Eases the Path to Medical Device Product Testing
A development and manufacturing service provider is using dissolvable molds to build injection molded silicone prototypes.
Read More420 Stainless Steel Now Qualified With TrueShape 3D Printing Technology
NPE2024: Mantle's additive manufacturing technology is designed for precision tooling.
Read MoreMedical Manufacturer Innovates with Additive Manufacturing and Extrusion Technology Hubs
Spectrum Plastics Group offers customers two technology hubs — one for extrusion, the other for additive manufacturing — to help bring ground-breaking products to market faster.
Read MoreThe Connector Conundrum: 3D Printed Mold Tooling’s Role in Innovation
ReelView Fishing faced an electronics obstacle in the development of its new technology for underwater video. Additive manufacturing for moldmaking allowed for the speed necessary to iterate to a solution. How inventors and invention will benefit from new ways of obtaining production-ready tooling.
Read MoreRead Next
Injection Molding & 3D Printing Combine to Make ‘Impossible’ Parts
Stereolithography cavity inserts can be injected with thermoplastic, then removed from the mold and dissolved away to leave a complex-shaped part.
Read MoreSee It Live: The Ultimate Crossover of Injection Molding & 3D Printing
AddiFab, Mitsubishi Chemical and Alba Enterprises to demonstrate Freeform Injection Molding at Rapid + TCT show in May.
Read MoreBeyond Prototypes: 8 Ways the Plastics Industry Is Using 3D Printing
Plastics processors are finding applications for 3D printing around the plant and across the supply chain. Here are 8 examples to look for at NPE2024.
Read More