Thermoplastics Composites Featured in SABIC’s ICEhouse
Innovative structure at 2017 World Economic Forum combined advanced technologies and design.
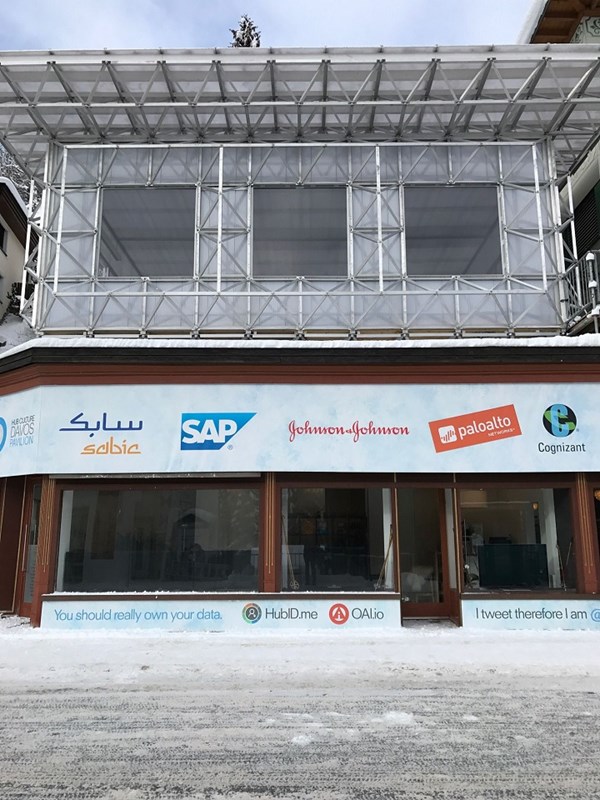
Innovative structure at 2017 World Economic Forum combined advanced technologies and design.
Featured at the 2017 World Economic Forum held last week in Davos, Switzerland, was the SABIC ICEhouse (ICE stands for Innovation for the Circular Economy), which combined advanced thermoplastic composite technologies and design.
This iconic structure spearheaded SABIC’s efforts to highlight breakthrough technology to the world—including Lexan PC sheet and systems for the walls, ceiling, roofing and windows—and, in doing so, to promote renowned architect William McDonough’s concept of the importance of closed-loop, durable carbon systems.
McDonough—an author, sustainability pioneer and his company, William McDonough + Partners and WonderFrame LLC—designed and built ICEhouse with collaboration and support from SABIC. The Circular Economy incorporates the Cradle to Cradle design philosophy developed by McDonough, which incorporates the principles of material health, material reutilization, renewable energy, clean water and social fairness.
The Circular Economy utilizes this approach to product design to essentially disrupt the typical take-make-dispose flow of material resources, replacing it with designs that make use of carbon through products that are inherently recoverable, reusable and recyclable.
Said McDonough, “Carbon—the element—is not the enemy. Climate change is the result of breakdowns in the carbon cycle: it is a design failure. When carbon is used in the right way, like in the materials made by SABIC, buildings such as ICEhouse are breathing new life into the carbon conversation. Rather than focus on carbon emissions, we can work with carbon as durable element, as an earthbound asset.”
The 2017 ICEhouse features new fiber-reinforced thermoplastic composite technologies in the floor panels and profile structures instead of metal and wood, reportedly delivering superior durability, impact performance, and safety with less weight. The cladding is Lexan multi-wall PC sheet filled with nanogel for what is said to be outstanding energy efficiency.
Meanwhile, thermoplastic composite sandwich floor panels with skins made out of Udmax GPP 45-70 (continuous fiber-reinforced polypropylene) tape replace plywood and are reportedly 50% lighter, with higher abrasion and impact resistance. Also novel, are the tubular composite structures, also made with Udmax GPP 45-70, which partially replace aluminum L-shaped profiles with very favorable weight-to-performance ratio.
Ernesto Occhiello, executive v.p. for SABIC Specialities, notes that these material innovations are not limited to ICEhouse. For example, the Udmax PP tape can be used for aircraft or train panels.
Related Content
-
Automotive Awards Highlight ‘Firsts,’ Emerging Technologies
Annual SPE event recognizes sustainability as a major theme.
-
What's the Allowable Moisture Content in Nylons? It Depends: Part 2
Operating within guidelines from material suppliers can produce levels of polymer degradation. Get around it with better control over either the temperature of the melt or the barrel residence time.
-
Tracing the History of Polymeric Materials, Part 26: High-Performance Thermoplastics
The majority of the polymers that today we rely on for outstanding performance — such as polysulfone, polyethersulfone, polyphenylsulfone and PPS — were introduced in the period between 1965 and 1985. Here’s how they entered your toolbox of engineering of materials.