Chillers Feature Redundant Design
Delta T Systems makes built-in redundancy—including a second refrigeration unit and parallel components—an option for its full line of air- and water-cooled process chillers ranging from one to 15 tons.
Industrial chiller manufacturer Delta T Systems now offers built-in redundancy as an option for its full line of air- and water-cooled process chillers ranging from one to 15 tons of cooling, adding a second chiller into one cabinet with full component redundancy.
Delta T notes that maintaining an extra chiller for each operation is the ultimate failsafe, but double the investment, whereas a process chiller with built-in redundancy provides the same level of protection against downtime with less initial cost. Also, where many manufacturers’ redundant chillers integrate a second refrigeration circuit as a backup and to improve energy efficiency, the unit is still vulnerable to other component failures.
Delta T Systems chillers with built-in redundancy avoid this by featuring two full chiller circuits with a single tank connected to and from the process. The redundant chiller has two compressors, two evaporators, two condensers, two water pumps and two controllers, among other key components.
Delta T Systems’ redundant chillers alternate between the two water pumps every 100 hours, with both refrigeration circuits constantly running, each at 50% of the required cooling. The company says this process is more energy efficient than alternating between the two, and regularly using both circuits in cooling equalizes compressor runtime and confirms that the backup circuit is fully functional.
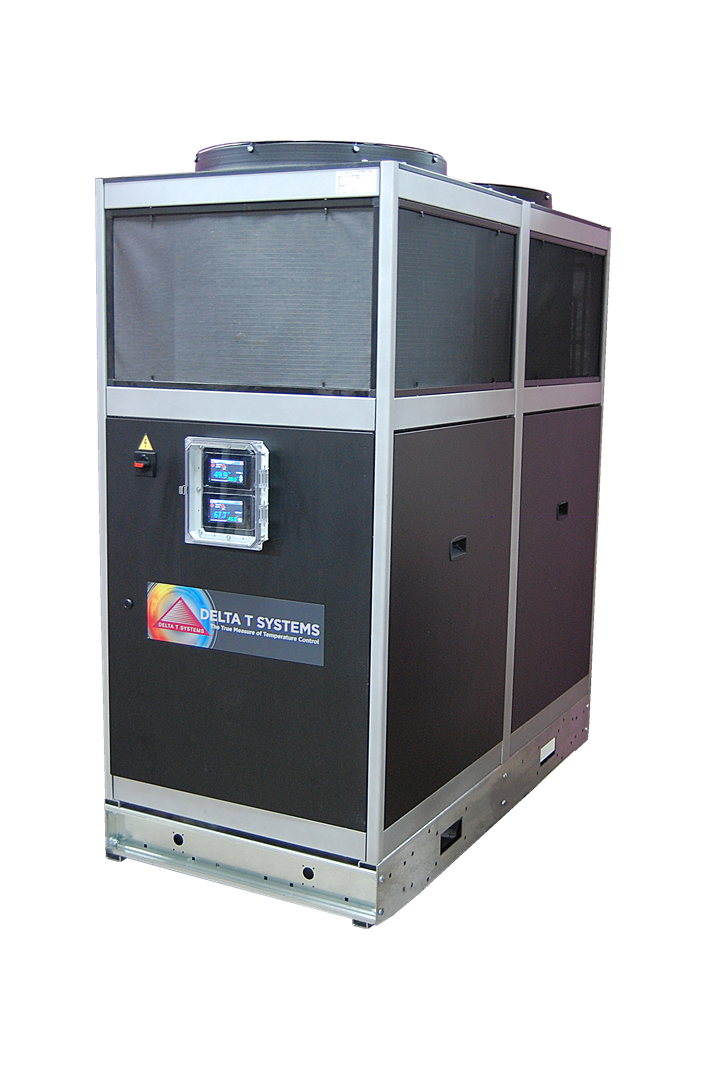
Delta T Systems now offers full redundancy as an option for its chillers.
Photo Credit: Delta T Systems
Related Content
-
ACS Group Adds Regional Sales Manager
Richard Gutierrez named Southwest regional sales manager.
-
Water Temperature Control Upgraded and Integrated into Machine Control
Engel’s new eco-flomo temperature control system continuously monitors injection mold cooling and temperature control circuits, displaying pressure, temperature and flow rate values.
-
Multicoupling Range Extended
Hasco‘s quick-connect system for multiple cooling circuits has added U.S., French and HT versions.