Automation: Cobot Adds Interface for Easier Integration With Injection Molding Machines
Universal Robots has developed an Injection Molding Machine Interface (IMMI) supported by EUROMAP 67 and SPI AN-146 communication protocols, simplifying cobot/machine integration.
In response to increased growth in the market, Universal Robots (UR; U.S. headquarters in Ann Arbor, Mich.) has developed an Injection Molding Machine Interface (IMMI) to make communication between its e-Series cobots and molding machines fast and easy. Compatible with EUROMAP 67 and SPI AN-146 communication interfaces, the new IMMI eliminates the need for a hardwired connection with discrete IOs and the development of custom application software to map those IO points coming to and from the injection molding machine. Newer model (made in 2020) e-Series robots using the IMMI can now simply plug in and use a standard interface to communicate.

Universal Robots’ new injection molding machine interface eliminates the need for hardwired connection with discrete IOs.
With the IMMI, UR says molders have the ability to set up, program and control the entire application cycle through the cobot’s teach pendant. The company says the IMMI can be installed into the UR cobots’ control box in less than 10 minutes, using the e-Series control box expansion port for mounting and cable management. To install, a ribbon cable e-connects to the extension bus on the control box, and a 6 meter long cable then connects to the injection molding machine. An IMMI template for the Universal Robots Polyscope operating system is also provided in the programming tree. The IMMI is currently available through UR’s UR+ platform of products certified to work with UR cobots.
Citing market research the company commissioned, UR said in a virtual press conference held to announce the new IMMI that 15% of all cobot applications in 2020 will be in injection molding, automating tasks such as placing inserts into molds and moving parts through post-mold processes.
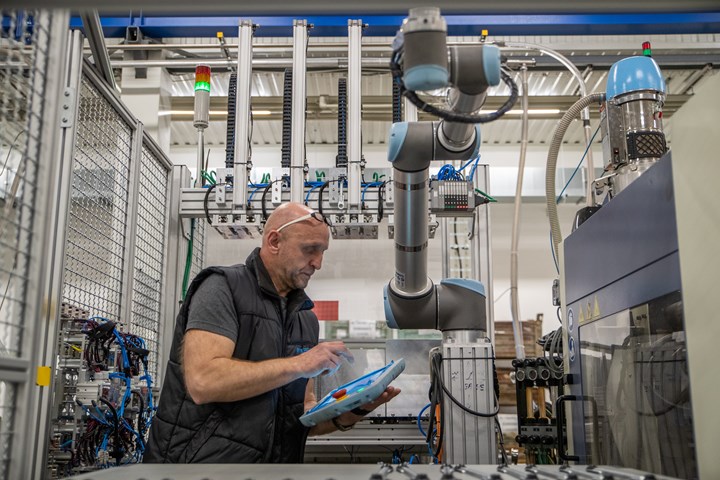
Automotive molder 2K Trend recently deployed a UR10 for machine tending.
Related Content
-
Ensuring Repeatability: The Key to Effective Injection Molding Automation
One of automation’s key promises is repeatability: the same movement to the same location, time and time again. But to achieve that, all elements involved — robot, machine, EOAT, mold — must be in and stay in alignment.
-
Adding Remote Service Functions for PET Bottle Blowing
KHS has added features to its internet machine communications portal for PET stretch-blow molding.
-
Open Automation Enables Flexibility in Chemical Recycling
Software-defined equipment control systems can be duplicated, transferred and scaled with ease.