SPE Automotive Awards Give Nod to 'Firsts' & Pandemic Solutions
The 50th annual automotive innovations awards recognized several “firsts” and an added category of innovative solutions for COVID-19 protection.
After having had to skip a year due to the coronavirus pandemic, the 50th annual Society of Plastics Engineers Automotive Division’s Blue Ribbon Automotive Innovation Awards did not disappoint. There were several “firsts” among the seven major categories, along with an added category featuring innovative solutions for COVID-19. Since 1970, this oldest and largest competition of its kind as highlighted the positive changes that polymers have brought to automotive and ground transportation industries, such as weight and cost reduction, parts consolidation, increased safety, and enhanced aesthetics and design freedom.
To commemorate “50 Years of Plastics Innovation,” instead of picking a single Hall of Fame (HOF) Winner for 2021, the HOF committee selected the top five leading innovations from the previous 37 winners—from 1983 to 2019. The criteria for a HOF award is that the nomination be in use for at least 15 years and be game changing; very successful worldwide; innovative in materials, process and application; and still being used. The top five Hall of Fame Awards are:
• HDPE fuel tank, awarded to Volkswagon AG in 2000.
• Front & rear TPO bumper fascias, awarded to General Motors Co. in 2010.
• PVB (polyvinyl butyral) windshield interlayer, awarded to Ford Motor Co. in 1988.
• Nylon intake manifold, awarded to Porsche AG in 2005.
• PC headlamp assembly, awarded to Ford Motor Co. in 2007.
Meanwhile, the 2021 Vehicle Engineering Team Award (VETA) award went to the team at Ford Motor Co. and its suppliers that developed the 2021 model year Ford F-150 pickup. Created by SPE in 2004, the VETA award recognizes the technical achievements of entire teams—automotive designers, engineers, tier integrators, materials suppliers, toolmakers, and others—whose work in research, design, engineering, and/or manufacturing has led to significant integration of polymeric materials on notable vehicles. For 44 years, Ford’s F-Series has been the best-selling pickup in the U.S., and the 2021 model features numerous plastics and composites innovations, many of which were nominated in other categories of this year’s competition, including Body Exterior, Body Interior, Chassis/Hardware and Materials
Now here’s a look at the eight 2021 winners.
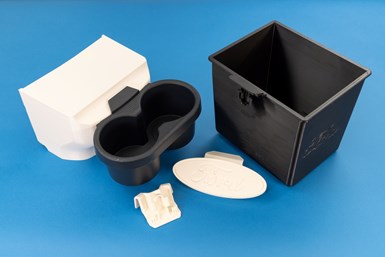
Additive manufacturing was used in an industry-first integrated tether system for use across the entire Ford Maverick series.
Additive Manufacturing: Integrated Tether System
Additive manufacturing was used to produce an industry- first integrated tether system whereby customers can select, download NFTL files, and 3D print their own swappable accessories (e.g. cupholders, trash bins, phone cord organizers, umbrella holders, etc.) that fit in storage slots of their vehicle across the entire Ford Maverick series. More than 20 initial designs were developed by Ford and its supply teams, such as tier supplier IAC Group, but many future designs could be suggested by customers. A variety of printer types and suggested materials can be used. This provides customers with flexible, customizable storage and use features or the option to maximize cabin space while avoiding significant tooling investment.
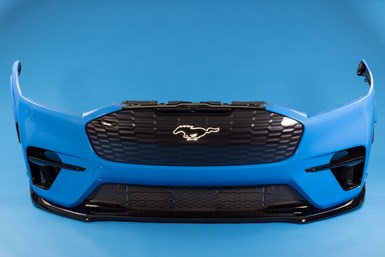
Hardcoated and painted front PC grille with lit emblem for the 2021 Ford Mustang Mach E GT.
Body Exterior: Grille with Integrated Lit Emblem
This hardcoated and painted front PC grille with lit emblem provides a 3D futuristic effect in a single part and is featured on the 2021 Ford Mustang Mach E GT. The tier supplier/processor is Magna Exterior and its LexaMar Div. Covestro is the material supplier and Inevo Group the tool maker. Injection/compression molding forms the large-format clear PC grille with variable wall thicknesses (3 to 5 mm) in a lower-tonnage press that helped minimize or eliminate flow lines and stress marks. After molding, the optical-quality part undergoes a hardcoat silicone dip to provide weathering and abrasion resistance; the pony emblem is milled out; and primer and paint are selectively applied to the B side of the part—the first use of paint-over-hardcoat for an auto exterior-trim application.
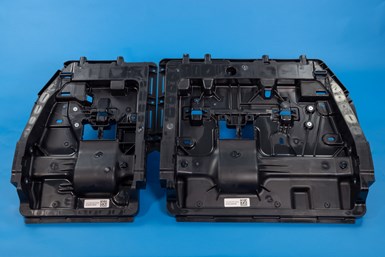
This single shoot & ship plastic part replaces a 16-piece steel assembly for the third-row seatback in the 2021 Toyota Sienna.
