Equipment Supplier Sees Demand for Circular Plastics Gathering Momentum
VDMA interviewed Martina Schmidt, head of recycling business unit at Vecoplan AG
Vecoplan AG is a supplier of industrial shredders and material handling equipment. The company’s US subsidiary is Vecoplan LLC. Plastics Europe Deutschland is the German division of the European plastics trade organization. As part of a series of interviews leading up to the K Show, (the German mechanical engineering trade association) spoke with its head of recycling business, Martina Schmidt.
Ms. Schmidt spoke of the increased demand for recycled materials seen by Vecoplan customers, as well as the challenge of the shortfall of available recyclates. Schmidt described how recyclers are dealing with the challenges, and the potential for circularity to reduce environmental impact and improve the public image of plastics. The full text of the interview is included below.
VDMA: Ms. Schmidt, is the circular economy gaining momentum?
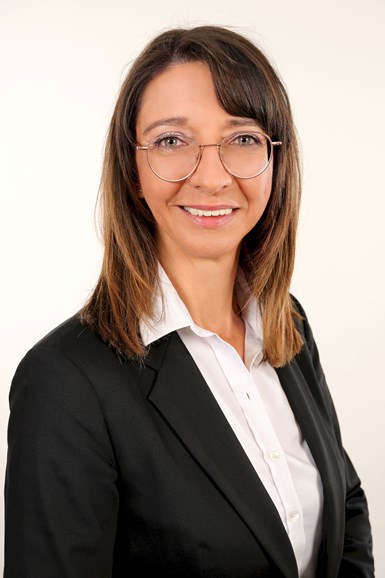
Martina Schmidt, head of recycling business unit at Vecoplan. Photo: Vecoplan AG
Schmidt: Yes, this great collaborative project has picked up enormous pace. The circular economy is now perceived very differently from just a few years ago. Everyone has understood that it's not just about functional waste management, but that all players in the market need to take part. This begins with product design, continues with politics (keyword: recycling quota), and finishes with the end consumer. Today, people are aware that the entire value chain must take action if we are to fight climate change and protect the environment.
VDMA: From which sector is Vecoplan seeing this additional, awareness-driven demand?
Schmidt: The demand is all across the board. It is not limited to certain sectors, because the entire plastics industry is undergoing changes. The main impetus stems from the recycling rate. The plastics industry has to come to terms with the fact that, in future, the product that is launched onto the market will contain recyclate as well as being recyclable itself. This development is being driven from both sides: both the producer and the customer are now looking for recycling concepts. The trend towards individual cycles will change everything in a sustainable manner.
VDMA: What are the consequences?
Schmidt: The demand is high, but there are not enough recyclates to meet those demands. The situation is currently being exacerbated by the fact that large corporations are creating these closed loops themselves. They then know the products that are in the loop, they know the manufacturing process, and the remanufacturing process. They know how the product comes back from the customer and how they can recycle it within their own loop. So, a large amount of potential recyclate does not reach the market.
VDMA: How can you counteract this?
Schmidt: Our customers are experiencing shortages of materials and rising prices. As an alternative, they are looking for other material streams of the same material that are also recyclable. In the polyolefin sector for example, these are big bags, filaments, yarns, non-wovens. These materials are available in sufficient quantities, but until now there has been no need to focus on them. This raises the question of where these material streams come from, what their mechanical and thermal characteristics are, and what process must be set up to recycle them. Through our decades of experience and expertise, we are capable of fully supporting our customers in this field.
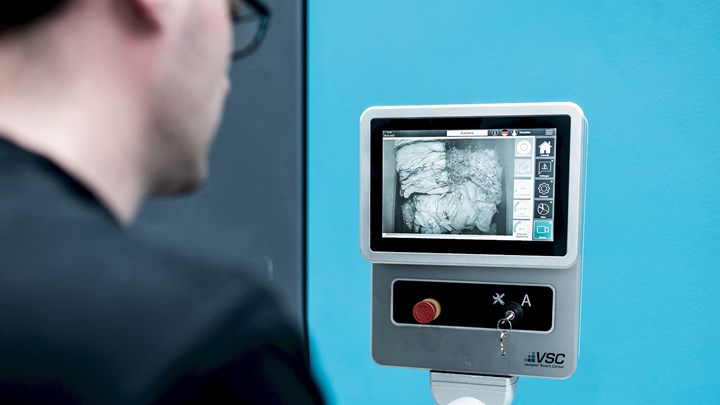
Vecoplan’s smart center displays camera feed from inside the machine.
Photo Credit: Vecoplan AG
VDMA: Can post-consumer plastics also be used to produce high-quality recyclates?
Schmidt: Basically, the answer is yes. The question is: how intensively would I want to do it, and what are my expectations of the end product? For example, I make a distinction between whether the packaging is produced for the food sector or for goods for everyday use.
VDMA: What part of the plastic material has already been tapped and how great is the potential?
Schmidt: The share of established cycles, and quantities that are processed in them is absolutely small compared to the quantities of materials that enter the market and are not yet recycled. The potential for recycling is quite considerable.
VDMA: What is Vecoplan’s response to changing customer requirements?
Schmidt: As in the other business areas at Vecoplan, the team in our business area consists of the highest-level specialists, which include plastics and application engineers, mechanical engineers, sales professionals, and project managers. It’s not solely a great deal of technical know-how that we collate within the business unit, but also extensive personal experience. In close cooperation with our customers, we offer the possibility of running test series with customer material and coordinating individual concepts in our technology center. For us as a machine and plant manufacturer, the circular economy is a great opportunity for actively shaping change.
VDMA: Will a well-functioning circular economy lead to a better image for plastic?
Schmidt: That will certainly be the case. Plastic does not deserve its bad image. It makes an important contribution to climate protection. A study by Fraunhofer Institute UMSICHT concluded that replacing virgin granulate with recycled material in packaging will reduce climate-damaging greenhouse gases by up to 60 percent. We should learn to make use of the advantages of plastic and, on the other hand, ensure that it does not end up in the environment. The circular economy will contribute significantly towards achieving this.
Related Content
Reversing Logistics for Plastic Film Recycling
Learn how Mainetti built a circular supply chain for clear film packaging.
Read MoreEvolving Opportunities for Ambitious Plastics Recycler
St. Joseph Plastics grew from a simple grinding operation and now pursues growing markets in recycled PP, food-grade recycled materials, and customized post-industrial and post-consumer compounds.
Read MoreExtrusion Technology Extended to Injection, Enabling Up to 100% Regrind Usage
Twin-barrel (shot-pot) press can handle more regrind, offers other benefits to molders.
Read MoreOptical Sorting for Color Flexibility in Recycled Plastics
Aaron Industries added optical sorting to its operation, expanding capabilities to meet the color needs of customers.
Read MoreRead Next
Lead the Conversation, Change the Conversation
Coverage of single-use plastics can be both misleading and demoralizing. Here are 10 tips for changing the perception of the plastics industry at your company and in your community.
Read MoreBeyond Prototypes: 8 Ways the Plastics Industry Is Using 3D Printing
Plastics processors are finding applications for 3D printing around the plant and across the supply chain. Here are 8 examples to look for at NPE2024.
Read More