Flow Controller Series Updated
A new control valve for more precise management of the flow rate is one update to the flow controller line Wittmann Battenfeld started its business with more than 40 years and 500,000 units ago.
Wittmann Battenfeld (U.S. office Torrington, Conn.) has updated it Series 110 and 310 flow controllers, keeping proven features borne out over 40-plus decades in the field and adding new ones. Used for distributing cooling water into molds and specific areas inside injection molding machines, such as the feed zone, or for the oil-cooling system in hydraulic machines, the 101 and 301 flow controllers will retain the proven pipe cleaning method, which can be done without removing the pipe through the top part of the housing. Wittmann notes that replacing the O-ring by lifting the pipe out of the bracket and then pulling it through the housing is still possible.
New to the product is a highly precise control valve for accurate manipulation of the flow rate. The valve disk is double sealed towards the spindle, and its axial movement vs. radial movement marks a shift from previous designs.
Wittmann says these innovation reduce wear for the O-rings, extending their service life. Made from EPDM, the O-rings also provide high levels of chemical and heat resistance. As in previous models, the thermometer’s sensor tube is situated directly in the return water, giving instantaneous readouts of temperature fluctuations. To keep the pressure drop inside the flow controller to a minimum, the cross-sections have been made as large as possible.
Options Available
Additional valves are also offered for the new 110 and 310 series, including the central shut-off or Z-valve for central blocking of the water supply to several circuits in the event of interruptions in the injection molding cycle. Single shut-off valves or E-valves are available as well, which are used to interrupt the cooling process in individual mold circuits by cutting off the cooling water flow. E-valves are normally used in combination with temperature sensors monitored by the machine’s control. This allows temperature control of individual mold cooling circuits via cooling pulses. The optional blow-out valve has an additional compressed air connection and in conjunction with the Z-valve allows emptying of the mold circuits.
The Series 110 works with open and closed cooling circuits. Flow volume is indicated in accordance with the float measuring principle: a cone is lifted by the water flowing in the return of the mold circuit. Flow range per circuit ist he standard 0 to 10 l/min. Mold connections with a 12-mm brass socket for 3/8-in. hoses are standard, with a threaded connection with a G 3/8-in. brass threaded sleeve available on request. There are also options for threaded 14-mm brass socket for ½-in. hose, or a threaded 20-mm brass socket for ¾-in. hose.
The Series 310 flow regulators for large injection and blow molding machines features a low pressure drop to run the highest flow volumes. The special design of the regulating valves reportedly results in accurate reproduction of cooling water volume and temperature in the different mold circuits and can also be achieved for low flow volumes.
Standard flow rates range from 0–30 l/min, with G 3/8-in. brass threaded sleeve mold connections. A threaded 14-mm brass socket for ½-in. hose, or a threaded 20-mm brass socket for 3/4-in. hose is optional.
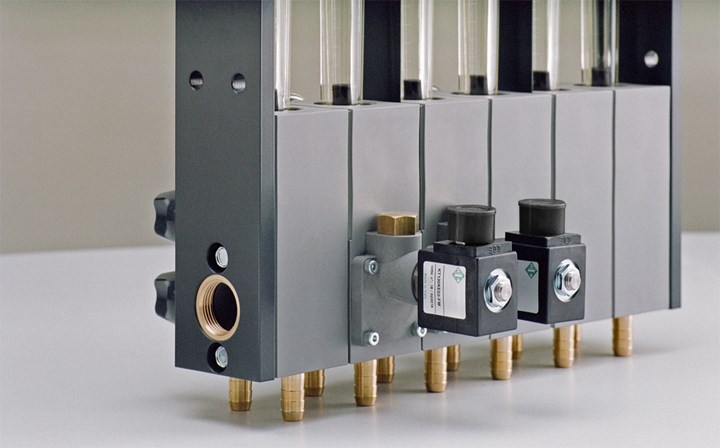
Wittmann Battenfeld’s flow controllers feature an updated control valve with a double-sealed valve disk.
Related Content
Captive Molder Beefs Up Auxiliaries to Boost Quality, Consistency
SeeScan adds conveying, drying, feeding and chilling technologies to improve quality — and enhance employee safety — in production of its underground/underwater inspection systems.
Read MoreMulticoupling Range Extended
Hasco‘s quick-connect system for multiple cooling circuits has added U.S., French and HT versions.
Read MoreACS Group Adds Regional Sales Manager
Richard Gutierrez named Southwest regional sales manager.
Read MoreTemperature Control: What You Need to Know to Comply With New Cooling-Fluid Regs
Beginning the first of this year, 12 states are following EPA bans on potentially damaging cooling fluids. Chiller suppliers have adjusted equipment designs to accommodate the new regulations. Here’s what all this means to processors.
Read MoreRead Next
Heating/Cooling: Pressurized Temperature Controller With Cell Connectivity
Wittmann Battenfeld is expanding its Tempro line of temperature controllers at K with a pressurized unit capable of reaching a maximum temperature of 100C.
Read MoreWittmann’s 40th Anniversary Gala Unveils New Products
New machinery, robots, and auxiliaries demonstrate continued momentum of technical development—and preview some K 2016 exhibits.
Read MoreWittmann Battenfeld Hosts Live Show
Open house to celebrate the expanded U.S. headquarters showcases innovations.
Read More