Pure Loops Shredder-Extruder Delivers Impressive Recycling of Challenging Production Waste
Erema’s Pure Loop technology can efficiently handle thin-walled HDPE drip tapes and HDPE irrigation pipes.
The shredder-extrusion combination from recycling technology Pure Loop, subsidiary of Austria’s Erema Group (U.S. office in Ipswitch, Mass,) reportedly is proving to be an ideal solution for recycling challenging production waste. This includes HDPE drip tapes and HDPE irrigation pipes that accumulate as waste during the production of irrigation systems or are rejected during quality control inspection. Pure Loop has shown that manufacturers who already implement this technology, reuse production waste in the form of recycled pellets in proportions of up to 20% without any loss of quality compared to production from virgin material.
Said Pure Loop managing director Manfred Dobesberger, "This level of reuse can still be significantly increased thanks to the high- quality of the recycled pellets. The high demands on the recycling process result from the high volume of the bulky input material as well as the material composition of the drip tapes and irrigation pipes.” Their job is to ensure that crops can grow and thrive, using as little water, fertilizer and pesticides as possible. For this purpose, either thin-walled HDPE drip tapes laid on the surface or HDPE irrigation pipes buried in the ground are used. The water is distributed through emitters.
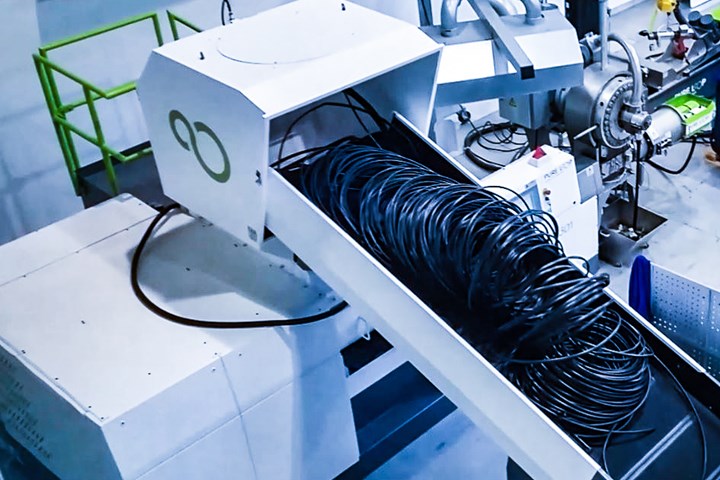
In the case of the thin-walled drip tapes (150-250 µm/5.9-9.8 in.), these are LLDPE injection-molded parts which are spaced at regular intervals of around 20 cm/7.8 in.. In the case of thick-walled irrigation tubes (over 300 µm/11.8 in.), the emitters are also fitted with a silicone membrane for pressure compensation, so that the same flow rate of water is discharged from each emitter over the entire length of the tube and the flow of water is not obstructed by soil, sand or roots growing into the emitter.
The purpose-specific function of the pipes and tapes is tested at regular intervals during the production process. Reported Pure Cycle’s Manfred Dobesberger, "In order to test whether their irrigation pipes meet the strict quality standards of a maximum of two pinholes per 10 kilometers/6.2 miles, one of our customers pressure-tests them with water. The proportion of foreign polymers in this material is a real challenge in recycling, but one that our ISEC evo shredder-extruder combination with double degassing and Erema laser filter can handle with perfectly.”
In the laser filter, three scrapers rapidly and continuously remove contaminants--which mainly consist of the silicone in the emitters, from the filter screen during each revolution. The efficiency of this filter reportedly enables high throughput rates in the recycling process and the highest recycled pellet quality. Further advantages for the user are that, as an all-rounder, the recycling machine processes bulky hose bundles as well as other production waste such as start-up lumps and regrind material or complete rolls with drip tapes. Single-shaft shredders and double feed ram systems flexibly adapt to individual logistic requirements and, thanks to the conical transition to the extruder, the material is compacted and oxygen is reduced, which ensures the plastic material is processed very gently. The entire ISEC evo series also offers straightforward operation and a high degree of automation, and the machines are quickly ready to start processing at any time.
This overall recycling concept reportedly has already impressed irrigation system producers in the U.S., Israel, Italy and Mexico. They operate recycling plants with throughputs of 100 to 500 kg/h (224 to 1102 lb/hr) and reuse the recycled pellets produced in proportions of up to 20% in the production process of thin-walled tapes and thick-walled pipes. However, practical tests have shown that significantly higher proportions of recycled pellets would be possible in the end product. "Even for very thin drip tapes with a wall thickness of 100 µm/3.9 in., we were able to use a proportion of 10% recycled pellets in a 48-hour trial without any loss of quality," said Dobesberger.
Related Content
Looking to Run PCR on a Single Screw? Here’s What to Keep in Mind
Just drop it in and mix it up? Sorry, there’s a lot more to it than that. Here is some of what you need to consider.
Read MoreMultilayer Solutions to Challenges in Blow Molding with PCR
For extrusion blow molders, challenges of price and availability of postconsumer recycled resins can be addressed with a variety of multilayer technologies, which also offer solutions to issues with color, processability, mechanical properties and chemical migration in PCR materials.
Read MoreOptical Sorting for Color Flexibility in Recycled Plastics
Aaron Industries added optical sorting to its operation, expanding capabilities to meet the color needs of customers.
Read MoreEvolving Opportunities for Ambitious Plastics Recycler
St. Joseph Plastics grew from a simple grinding operation and now pursues growing markets in recycled PP, food-grade recycled materials, and customized post-industrial and post-consumer compounds.
Read MoreRead Next
See Recyclers Close the Loop on Trade Show Production Scrap at NPE2024
A collaboration between show organizer PLASTICS, recycler CPR and size reduction experts WEIMA and Conair recovered and recycled all production scrap at NPE2024.
Read MoreFor PLASTICS' CEO Seaholm, NPE to Shine Light on Sustainability Successes
With advocacy, communication and sustainability as three main pillars, Seaholm leads a trade association to NPE that ‘is more active today than we have ever been.’
Read More