Fakuma 2023: Wittmann Battenfeld Expands All-Electric Line, Direct-Current Capabilities
Wittmann Battenfeld will introduce the new EcoPower B8X injection molding machine line and show direct current as an energy source for a concept machine that will power its own robot.
At Fakuma 2023 (Friedrichshafen, Germany; Oct. 17-21), Wittmann Battenfeld plans to bring minimum energy usage into maximum focus. In all, the company’s exhibit (Hall B1, booth 1204) will feature eight technology displays, including injection molding machines from the MacroPower, SmartPrimus (formerly SmartPower) and EcoPower lines of hybrid and all-electric presses. For the EcoPower all-electric line, the company will unveil the new EcoPower B8X line, which will be available in the European market in clamping forces from 550 to 1800 kN (approx. 60 to 200 tons) from Fakuma onwards. It will also expand its conceptual machine model — EcoPower DC — which draws its power supply solely from a battery as DC voltage source.
A Wittmann spokesperson told Plastics Technology the EcoPower B8X will be available in the U.S. market starting at the NPE show (May 6-10; Orlando), in a size range from 60 to 330 tons.
Wittmann Battenfeld points to several specific upgrades made to the EcoPower B8X line, which it says provide further energy reduction over its predecessors. The new injection unit, which can swing out, has replaced grease lubrication with oil lubrication, lowering resistance and adding to the press’s flexibility. That flexibility is aided further via a range of additional injection unit sizes. The company says the toggle-lever design has also been optimized to serve dynamic operations and greater service life, which in addition to faster injection units, has enabled short cycle times for the machines.
Regarding improvements to the toggle, the spokesperson said the design has been optimized so that 15% less force is required to lock the clamp unit, reducing energy consumption by 3% to 7%, depending on the press size. In addition, the diameter of the bolt has been increased to reduce the surface pressure and result in a longer service life, with bushing changed to a hardened bronze.
The B8X control system now utilizes several in-house-developed system components, which reportedly enable a higher internal clock frequency, resulting in shorter response times to sensor signals and thus a higher reproducibility of parts.
To showcase the newly improved line, Wittmann Battenfeld will display an EcoPower 110/350 B8X paired with a new sprue picker: model WX90, plus a WFC120 flow controller. The machine and auxiliaries are laid out as an “Insider Cell”, wherein production scrap is reintegrated directly into the molding process via a parts chute and an S-Max screenless granulator.
The cell will produce a climbing net bracket from an 8-cavity mold supplied by Austrian toolmaker Lechner. The sprue will be removed and transported directly into the granulator, which is integrated into the machine, via the WX90 sprue picker. Robot and granulator are incorporated in the molding machine’s B8X control.
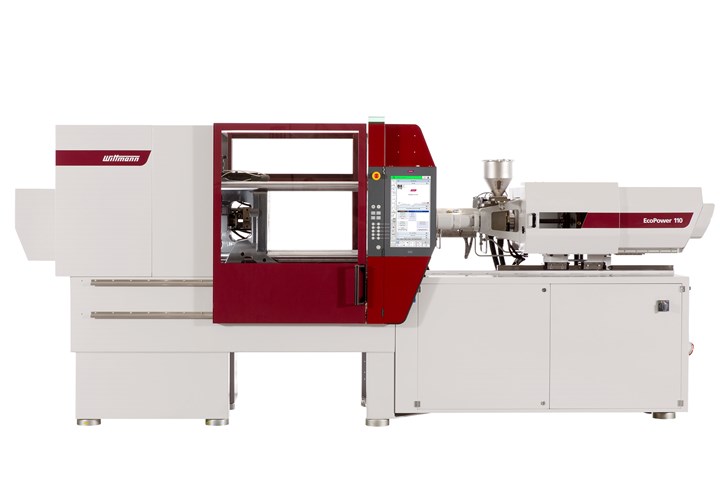
The new EcoPower B8X line will be available in the European market in clamping forces from 550 to 1800 kN (approx. 60 to 200 tons) from Fakuma 2023 onwards.
Photo Credit: Wittmann Battenfeld
Direct Power to the Process
Fakuma provides Wittmann Battenfeld the opportunity to display the latest in its EcoPower machine concept, which was introduced at K 2022 and seeks to directly utilize renewable energy without first having to pass the sustainably derived electricity through inverters, transformers and high-voltage power lines, which have their own carbon footprint and lead to power loss. At the fair, the company will take the concept further by having the 3-axis robot removing parts from the machine drawing its power directly from the interim DC voltage circuit of the EcoPower.
In addition to a smaller carbon footprint, Wittmann Battenfeld points out that the use of direct current to operate an injection molding machine can help keep energy costs low, and the direct current energy can also be stored in conventional batteries to protect against voltage spikes and to increase energy security.
