Multicomponent Mold Combines Capping and Unscrewing Functions for Pharma Closure
Braunform says its patented RotaricE² mold, which will mold Luer lock pharmaceutical closures in Arburg’s K 2022 booth, allows the use of one tool and one machine, versus two, while eliminating post-mold assembly.
Braunform will present its patented RotaricE² mold technology at K 2022, running a Luer connector in Arburg’s booth, integrating multiple materials, servodriven mold actions and assembly steps into a single 4+4 cavity mold. Running on an Arburg Allrounder More and featuring a Ewikon hot runner for the second shot, the Braunform mold will produce the 11-mm (0.43-in) long Luer locks with a diameter of 10 mm (0.39 in) in an overmolding tool, which also has capping and unscrewing functions in a side-gated design. The second shot in TPE weighs just 0.05g, requiring precision design in the Ewikon hot runner system.
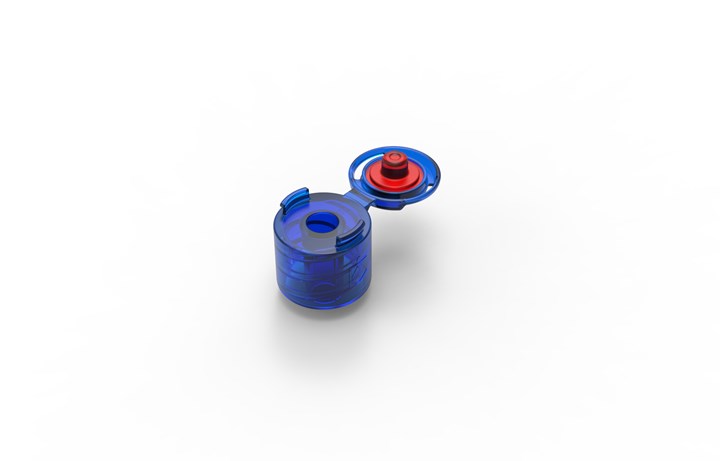
The Luer lock pharmaceutical closure is 11-mm long and 10-mm in diameter.
Photo Credit: Braunform
Braunform says this compact, multitasking setup allows a high number of cavities in a small-footprint mold. In fact, the company says 4+4-cavity mold running at K could be expanded out in modular design of up to 64+64 cavities.
To achieve capping in a multi-component application in a single step with limited space, Braunform redirected a rotary movement into a translational movement within the mold. Braunform says the integrated servoelectric rotary drives move in the mold quickly, gently and with wear detection. Braunform says this design enables compact, radial arrangement of mold cavities with slides or masking devices around a sprue or a sidegate.
In total, Braunform says RotaricE² mold integrates six functions into the ejector side—core-back, two sliders per cavity, raising the lid by means of a lifter, translational capping of the closures, unscrewing and final ejection. Braunform notes that the second component is formed via the core-back system, which means the part doesn’t need to be repositioned. Sliders, which are actuated by pull/push parts when the mold is opened, demold the snap-on hooks for the lid. A lifter then raises the lid so that the closure can then be capped while still in the mold using the patented in-mold capping system. As final step the Luer thread is molded and demolded by a thin unscrewing sleeve. The final demolding of the assembled product is performed by a thin pipe ejector with a wall thickness of 0.60 mm (0.02 in). The four main movements—core-back, lifter, in-mold capping and unscrewing—are controlled by AMK servo motors, with ejection powered by the machine ejector.
Two Kistler indirect pressure sensors per mold cavity can detect and sort defective parts by communicating with the automation. Ewikon equipped the hot side of its hot runner with a Smart Control system for real-time data analysis and evaluation, while Meusburger supplied key mold components. Utilizing the Braunform MED Mold concept, the features coatings from Oerlikon Balzers and rolling element centering systems from Agathon, as well as diffusion-welded inserts from IQtemp to ensure close-contour cooling of the die inserts on the nozzle side.
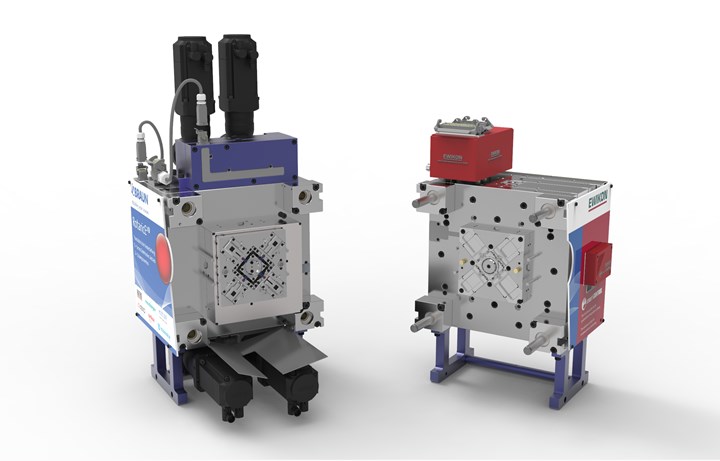
Braunform has integrated six distinct functions into the ejector side of the tool, giving it higher functionality in a more compact footprint.
Photo Credit: Braunform
Related Content
-
Exhibitor Registration Opens for K 2025
Exhibitor registration for the triennial event, which will take place Oct. 8-15, 2025, in Düsseldorf, Germany, is open with a reservation deadline of May 31, 2024.
-
Breaking the Barrier: An Emerging Force in 9-Layer Film Packaging
Hamilton Plastics taps into its 30-plus years of know-how in high-barrier films by bringing novel, custom-engineered, nine-layer structures resulting from the investment in two new lines.
-
Energy Efficiency in Focus at K 2022
As much as cycle time, kWh/kg was an oft-cited metric by injection molding machine suppliers at October’s big show.