X2F Taps Mold-Masters Veteran as New Technology Director
Amidst a commercialization push, the Loveland, Colo. based creator of a new injection molding technology announced Ken Jacob as its new technology director.
Injection molding technology supplier X2F (Loveland, Colo.) has appointed plastics industry veteran Ken Jacob as its Director of Technology. The appointment was announced in a press release by Rick Fitzpatrick, X2F founder and Chief Technology Officer (CTO).
Jacob has more than 25 years of experience in product development, machine design, engineering, and hot runner systems. Most recently, he served as the Global Manager of Master Solutions at Mold-Masters Ltd., with responsibility for engineering groups in North America, Europe, India and Asia.
X2F’s molding technology, which applies controlled viscosity and “pulse-packing”, reportedly enables the manufacture of complex product designs using previously difficult-or-impossible-to-mold materials. X2F says controlling viscosity dramatically reduces material degradation and molded-in stress more common in conventional molding technologies.
X2F said current commercialization of the technology is occurring in optics, overmolded electronics, and highly filled engineering resin applications. For optical applications, like mobile phone lenses, X2F says its process produces parts with reduced birefringence and anisotropic shrink. In automotive lighting applications, the X2F process can produce complex geometries, thicker lenses, and larger shapes. In encapsulated electronics applications, the X2F process allows for fewer production steps. In compounds, X2F says its process allows increased loadings of functional fillers, such as glass or carbon fiber.
X2F says its technology has produced nearly three million commercial parts for the medical, industrial, automotive, and consumer electronics industries.
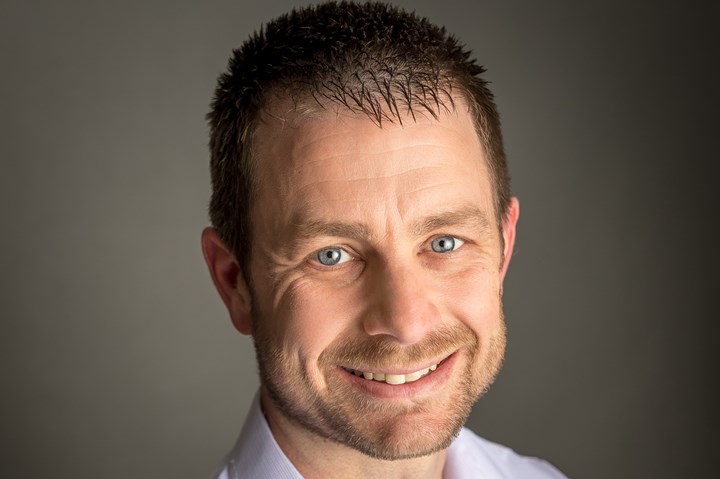
X2F’s new technology director, Ken Jacob, has more than 25 years of plastics industry experience, most recently with Mold-Masters.
Related Content
-
Three Key Decisions for an Optimal Ejection System
When determining the best ejection option for a tool, molders must consider the ejector’s surface area, location and style.
-
Back to Basics on Mold Venting (Part 2: Shape, Dimensions, Details)
Here’s how to get the most out of your stationary mold vents.
-
What to Look for in High-Speed Automation for Pipette Production
Automation is a must-have for molders of pipettes. Make sure your supplier provides assurances of throughput and output, manpower utilization, floor space consumption and payback period.