Body Interior: Third-Row Seatback
Another industry first is the replacement of a 16-piece steel assembly with a single, shoot & ship plastic part for this third-row seatback in the 2021 Sienna Toyota. Tier supplier/processor are Toyota Boshoku Corp and Flex-N-Gate Corp. BASF is the material supplier and Concours Technologies is the toolmaker. Using BASF’s new Ultramid B3ZG7 CR, a 35% short-glass, impact-modified nylon 6 injection grade, saved 30% in weight and 15% in cost. Moreover, this all-plastic, freestanding seatback offers excellent energy absorption without need for metal support brackets and is said to represent a two-fold improvement in crash performance and takes 63% less effort for occupants to raise the seat to its upright position, eliminating the need for a seat motor.
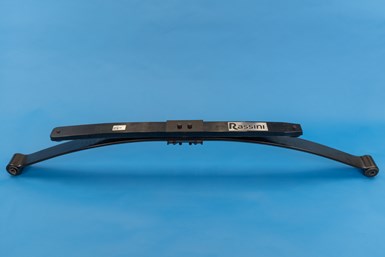
The winner of the Chassis/Hardware category and the Grand Award winner is the thermoset multi-material rear leaf spring on the 2021 Ford F150.
Chassis/Hardware/Grand Award Winner: Multi-Material Rear Leaf Spring
This new hybrid rear leaf spring featured on the 2021 Ford F150 combines a high-strength steel main pack plus an HP-RTM fiberglass-reinforced epoxy helper that reduces mass 30% while providing the same stiffness and durability as a conventional steel leaf spring. Tier supplier/processor are Rassini Suspensiones and SGL Carbon, and the materials suppliers are Hexion and SGL Carbon. Additional benefits cited include increased payload capability, lower part count, decreased interleaf friction, smoother engagement, lower noise, and lower carbon footprint.
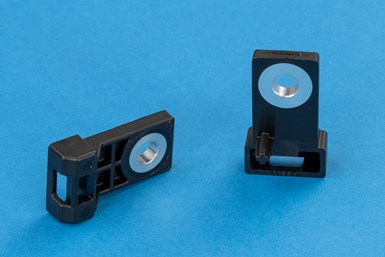
These nylon 6 wire-harness clips on the 2021 Ford Bronco Sport are injection molded from 100% PCR ocean plastics.
Environmental: Wiring-Harness Clip
These injection molded recycled nylon 6 wire-harness clips featured on the 2021 Ford Bronco Sport are injection molded from 100% PCR ocean plastics. “Ghost gear” (discarded fishing nets) are collected by fishermen in the Indian Ocean and Arabian Sea, providing jobs and healthier marine life. Tier supplier/processor are Lear and HellermannTyton North America. Material supplier/toolmaker are DSM and HellermannTyton North America
DSM’s Akulon RePurposed nylon 6 is melt compounded and is said to provide performance comparable to virgin prime resin at 10% cost savings, lower energy use, improved supply-chain stability, and LCA benefits. No tooling changes and minimal process changes were needed for this drop-in substitution.
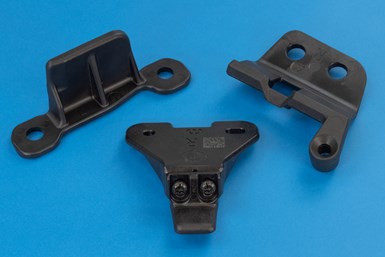
A 30% ultrasoft carbon fiber-reinforced PPA replaced investment cast steel in six brackets for removable hardtop and soft top roofs as featured on the 2021 Stellantis Jeep Wrangler and Jeep Gladiator.
Materials: Composite Roof Receivers
Six brackets for removeable hardtop and softtop roofs were converted from cast steel to 30% ultrashort carbon-fiber (USCF) reinforced PPA for the 2021 Stellantis Jeep Wrangler and Jeep Gladiator. These injection molded roof receivers provide comparable part strength while reducing costs 38% and weight 79%.
The tier supplier is Stellantis and the material supplier/toolmaker are Mitsubishi Chemical Advanced Materials and Maple Mold Technology. Mitsubishi’s KyronMAX S-4340 PPA with 30% USCF allowed the elimination of powder coating, providing improved scratch and mar resistance and a weatherable Class A finish that allowed for mid-program replacement and backward service compatibility. The USCF composite is said to mold like neat polymers but outperforms long-fiber (LFT) materials, is fully recyclable, and has a lower carbon footprint than metal/alloy parts. Direct-drop valve gates and T-nut fasteners also were key enablers.