At Fakuma, this technology will be demonstrated on an EcoPower 180/750+ B8X. Running a single-cavity mold from the Austrian company Kunststofftechnik Grabher GmbH, the cell will product a PP drainage body. The part will be removed by a modified WX142 robot in DC version from Wittmann, drawing power directly from the interim DC voltage circuit of the EcoPower. The technology will also return any surplus energy to the interim circuit whenever the axes are delayed. As part of the live presentation of the DC technology at the fair, the machine will not be plugged into the exhibition hall, rather it will be powered independently via a solar power storage battery consisting of salt battery technology supplied by Innovenergy. The battery has a total capacity of more than 45 kWh, which is more than sufficient for continuous machine operation throughout an entire 8-hour trade fair day.
Automated Assembly and LSR Molding
Other machine displays on hand will include a SmartPrimus 90/350, which is part of a digital cell producing a bubble level. Revisiting a machine display the company had at K 2022, with the SmartPrimus nomenclature replacing the previous SmartPower branding. Equipped with the CMS Lite conditioning monitoring system and an automation cell designed and manufactured by Wittmann Battenfeld in Germany, the machine will mold an ABS level from a 1+1-cavity mold supplied by Austrian firm SOLA. Top and bottom halves of the level housing are molded, with one laser printed and the other receiving the level vials, with visual inspection of all steps and followed by automated assembly of the halves. The bubbles’ positioning after assembly is also checked via a vision system.
An LSR molding demo will also revisit a K 2022 display, with a MicroPower 15/10H/10H Combimould producing a thermoplastics and LSR membrane for an upmarket micro loudspeaker from a single-cavity mold supplied by Austrian firm Starlim Spritzguss. Wittmann Battenfeld says the precision of the machine and mold allow a single-cavity tool, where normally multiple cavities are needed to satisfy the minimum throughput of the press and eliminate residence time issues. The MicroPower has 2-step screw-and-plunger thermoplastic and LSR aggregate injection units, with an LSR metering pump supplied by EMT Dosiertechnik, featuring a 1-liter cartridge system. Outside its own booth, Kracht will demonstrated LSR molding on an EcoPower 110/350 B8X. Equipped with an LSR metering pump from Kracht, the machine will use an 8-cavity mold supplied by Germany’s EMDE MouldTec to produce pacifiers.
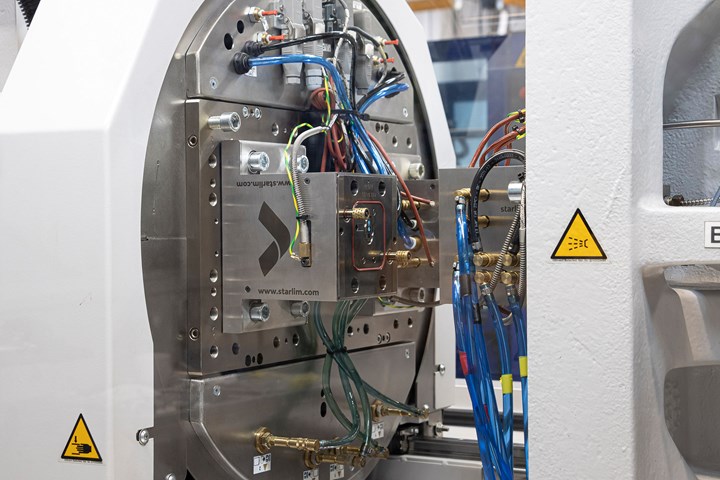
Utilizing a single-cavity mold supplied by Austrian firm Starlim Spritzguss, Wittmann will mold an LSR speaker membrane on its MicroPower micromolding machine at Fakuma 2023.
Photo Credit: Wittmann Battenfeld
Wittmann Battenfeld will also present Airmould internal gas pressure technology, including the Airmould 4.0 pressure control module and the manual operating unit, and the just as at K, IMAGOxt software will carry out energy measurement on every machine in the company’s booth. The program calculates CO2 consumption and energy savings, with calculations documented in reports online or the ability to use an optional extension to the TEMI+ MES program from Wittmann.
Related Content
Completely Connected Molding
NPE2024: Medical, inmold labeling, core-back molding and Industry 4.0 technologies on display at Shibaura’s booth.
Read MoreInternal Gas Pressure Molding Offers Sustainability Benefits
Wittmann Battenfeld says its upgraded Airmould 4.0 technology, which features a more compact footprint, saves material and cycle time — thereby also cutting energy use.
Read MoreRead Next
Industry 4.0: Wittmann Battenfeld Makes OPC UA Compatibility Standard
Citing the impact of the coronavirus on the need to digitize manufacturing, Wittmann Battenfeld announced that effective April 1, newly ordered peripheral equipment complies with OPC UA communication protocols free of charge.
Read MoreMES Platform Adds Energy Monitoring Module
Wittmann Battenfeld’s TEMI+ manufacturing execution system (MES) software has added the IMAGOxt software module to track energy consumption and more on a plant floor.
Read MoreAnswering the Sustainability Challenge with Digitalization
Attendees in the molding halls of K can count on exhibits that address two main themes: digitalization and sustainability. Digitalization in the form of smarter pieces of equipment communicating with each other and with plant personnel; and sustainability in the form of greater energy efficiency and the ability to process recycled and renewable resins.
Read More