Stainless Steel Range of Cooling Components Extended
Hasco says the expansion helps meet the growing demand for mold cooling applications in the medical and cleanroom fields.
Hasco has extended its cooling range of components in stainless steel across a swath of applications that includes more than 30 product groups, covering hose clips; sealing plugs and diverting bridges; and couplings and connectors, including the Push-Lok range of safety couplings.
Promising reliable cooling of injection molds when using hot or cold water or heat-transfer oil, the components are manufactured entirely from high-quality 1.4305 stainless steel. Hasco says the easily coupled system guarantees reliable, leak-proof and durable temperature control, including for use in clean room environments.
The standard cooling components feature FKM quality seals and can be used at temperatures of up to 150°C (302°F) for water and 200°C (392°F) for oil. Within high-temperature applications in particular, Hasco says the different coefficients of thermal expansion for steel and brass can result in small leaks, which can be avoided by utilizing stainless steel.
Hasco additionally offers stainless steel HT components specifically for the high-temperature range. Equipped with special FKM seals, these offer maximum operating temperatures of 180°C (356°F) for water and up to 220°C (428°F) for oil. The low compression set of the sealing rings is said to guarantee their optimum and safe use under changing operating temperatures. These new stainless steel products are compatible with the standard range, giving molders the opportunity to optimize existing tools by switching from brass to stainless steel.
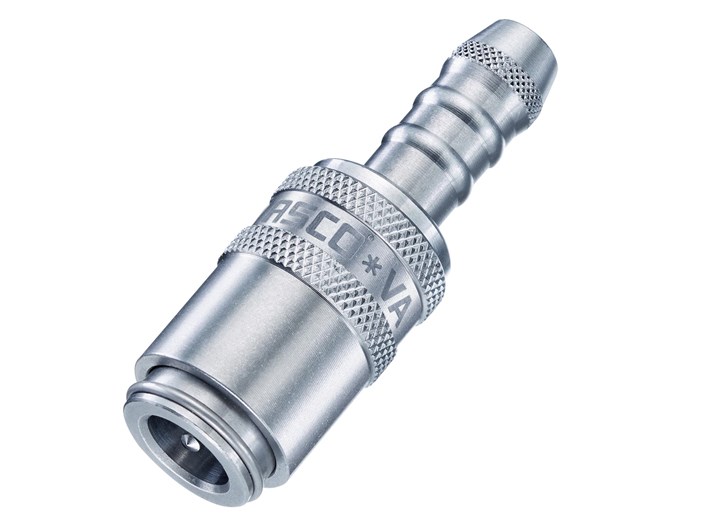
Hasco has extended its stainless steel range of cooling components to support cleanroom applications.
Photo Credit: Hasco
Related Content
-
Where and How to Vent Injection Molds: Part 3
Questioning several “rules of thumb” about venting injection molds.
-
Design Your Tools for Moldability ... and Maintenance
In the initial design phase, when considering the structure and elements of the tool, are you designing them to be maintenance friendly? Canon Virginia has used this approach and preventive maintenance to make tool replacement a thing of the past. You can, too. Here’s how.
-
How to Start a Hot-Runner Mold That Has No Tip Insulators
Here's a method to assist with efficient dark-to-light color changes on hot-runner systems that are hot-tipped.