Sleek Extruder for Coating Applications
Smaller footprint, lighter weight allows machine to be readily integrated into existing carriages or platforms.
Davis-Standard has introduced a compact extruder engineered for extrusion coating applications. Called the CHP, the machine has a sleek design that provides a smaller footprint. It’s also said to be lighter in weight than comparably sized machines, allowing it to be more easily added to an existing carriage or platform structure. This provides processors with a space-saving replacement or coextrusion addition for increasing outputs and line speed.
The design addresses profitability factors such as reduced raw material loss, improved outputs, and greater application development, Davis-Standard says. It is built for exceptional performance with improved transition times and significantly higher processing rates than conventional extruders.
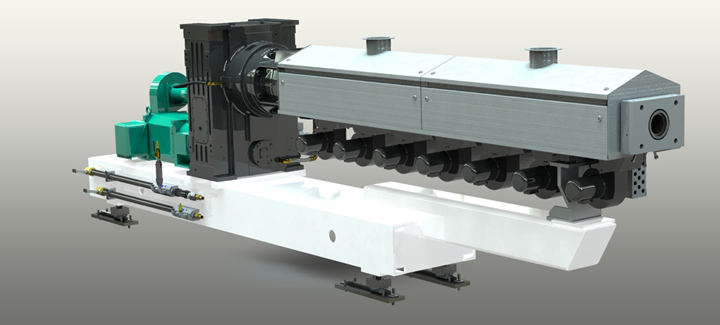
The CHP is available in sizes ranging from 2 in. to 4 in. (52 mm to 100 mm). Processors benefit from efficient mixing that delivers low pressure and melt temperature variability and output rates up to 80 to100% higher than current extruder options.
In addition, a reduced residence time of 3:1 with a faster purge between resins and colors supports quick changeovers minimizing raw material loss for bottom-line impact. Davis-Standard has a CHP extruder at its laboratory facility in Pawcatuck, Conn., for customers to run trials and validate processing opportunities prior to purchase.
Related Content
-
Use Interactive Production Scheduling to Improve Your Plant's Efficiencies
When evaluating ERP solutions, consider the power of interactive production scheduling to effectively plan and allocate primary and secondary equipment, materials and resources on the overall production capacity of the business and conclude that this is a key area that cannot be overlooked.
-
What to Know About Your Materials When Choosing a Feeder
Feeder performance is crucial to operating extrusion and compounding lines. And consistent, reliable feeding depends in large part on selecting a feeder compatible with the materials and additives you intend to process. Follow these tips to analyze your feeder requirements.
-
Understanding Melting in Single-Screw Extruders
You can better visualize the melting process by “flipping” the observation point so the barrel appears to be turning clockwise around a stationary screw.