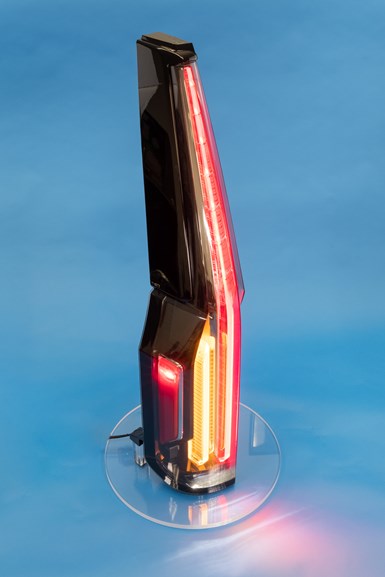
Program timing was reduced by three months and $250,000 in prototype tooling was avoided through virtual prototyping for this thick lightbar development featured on the 2021 GM Cadillac Escalade.
Process Assembly/Enabling Technologies: Thick Lightbar Development
This challenging 780 mm long × 18 mm thick, transparent-red light blade for rear taillamps, featured on the 2021 GM Cadillac Escalade, offers a unique appearance and homogeneous lit appearance.
Tier supplier/processor is Valeo Lighting Systems and material supplier/toolmaker are Covestro and Windsor Mold Group.
Key to making the patented application work were advanced simulation tools for design and functional optimization and warpage control; complex runner, parting line, shutoff valves, and multi-shot injection process control. Also key is a custom-formulated optical-grade of Covestro’s Makrolon LED PC that helped manage quality, cost, and molding capacity and met all legal rear-lighting requirements. Despite technical challenges, program timing was reduced by three months and $250,000 in prototype tooling was avoided through virtual prototyping.
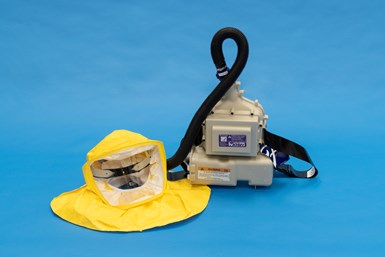
Ford Motor’s first all-plastic PARP converted metal components to plastic to reduce mass and costs and improve user comfort for this PPE used by medical workers treating COVID-19 patients.
(All Photos: SPE Automotive Div.)
Industry Solutions for COVID-19: Powered Air-Purifying Respirator
Ford Motor’s 2020 NIOSH-certified, Limited Use APR (Powered Air-Purifying Respirator), the first all-plastic product of its type, converted previously metal components to plastic to reduce weight and cost and improve user comfort. This personal protective equipment is used by medical workers caring for COVID-19 patients.
Tier and processor contributors were Ford and Denso Corp. Material suppliers were Asahi Kasei America and Celanese, and toolmakers were 3Dimensional Services and Protolabs. Asahi Kasei’s TD40 40% talc-reinforced PP was used for the injection molded breathing-tube adapter, filter cover, electronic cover and blower housing. The battery cover was transitioned from PP-TD40 to Celanese’s Hostaform/Celcon POM (polyacetal).
The lighter, more efficient design improved battery life, enabling workers to complete a 12-hr shift without needing to recharge the battery. Production was increased to 8500 units/week from the 650/week achieved by the previous supplier. All profits from sales were donated to COVID-19 relief funds. Four patents are pending on the unit.
Related Content
Additive Fusion Technology Optimizes Composite Structures for Demanding Applications
9T Labs continues to enhance the efficiency of its technology, which produces composite parts with intentionally oriented fibers.
Read MoreMolder Repairs Platen Holes with Threaded Inserts
Automotive molder ITW Deltar Fasteners found new life for the battered bolt holes on its machine platens with a solution that’s designed to last.
Read MoreNeste, Borealis and Covestro Plan to Make Polycarbonate From Recycled Tires
Companies announced agreement that will use advanced recycling to convert old tires into new PC-suitable for automotive applications.
Read MoreInjection Molded Tape and Resin “Sandwich” Technology Debuts
During its Mobility Days in Austria, Engel and KTM Technologies debuted an all-plastic molded motorcycle seat base produced via a tape-sandwich process that can run in a standard molding process.
Read MoreRead Next
Beyond Prototypes: 8 Ways the Plastics Industry Is Using 3D Printing
Plastics processors are finding applications for 3D printing around the plant and across the supply chain. Here are 8 examples to look for at NPE2024.
Read MoreLead the Conversation, Change the Conversation
Coverage of single-use plastics can be both misleading and demoralizing. Here are 10 tips for changing the perception of the plastics industry at your company and in your community.
Read MoreSee Recyclers Close the Loop on Trade Show Production Scrap at NPE2024
A collaboration between show organizer PLASTICS, recycler CPR and size reduction experts WEIMA and Conair recovered and recycled all production scrap at NPE2024.
Read More