All-Electric Press Gets U.S. Debut
NPE2024: For the first time, Arburg is making a global premier of a machine outside Germany with the new Allrounder 720 E Golden Electric among its 13 exhibits — seven in its own booth — in Orlando.
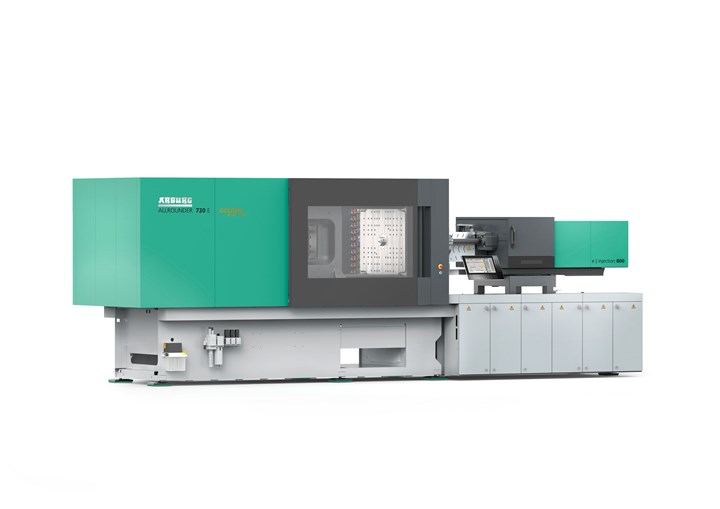
Arburg will introduce the newest machine in its Allrounder Golden Electric line at NPE2024. Source: Arburg
Saying the machine and the market are of “great strategic importance,” Arburg is premiering its Allrounder 720 E Golden Electric at NPE2024, noting this is the first global launch of a new machine outside of Germany. The all-electric machine with 310 tons of clamp force is among 13 exhibits for Arburg, with seven of those in its own booth. In a release, Gerhard Böhm, managing director sales and aftersales at Arburg, said the fact that the company is premiering the new Golden Electric at NPE2024 “reflects the great importance of the American market for Arburg.”
Featuring servo-electrically driven injection/metering and mold opening/closing, the Golden series is positioned by Arburg as providing an outstanding price/performance ratio and ready availability thanks to its design, which the use of standardized components. To date, the Allrounder Golden Electric series includes four models, ranging in clamp size from 65 to 220 tons with tiebar spacing from 14.57 by 14.57 inches up to 22.44 by 22.44 inches. The Allrounder 720 E Golden Electric will supplant the 570 E as the largest model in the line.
Arburg says the Allrounder 720 E Golden Electric’s design has been optimized, resulting in a significantly smaller footprint compared to other machines in its class. The machine can target a wide range of plastic parts and cycle times of around 15 seconds or more, with typical applications in medical technology, mobility and technical injection molding. At NPE2024, an Allrounder 720 E Golden Electric will run a 24-cavity mold to produce razor covers, with a Multilift V 30 linear robot system removing parts.
IML, Cube Molds and More
In addition to the new Allrounder 720 E Golden Electric, Arburg’s machine exhibits at its own booth and those of partners will include a new precise in-mold labeling (IML) process designed specifically for medical technology displayed on a cleanroom-designed electric Allrounder 520 A production cell molding labeled centrifuge tubes.
For the first time in the U.S., an Allrounder Cube 1800 machine will be presented, using an integrated 6-axis robot to produce two-component medical closures fully automatically. Positioned as an energy-efficient alternative to thermoforming, an Allrounder 720 A Ultimate electric packaging machine will mold IML round cups with a wall thickness of 0.015 inch using injection compression molding at an injection pressure of just 23,000 psi.
An Allrounder More 2000 two-component Allrounder equipped with an integrated six-axis robot will combine thermoplastic and optical LSR in a pair of glasses. Elsewhere, an Allrounder 520 H “Premium” featuring new hybrid machine technology processes and using the company’s recyclate package will mold 100% ABS recyclate into components for a 1:18 scale Allrounder model. Patient showgoers will be able to take home an Arburg-designed toolbox featured at other shows globally produced on a hybrid Allrounder 920 S turnkey system. In additive manufacturing, a 750-3X high-temperature Freeformer will be demonstrating industrial additive manufacturing.
Digitization
On the digitalization front, all Allrounders at the show will be networked with the Arburg ALS host computer system via OPC UA interfaces. With this central MES, the entire plastic parts production process can be digitally planned and controlled, with relevant information tracked. Arburg’s Jürgen Peters, director of software development, will give a presentation on the advantages of integrating peripherals via OPC UA on May 7 at the “Innovation Stage” in Orlando.
Related Content
LS Mtron’s Outsized NPE2024 Presence Jump-Starts Ambitious North American Market Goals
The Korean maker of injection molding machines featured eight machines in its nearly 14,000-square-foot booth with additional presses at Yushin and Incoe’s booths, as it targets 20% market share.
Read MoreIPEX Opens Injection Molding Facility in North Carolina
The pipe and fittings manufacturer’s new 200,000-square-foot facility represents a $200 million investment and will create 150 jobs.
Read MoreArburg Open House Emphasizes Turnkey Capabilities
Held at the company’s U.S. headquarters in Rocky Hill, Connecticut, the event featured seven exhibits, including systems that were designed, sourced and built in the U.S.
Read MoreScaling New Heights With Vertical Integration
Eden Manufacturing was founded on a vision of vertical integration, adding advanced injection molding capabilities to a base of precision moldmaking and more recently bringing Swiss-type machining capabilities in-house.
Read MoreRead Next
Fakuma 2023: Arburg Extends Hybrid Range, Introduces New Service
Arburg will have nine exhibits on its own stand and another 10 machines on partner stands with live demonstrations of applications, processes and trends in injection molding and 3D printing.
Read MoreAnswering the Sustainability Challenge with Digitalization
Attendees in the molding halls of K can count on exhibits that address two main themes: digitalization and sustainability. Digitalization in the form of smarter pieces of equipment communicating with each other and with plant personnel; and sustainability in the form of greater energy efficiency and the ability to process recycled and renewable resins.
Read MoreMaking the Circular Economy a Reality
Driven by brand owner demands and new worldwide legislation, the entire supply chain is working toward the shift to circularity, with some evidence the circular economy has already begun.
Read More