Wittmann Battenfeld to Remain Operational During Covid-19 Crisis
Initially facing a forced shutdown, Wittmann Battenfeld—and many of the plastics manufacturers it supplies—were deemed essential and allowed to remain open.
On Friday, March 20, Connecticut Governor Ned Lamont issued the “Stay Safe, Stay Home” executive order, requiring all non-essential functions in the state to suspend in-person operations beginning at 8 p.m. on Monday, March 23. Understanding its important role in some very critical industries, injection molding machine, automation and auxiliary supplier Wittmann Battenfeld USA (Torrington, Ct.) leapt into action, Sonny Morneault, VP of U.S. sales told Plastics Technology.
“We activated our staff over last weekend and reached out to all our customers that we thought may be impacted by us not being able to service them,” Morneault said. The overwhelming response, according to Morneault, was, “Yes, we really need you.”
Many of these businesses were also deemed essential, and Connecticut quickly corrected the directive and established that manufacturing was indeed essential and could remain open with as much staff as possible working remotely. Morneault said Wittmann Battenfeld’s office in Illinois was under a similar order.
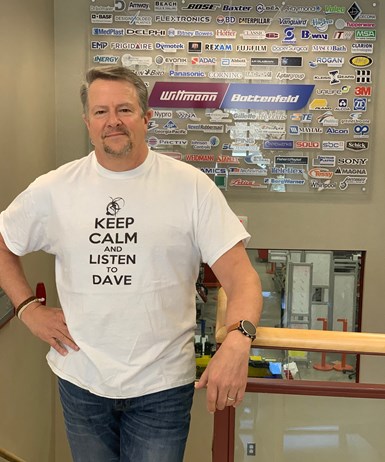
“Plastics are essential materials for manufacturing items that are essential to battling the COVID-19 crisis,” said David Preusse, president Wittmann Battenfeld. “The importance of plastics in a time like this cannot be understated, and we are proud to be a part of this industry.”
On March 25, Wittmann Battenfeld issued a press release noting that it would remain open for business during Covid-19 crisis. That initial over-the-weekend-outreach to customers had resulted in 45 ‘Essential Status’ letters “from customers who mold products that are critical to saving lives and battling this pandemic,” said David Preusse, president of Wittmann Battenfeld in North America.
“Yes, we really need you.”
The ‘Essential Status’ letters have come in from customers around the country, including industry leading names such as BD, Jabil Healthcare, Baxter Healthcare, Eli Lilly, 3M, Nemera, Flex, Cardinal Healthcare, Corning Life Sciences, Technimark and Comar. These customers are making essential plastic components including ventilator parts, Covid-19 diagnostics, pipette tips, drug delivery devices and many more emergency medical supplies.
At this time, about 50 employees in the state are working remotely, while at the company’s two facilities in Torrington, Preusse said there are about 30 staff on hand to work on essential jobs. Prior to the governor’s order, the company had tested its IT systems to ready them for more remote work.
The company has also addressed short-term customer service issues, creating a series of webinars for robot training that will temporarily take the place of in-person classes, for example. In addition, Wittmann Battenfeld has numerous apps and online support systems available for customers on a 24/7 basis.
The company is using regional staff as much as possible to minimize air travel, as well as deploying Team Viewer Meetings, web-based service and Face Time with our customers to help them keep running. Writing ‘All Employee Updates’ every 2 days, Preusse said he has strived to keep communications open with all employees. The company also put in place two weeks pay and paid time off to help staff get through what was originally an Executive Order for all companies to shut down in Connecticut, starting March 20, for 4-and-a-halfweeks.

Even after the state changed course on Sunday March 22 and moved to exempt all Connecticut manufacturing companies, Preusse said the company liked the idea of temporarily keeping a minimal workforce. “We believe this is the optimum measure to reduce the spread of this pandemic and the terrible overload in our hospitals, which leads to unnecessary deaths,” Preusse said.
Morneault noted that while the company has not yet experienced significant disruptions in its own supply chain, it expects that to change.
“We know [disruptions] are coming, but as of right now, we are still able to keep production running and goods/services/raw materials continue to trickle in,” Morneault said. “We know this will change in the coming weeks, so we are preparing for how to handle that. Fortunately, we still have a lot of inventory in house to support our customers.”
Related Content
Industrial Resin Recycling Diversifies by Looking Beyond Automotive
Recycler equips for new business in medical, housewares and carpeting.
Read MoreDuPont Buys Medical Product Manufacturer Spectrum Plastics
Purchase price of $1.75 billion for leading supplier of extruded, molded, and 3D printed medical components.
Read MoreCatheter Specialist Finds Sweet Spot Serving Small, Medium-Sized Concerns
Medical-component specialist LightningCath has carved a niche meeting the needs of small to medium-sized entrepreneurs with complex catheter designs … quickly.
Read MoreMedical Molder, Moldmaker Embraces Continuous Improvement
True to the adjective in its name, Dynamic Group has been characterized by constant change, activity and progress over its nearly five decades as a medical molder and moldmaker.
Read MoreRead Next
Coping with Coronavirus: What If You Can’t Get a Tech Service Visit?
‘Social distancing’ for service technicians? Online remote servicing to the rescue!
Read MoreWittmann’s 40th Anniversary Gala Unveils New Products
New machinery, robots, and auxiliaries demonstrate continued momentum of technical development—and preview some K 2016 exhibits.
Read MoreCoronavirus and the U.S. Plastics Industry Supply Chain
While we cannot confirm today that the coronavirus has already impacted the U.S. plastics industry supply chain, it is reasonable to expect that if the coronavirus crisis in China continues and escalates, it will negatively impact the U.S. plastics industry. For business continuity reasons, U.S. plastics companies need to look at their current supply chain involving China and—as a precautionary measure—examine alternative supply sources.
Read More