Ford Converts 3D Printing Scrap into New, Molded Parts
Ford has collaborated with HP to reuse spent 3D printed powders and parts turning them into injection molded vehicle parts.
Ford and HP announced a collaboration that transforms 3D waste into new auto parts, including components for Super Duty F-250 trucks. The spent 3D printing powders and parts are being used to injection mold fuel-line clips installed first on Super Duty F-250 trucks.
Ford reports that these parts have better chemical and moisture resistance than conventional versions, while also being 7% lighter and costing 10% less. The OEM’s research team has identified 10 other fuel-line clips on existing vehicles that could also apply the new reclaimed material stream.

Ford and HP worked with SmileDirectClub to gather and reclaim the spent powder and parts from the printing of teeth aligners.
Debbie Mielewski, Ford technical fellow, sustainability, noted in a release that this project creates a high-value application for waste powder that likely would have gone to landfill, transforming it instead into functional and durable auto parts.
HP said that its 3D printers, which Ford uses at its Advanced Manufacturing Center, are designed for high efficiency with minimal waste, but working with Ford, they can push the printers to zero waste.
Three other companies helped Ford and HP complete the project, which came together in less than a year. SmileDirectClub, which operates the largest facility of HP 3D printing systems in the U.S. in the creation of oral care and teeth straightening products, participated. The company’s fleet of more than 60 HP 3D printers produces more than 40,000 aligners a day, with the resulting scrap 3D printed parts collected and recycled with HP.
Resin producer Lavergne then transforms those molds and discarded powder from Ford’s HP 3D printers into high-quality recycled plastic pellets, suitable for injection molding. The pellets are then molded into fuel-line clips by Ford supplier ARaymond, who designs, engineers and manufactures assembly systems.
Ford is developing new applications and utilizing a multitude of 3D printing processes and materials, including filaments, sand, powders and liquid vat polymerization. The auto maker already uses 3D printing for a variety of low-volume commercial vehicle parts, as well as fixtures used by assembly line workers.
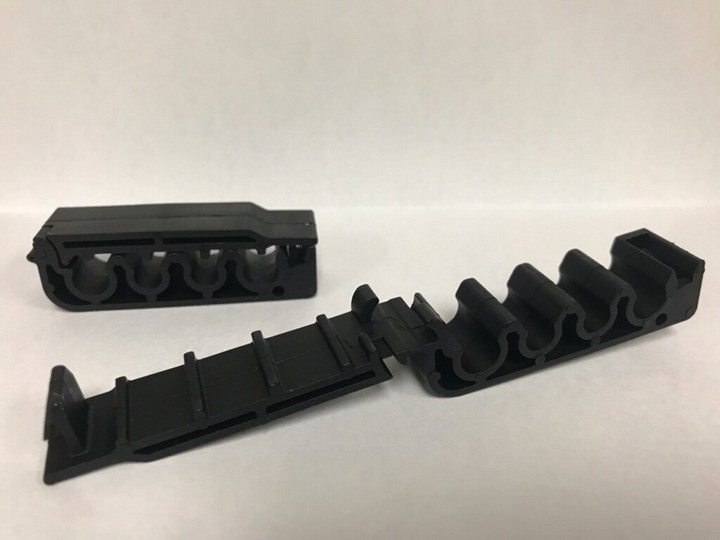
Ford says the parts molded from reclaimed 3D printing scrap have better chemical and moisture resistance than conventional versions, while also being 7% lighter and costing 10% less.
Related Content
-
Freeform Injection Molding Eases the Path to Medical Device Product Testing
A development and manufacturing service provider is using dissolvable molds to build injection molded silicone prototypes.
-
DuPont Buys Medical Product Manufacturer Spectrum Plastics
Purchase price of $1.75 billion for leading supplier of extruded, molded, and 3D printed medical components.
-
NPE 2024: Additive Manufacturing Assisting, Advancing Plastics Processing
Exhibitors and presenters at the plastics show emphasized 3D printing as a complement and aid to more traditional production processes.