Finnish Tech Center to Commercialize Chemical Recycling Process for Polyolefins
Process developed by VTT reduces waste polyolefins back to olefins will be basis for new company.
The VTT Technical Research Center, owned by the Finnish state, has announced it will spin off Olefy Technologies as a separate company. The move will allow the commercialization of a process for recycling waste developed as part of VTT Launchpad, VTT’s science technology incubator.
The recycling technology uses steam to rapidly heat waste plastics, breaking them down into virgin-grade olefin. The process works at a lower temperature than conventional naphtha cracking, and so it saves energy in addition to its potential to displace virgin production from oil. CO2 emissions are reduced by approximately 60%, VTT estimates. It works best with better quality feeds such as industrial waste, but can tolerate both organic and inorganic impurities and be used for any polyolefin-rich waste stream.
Materials like PET are not well suited for the process, because oxygen will react with the gaseous products. Given that existing systems for recycling PET are relatively robust, the Olefy process may fit in as a complement for recycling waste streams from which PET has already been removed.
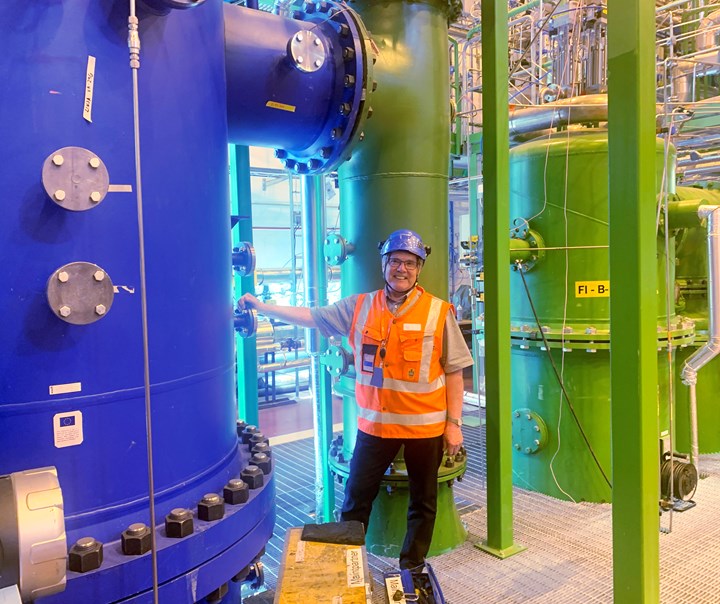
Matti Nieminen at VTT’s pilot center in Espoo, Finland.
Photo Credit: VTT Technical Research Center of Finland
Matti Nieminen, principal scientist at VTT, is technology director at the new company. “We have already tested our process with reject material from a mechanical recycling plant. This is very low quality material that would end up in an incinerator. Our Olefy process was able to recover more than 23% of the olefins, and in addition we recovered aromatic chemicals like benzene, xylene, and toluene,” said Nieminen. “Thus the overall yield of chemically recycled materials was more than 30% from this very low value waste.”
Olefy is currently exploring partnerships with technology providers to bring the process to market. The company anticipates its technology will be incorporated into existing steam cracking sites. Industrial demonstration is expected by 2026.
Related Content
-
‘Monomaterial’ Trend in Packaging and Beyond Will Only Thrive
In terms of sustainability measures, monomaterial structures are already making good headway and will evolve even further.
-
General Polymers Thermoplastics to Further Expand Distribution Business
NPE2024: Following the company’s recent partnership buyout, new North American geographic territories are in its sight.
-
Dow, Circusil Collaborating on Silicone Recycling Facility
Dow and Circusil announced plans to construct a silicone recycling facility in Kentucky.