RFID Applied to Hot Runner Systems
Hasco says the adapted variant of the Mold Tag makes it possible to read out all data on the hot half or a wired system directly on a smartphone.
Hasco is bringing RFID technology to hot runner systems, using a Mold Tag for data management of hot halves to aid in maintenance, repairs and the ordering of spare parts. This technology makes it possible to read out all data on the hot half of a wired system directly on a smartphone.
Hasco notes that newly ordered hot halves and wired systems are now supplied directly with an integrated Hasco Mold Tag A5910/… Hasco says RFID technology (as opposed to bar codes or QR codes which can be copied) provides unambiguous identification with forgery-proof certification of origin.
The Mold Tag provides access to current information and CAD data of the hot runner system, as well as order reference, product category, product type, material number or maximum mold size to ensure correct installation. It is also kept up to date should any changes are made to the system.
The app contains a parts list and system specifications, with the ability to download assembly drawings as a PDF or 3D constructions of the entire system. Newly ordered hot halves are equipped with the tags as standard going forward. By clicking the NFC Scan button on the Hasco app and moving the NFC-capable end device close to the Mold Tag, all data about the hot runner system can be called up directly in the app.
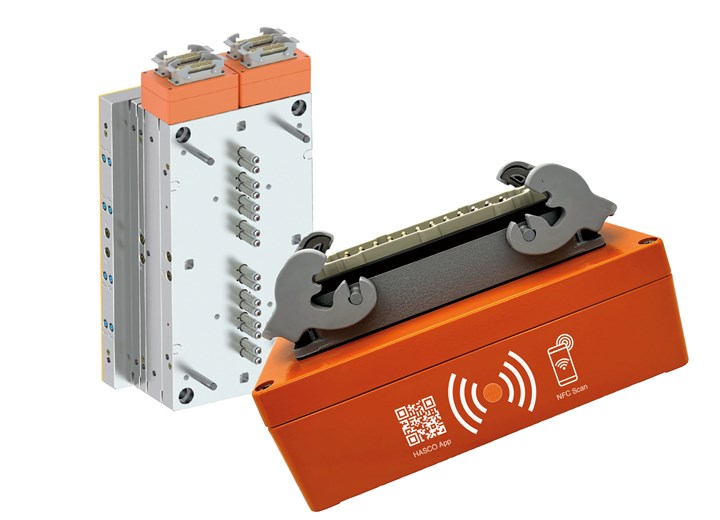
Hasco Mold Tag A5910/… brings RFID communication technology to hot runner hot halves. Photo Credit: Hasco
Related Content
-
Hot Runners: How to Maintain Heaters, Thermocouples, and Controls
I conclude this three-part examination of real-world problems and solutions involving hot runners by focusing on heaters, thermocouples, and controls. Part 3 of 3.
-
Three Key Decisions for an Optimal Ejection System
When determining the best ejection option for a tool, molders must consider the ejector’s surface area, location and style.
-
Design Your Tools for Moldability ... and Maintenance
In the initial design phase, when considering the structure and elements of the tool, are you designing them to be maintenance friendly? Canon Virginia has used this approach and preventive maintenance to make tool replacement a thing of the past. You can, too. Here’s how.