Eigen Integrates Ampacet Color Monitoring into Machine Vision Solutions for Plastics
Injection molders, blow molders and extruders looking to avoid downtime and reduce scrap related to defect detection and color monitoring get a single solution for inline quality monitoring and management.
Eigen Innovations has partnered with Ampacet LIAD to integrate the latter’s Spectro 4.0 color monitoring and management solution into its machine vision solutions. Color metrics captured by the sensor are correlated with digital part records generated by Eigen’s integrated machine vision solutions.
“Our machine vision solutions are designed to capture and correlate all the data manufacturing teams require to assess the quality and start avoiding defects,” says Josh Pickard, director of innovation at Eigen. “This collaboration with Ampacet LIAD is exciting because it brings color metrics into our digital records, meaning inline color monitoring and the ability to color correct on the fly through our software.”
Adds Douglas Brownfield, commercial director of LIAD Smart at Ampacet, “We created Spectro4.0 to allow plastic processors to accurately measure color during production in real-time to reduce scrap and lost production due to poor color quality. When we saw what Eigen was doing — generating digital records with correlated quality and process data and what those records enable in terms of analytics, insights and ultimately, defect prevention — it was a no-brainer to bring our solutions together.”
Comprehensive Quality Monitoring & Management
Eigen’s machine vision solutions feature camera sensors, Edge processors and machine and network connectivity to capture and generate digital records with critical quality and process data on every part produced. Captured Image and process data is processed at the Edge enabling operators to review records flagged by machine learning models trained and managed within the solution software. The solutions operate on an open software platform meaning critical data from other sensors and sources can be integrated and correlated to each product record.
Ampacet’s Spectro 4.0 Smart Technologies is a patented color measurement system that offers in-line color measuring and correction capabilities. It ensures that parts in production meet the set color specifications. Fiber-optic sensors compare color data to the preset color standard throughout the manufacturing process to deliver consistent and accurate color monitoring —all without interrupting production or creating delays by collecting samples to test.
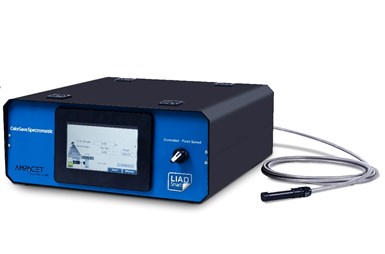
Combined, Spectro 4.0 and Eigen’s machine vision solutions are said to greatly reduce downtime, the consumption of expensive masterbatch, product rejects and the cost of scrap. Real-time quality monitoring and color measurements enable Production and Quality teams to make process adjustments and color corrections during production and provide historical data to improve future productivity.
“Having all that correlated data in standardized records is a game-changer for production and quality teams.”
“It comes down to removing subjectivity from the quality inspection process,” says Brownfield. “Spectro 4.0 removes it by delivering consistent color quality by way of L*a*b* value measurements and acceptable delta E threshold levels.”
Standardized Digital Product Records
The standardized digital part records containing quality (defect), process and color are accessible from anywhere through Eigen’s cloud platform. Teams within and across factories can collaborate, analyze and share learnings. Learnings can be shared among machines — so when a new defect or issue is detected, the model can be updated and redeployed across machines— ensuring it doesn’t go undetected on other lines or in other factories.
“Having all that correlated data in standardized records is a game-changer for production and quality teams,” says Pickard. “It gives them instant visibility to quality assessments. It means no more reliance on sample testing. And most importantly, it gives them the ability to use the data to enable automation and control variation that often causes quality issues. It makes enabling automation and defect prevention a reality.”
Automation & Defect Prevention
With standardized records and integrated solutions, production teams can train one model and deploy it across machines. It makes machine learning scalable, allowing operations teams to automate inspection and process monitoring and giving them the ability to automate a response when an issue is flagged with a product in production.
Eigen machines vision solutions are interlocked with machines and PLCs, meaning when issues are detected, a part is removed or the process is stopped while operators investigate. The integrated Eigen/Ampacet solution can automate a signal to the masterbatch feeder to adjust dosing automatically, in real time, ensuring color consistency.
Designed for injection molding, blow molding and extrusion, Spectro 4.0 is a highly accurate QA solution that allows manufacturers to maintain uniform color standards both in-house and with contract processors around the world. Spectro 4.0 also incorporates optional cloud services so each line’s color performance can be verified wherever cellular service is available.
Related Content
Software Tracks Energy Waste in Real Time
Affordable add-on to production monitoring software alerts uses when energy is being wasted.
Read MoreIndustry 4.0 Without Fear: Modular MES Software Lets You ‘Start Simple’ and Add on Later
‘Don’t be afraid of MES.’ App-based platform can start with monitoring just downtime and cycle time on a few machines and add machines and functionality later.
Read MoreManufacturers’ Superpower: ‘X-Ray Vision’ into Your Processes
Meet a ‘new’ name (to North American processors) in MES software, which provides a simple, modular way to achieve visibility into your production operations.
Read MoreUse Cavity Pressure Measurement to Simplify GMP-Compliant Medical Molding
Cavity-pressure monitoring describes precisely what’s taking place inside the mold, providing a transparent view of the conditions under which a part is created and ensuring conformance with GMP and ISO 13485 in medical injection molding.
Read MoreRead Next
For PLASTICS' CEO Seaholm, NPE to Shine Light on Sustainability Successes
With advocacy, communication and sustainability as three main pillars, Seaholm leads a trade association to NPE that ‘is more active today than we have ever been.’
Read MoreSee Recyclers Close the Loop on Trade Show Production Scrap at NPE2024
A collaboration between show organizer PLASTICS, recycler CPR and size reduction experts WEIMA and Conair recovered and recycled all production scrap at NPE2024.
Read More